Testimonials
Trusted by Industry Leaders Worldwide
From medical devices to aerospace systems, our on-demand manufacturing services empower engineers and innovators to bring their ideas to life—faster, with precision they can count on.
- 98.6% on-time delivery rate across 2,000+ global projects
- 4,500+ unique parts manufactured annually with strict quality control
- 50+ countries served with multilingual engineering support
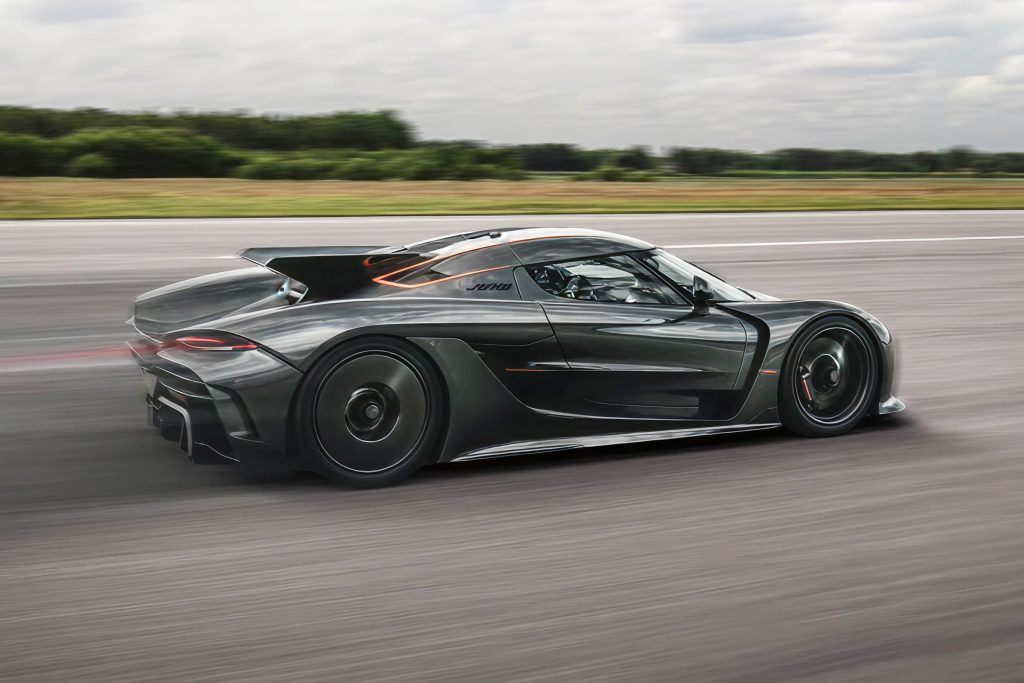
Koenigsegg × Koonze Model
To support Koenigsegg’s pursuit of performance and precision, Koonze Model provided high-tolerance CNC machined components for critical vehicle systems.
Our agile manufacturing process ensured rapid delivery without compromising quality, helping their team accelerate development cycles for next-generation hypercars.
Name
Position , Position
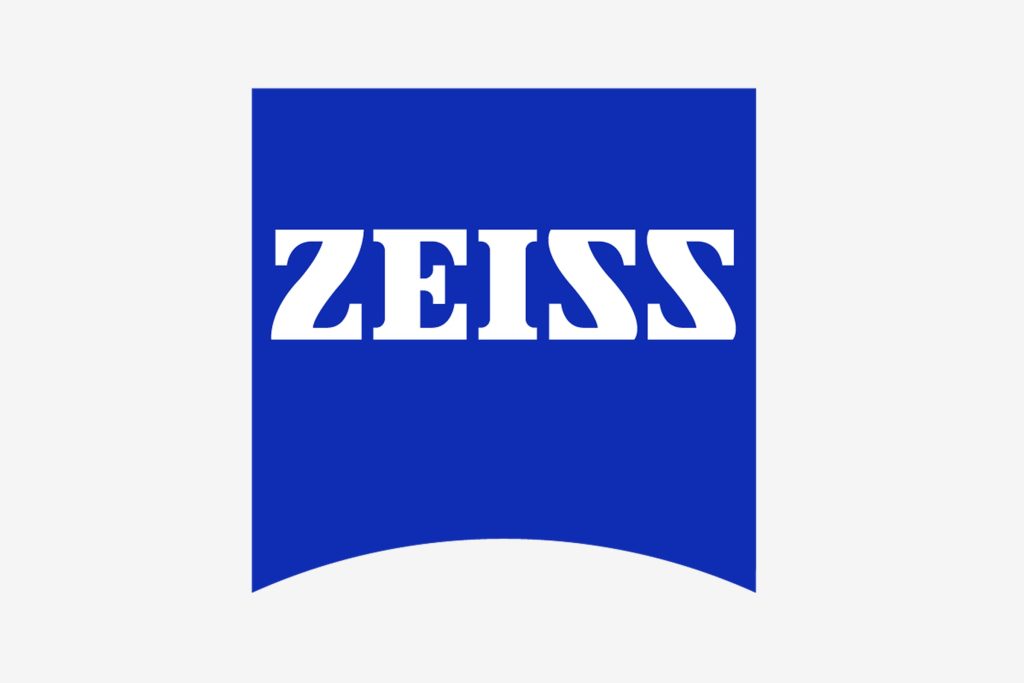
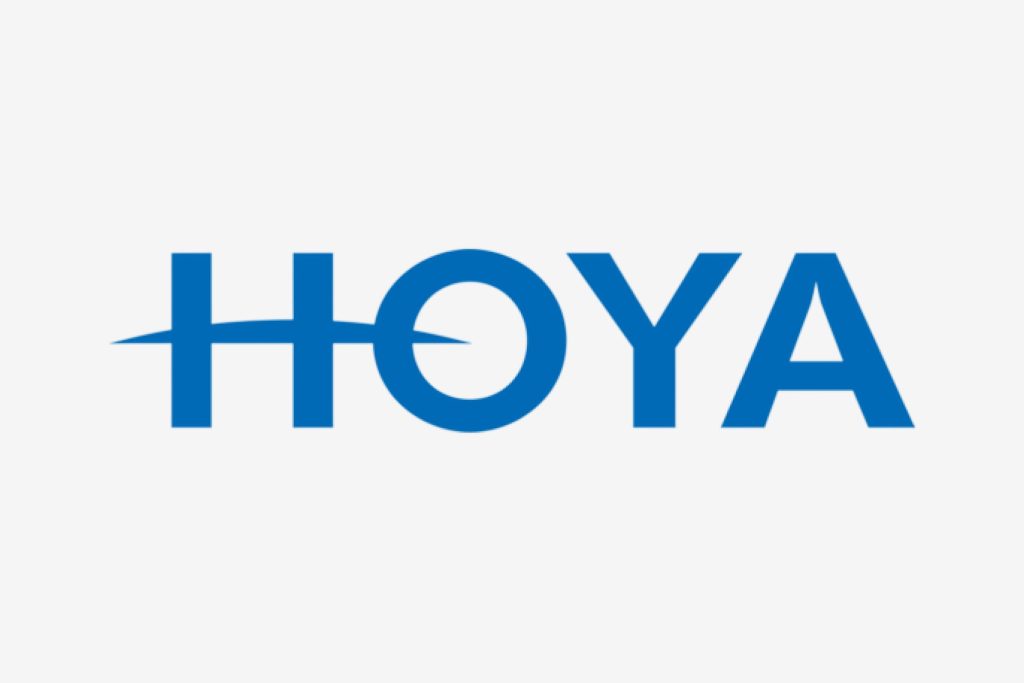
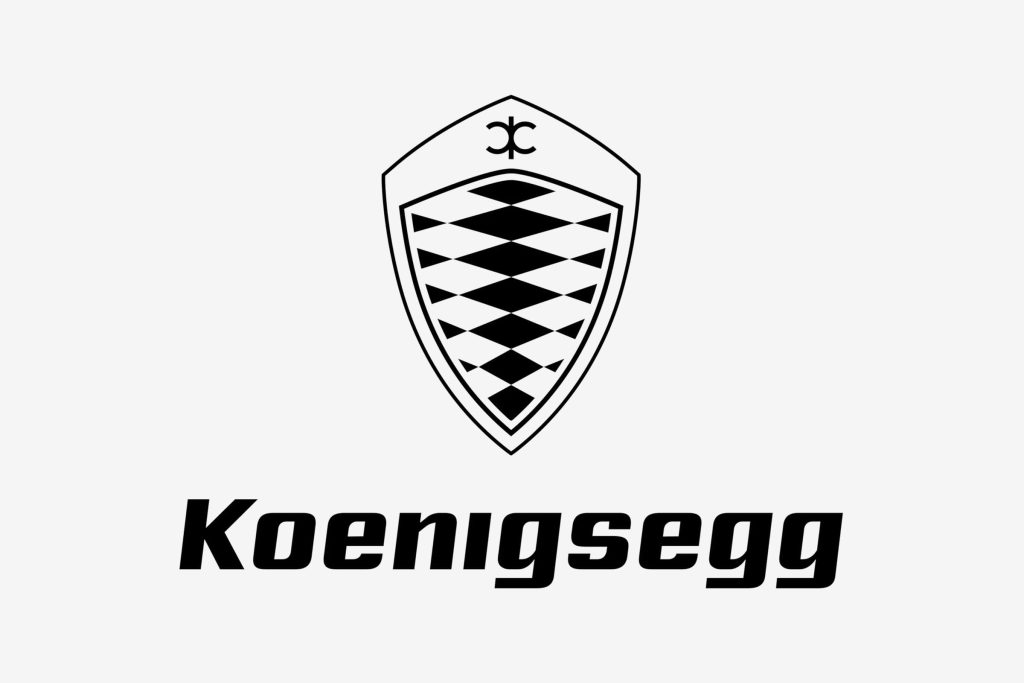
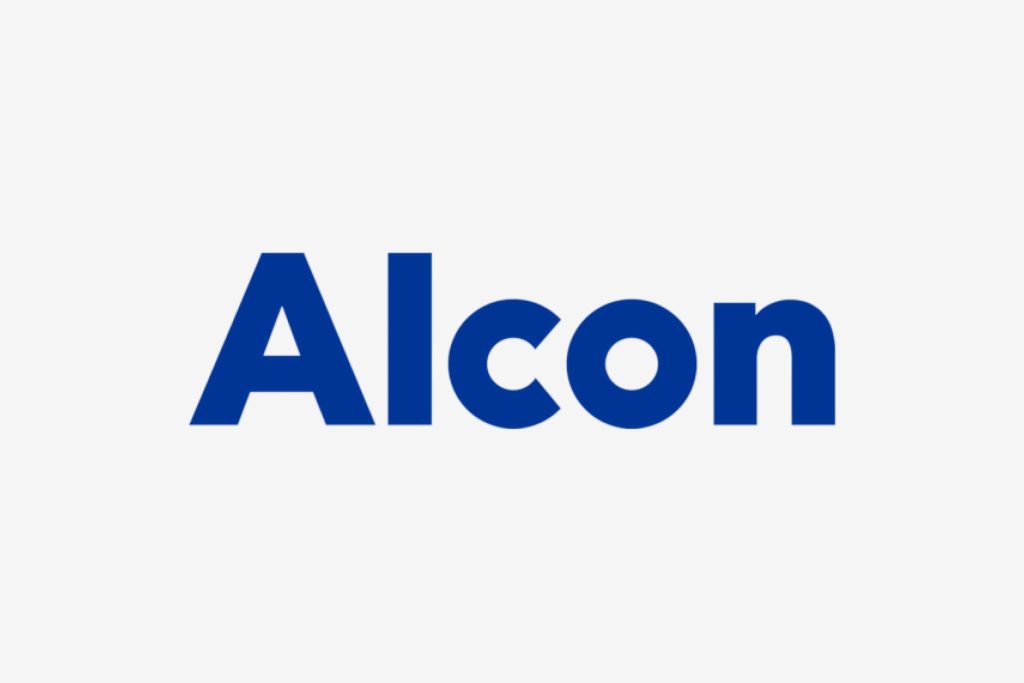
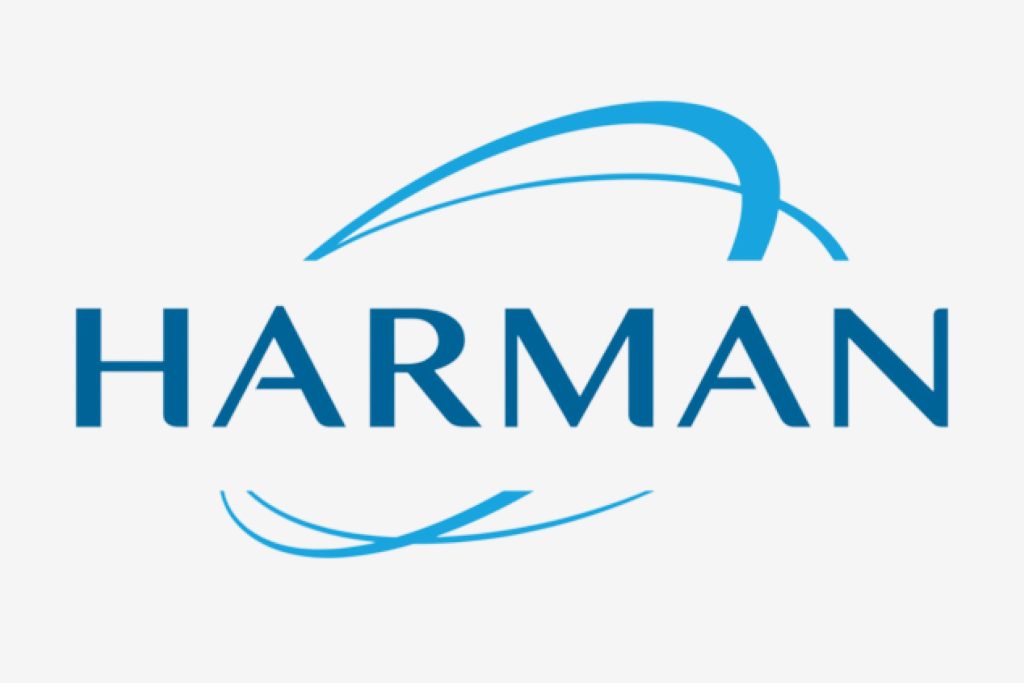
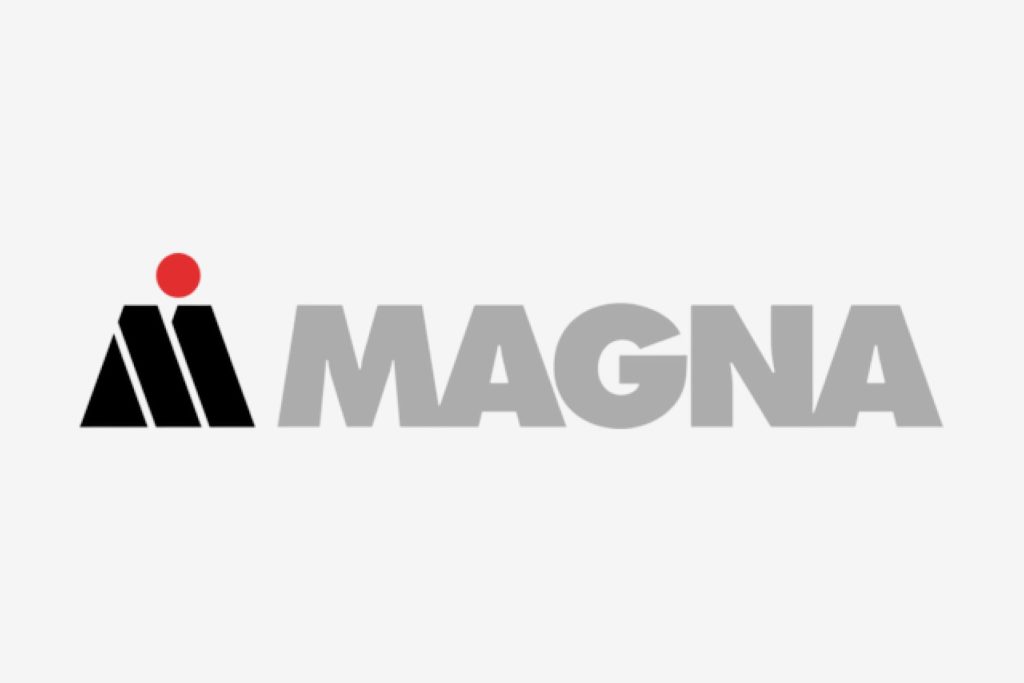
Speed Up Innovation with Functional 3D Prints
Our 3D printing services help product teams accelerate prototyping and design validation. With fast lead times, high resolution, and strong material options, we support everything from early concept models to functional engineering parts.
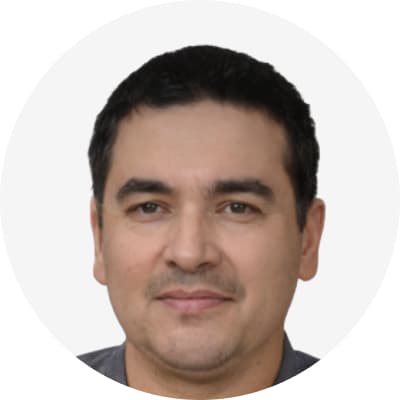
Lucas Meyer
Product Engineer
“We needed a prototype with tight tolerances for airflow testing. Your team printed it in two days, and it performed beautifully during simulations. The resolution and surface finish were far better than what we got from other vendors.”
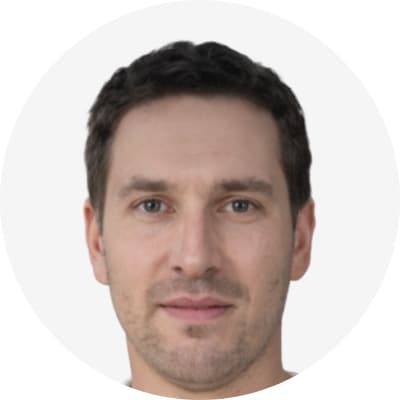
Ava Thompson
Lead Designer
“Thanks to your fast turnaround, we were able to show a working demo at CES without rushing production. The parts were dimensionally accurate and required zero post-processing. Honestly, that saved our product pitch.”
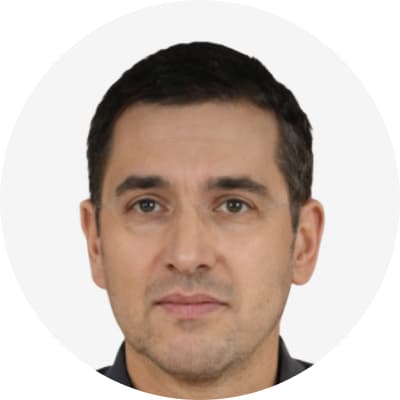
Ethan Cole
Senior Mechanical Designer
“We ran the parts through mechanical stress tests and were surprised at how well they held up. Your team helped us select the right resin, which made a real difference. I appreciated the technical guidance throughout the process.”
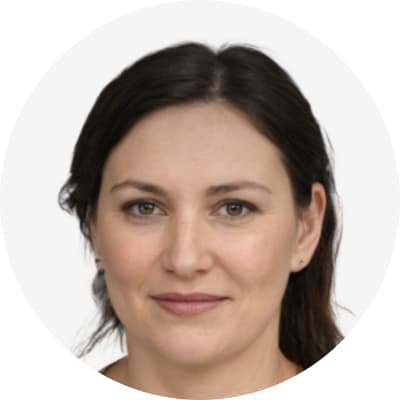
Sophie Bennett
R&D Manager
“We’ve worked with multiple 3D print suppliers, but yours stands out for consistency. Even small, intricate features came out clean and usable. That level of quality really supports our iterative design work.”
Precision You Can Rely On
From aerospace components to custom mechanical parts, our CNC machining service delivers high-precision results with tight tolerances, fast lead times, and full material traceability—ideal for critical applications across demanding industries.
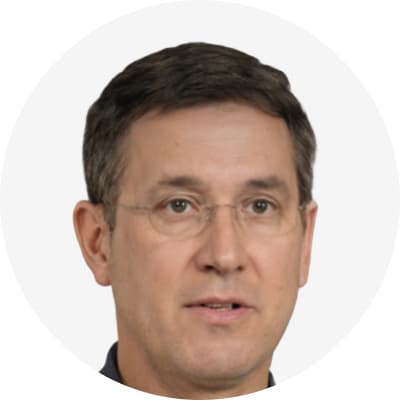
James Carter
Senior Engineer
“We required aluminum housings with ±0.01 mm tolerance, and your team delivered with zero revisions needed. The machining marks were minimal, and every part passed our inspection right out of the box. That level of accuracy saved us days on post-processing.”
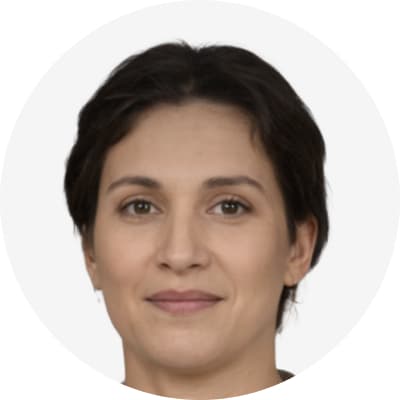
Emily Ross
Quality Manager
“Your inspection report included full CMM data, which helped us get instant QA approval. We especially appreciate the clear communication and willingness to walk us through the DFM suggestions—it made a real impact on cost and performance.”
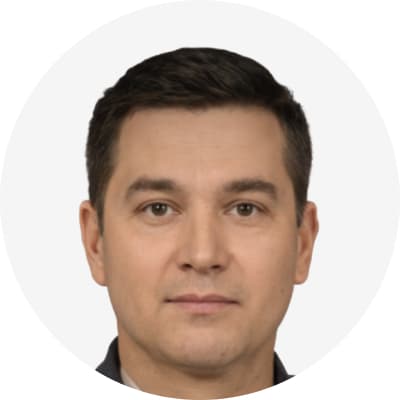
Daniel Wright
Project Lea
“We ran your machined prototypes through thermal cycling and vibration testing, and they held up without any issues. The consistency between parts was impressive—even for a low-volume run. It’s clear your shop knows precision manufacturing.”
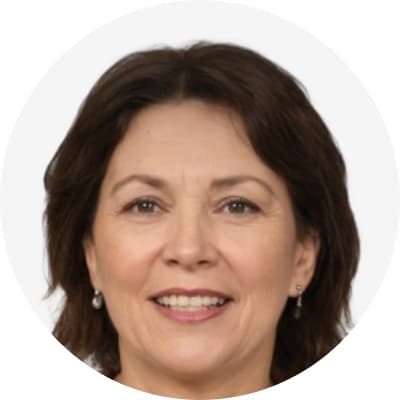
Olivia Hayes
Strategic Sourcing Director
“These stainless steel brackets were part of a defense-grade assembly, so we couldn’t afford dimensional drift. Your team delivered exact fits on every part, with proper certification and traceability. Definitely among the most reliable suppliers we’ve worked with.”
Scalable Parts with Repeatable Quality
Our injection molding service supports high-volume production with tight tolerances and consistent quality. From rapid tooling to full production runs, we help brands launch parts faster and more reliably.
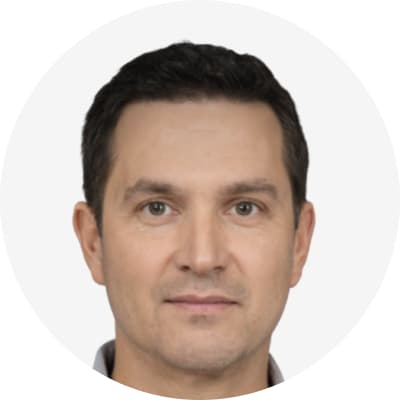
Andrew Miller
Procurement Manager
“We were up against a tight deadline to produce 5,000 ABS casings for a product launch. Your team helped us optimize the mold design and delivered flawless parts—no flashing, no warping. The whole process was surprisingly smooth.”

Natalie Perez
Senior Product Engineer
“You turned our complex multi-cavity mold around faster than any other vendor we’ve used. The parts came out clean and uniform, with great consistency across batches. Plus, your material advice was spot on for strength and finish.”
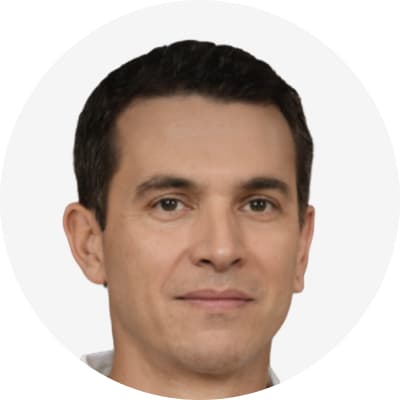
Mark Stevens
R&D Director
“Our team needed overmolded parts combining soft TPE and rigid PC. The result from your shop was excellent—the bonding was solid, and there were no alignment issues. You clearly understand multi-material molding at a technical level.”
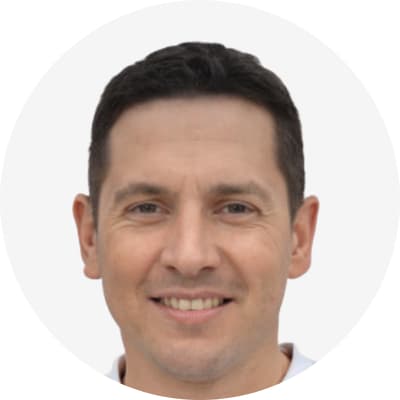
Rachel Kim
Operations Lead
“The first article approval process was fast, and you were very responsive to design tweaks. Once we locked in the mold, the production just kept running smoothly. Your reliability helped us avoid a costly delay in our supply chain.”
Custom Metal Parts with Industrial-Grade Precision
From enclosures to brackets, our sheet metal services offer flexible and precise fabrication with fast turnarounds. Ideal for prototypes and low-volume production, with support for multiple materials and finishes.
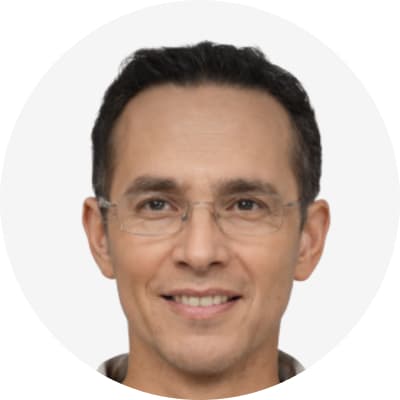
Benjamin Scott
Hardware Engineer
“We needed custom stainless steel enclosures with a brushed finish for an industrial panel. The bending, cutouts, and surface treatment were all perfect. You even managed to reduce sharp edges without us asking—impressive attention to detail.”
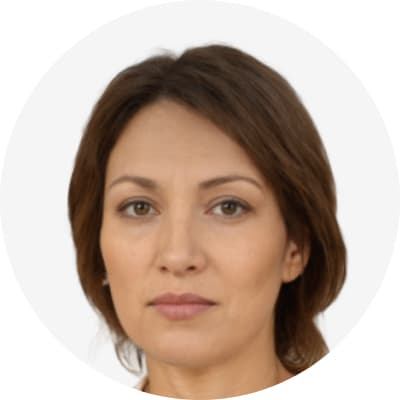
Laura King
Design Engineer
“Our prototype was unusually complex with multiple bends and tabs, but you handled it like it was standard. The parts arrived exactly to spec, and your tolerance control saved us time during assembly. We’ll definitely be ordering the production batch soon.”
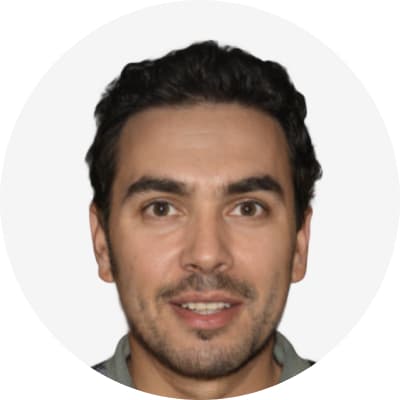
Tyler Monroe
Project Engineer
“We were impressed by how fast you delivered 100+ aluminum brackets, each one identical and burr-free. Your team flagged a design issue before cutting and suggested a more stable flange—small things that made a big difference downstream.”
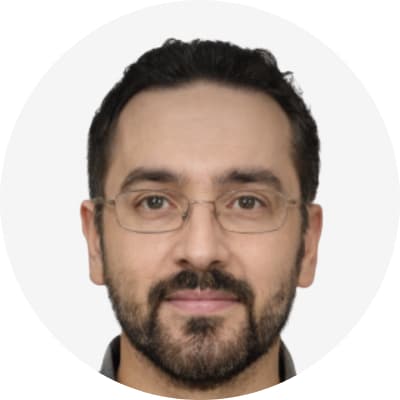
Hannah Lewis
Mechanical Program Manager
“This was our first time outsourcing sheet metal work, and we were cautious. But your process was transparent, fast, and the results speak for themselves. The anodized finish came out clean, and the parts fit right into our test rig.”
Hear What Clients from Every Industry Are Saying
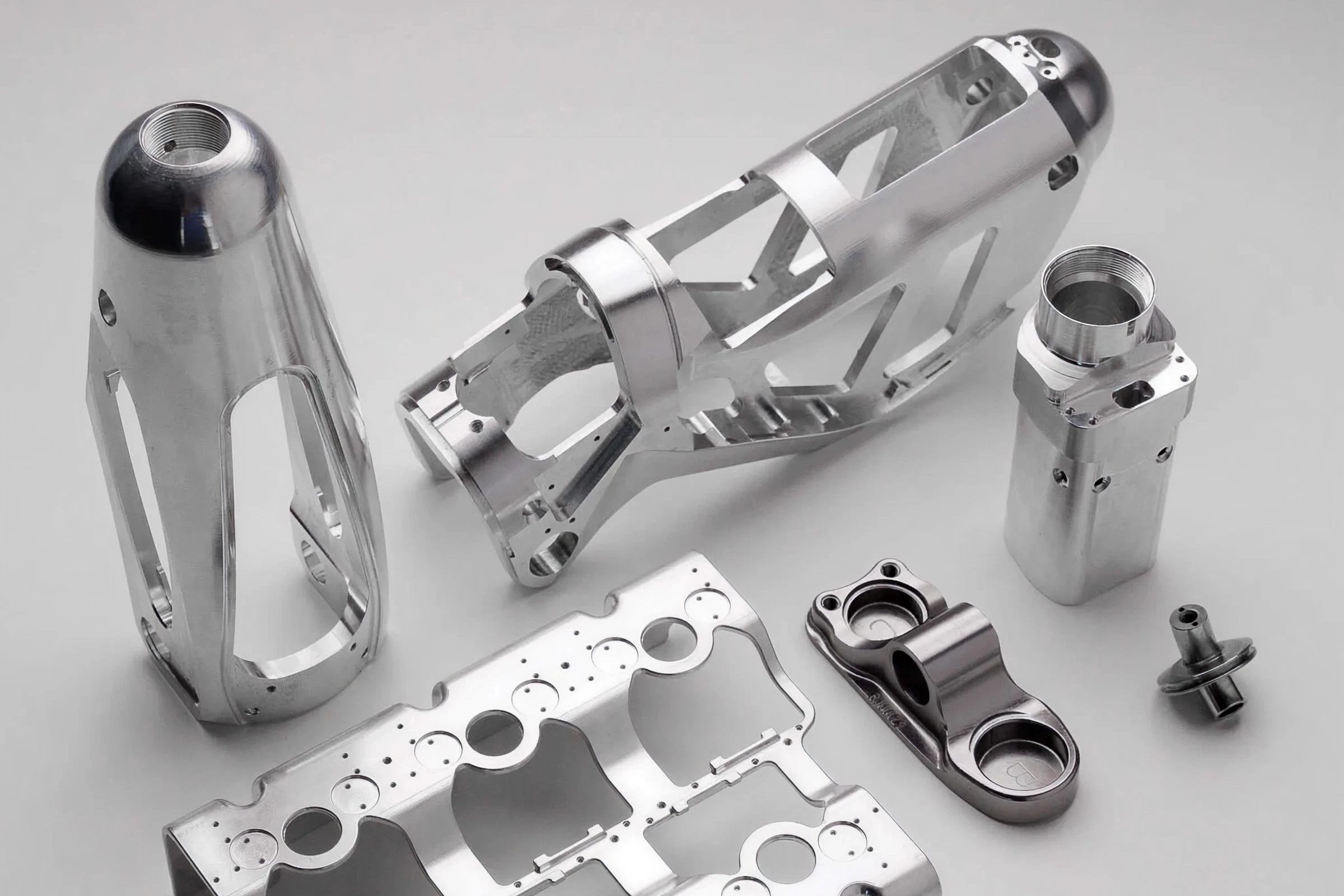
“We needed Class II device components with tight dimensional accuracy and biocompatible materials. Your team delivered clean, burr-free CNC parts with full inspection data. That level of quality and documentation made our FDA submission smoother.”
— Dr. Alan Rhodes, QA Director
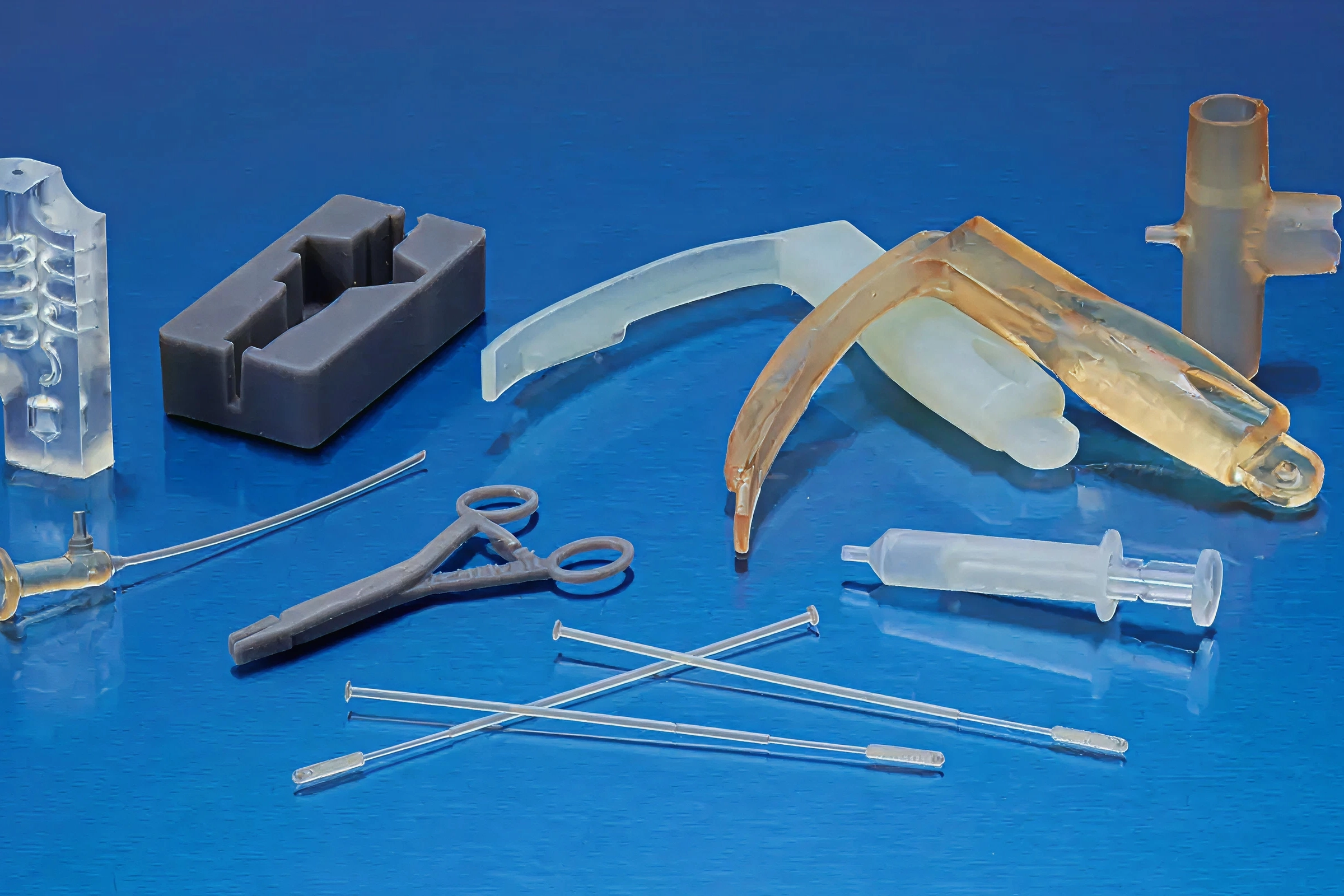
“Koonze Model helped us iterate on multiple design revisions quickly. The 3D printed prototypes were precise, and the communication with their engineering team was seamless. This speed really accelerated our bench testing phase.”
— Emily Zhang, R&D Engineer
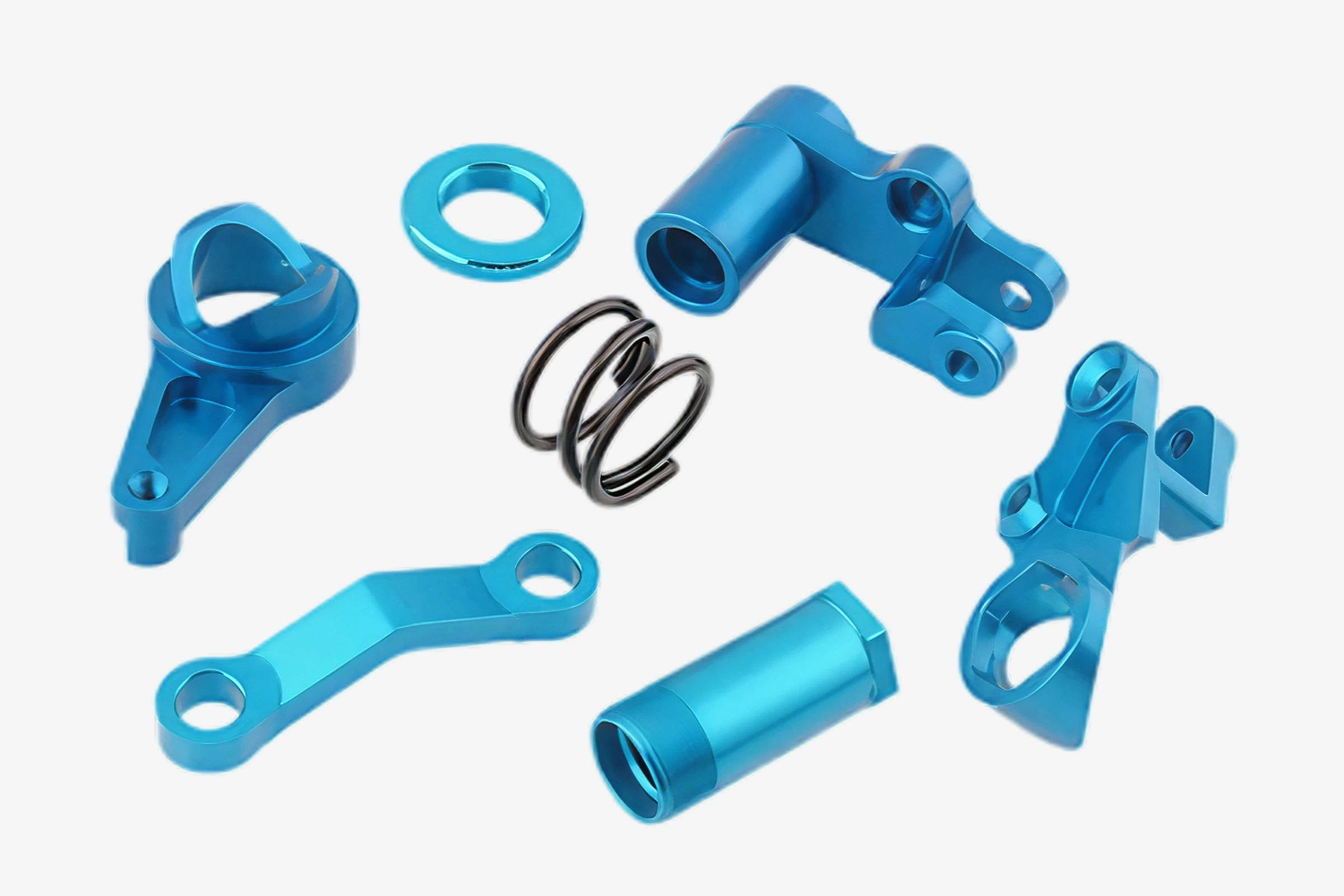
“Our surgical tool housings required both high strength and flawless surface finishing. Koonze delivered anodized aluminum parts that looked production-ready. Their attention to detail helped us go from concept to pilot run in record time.”
— Michael Tran, Product Development Manager
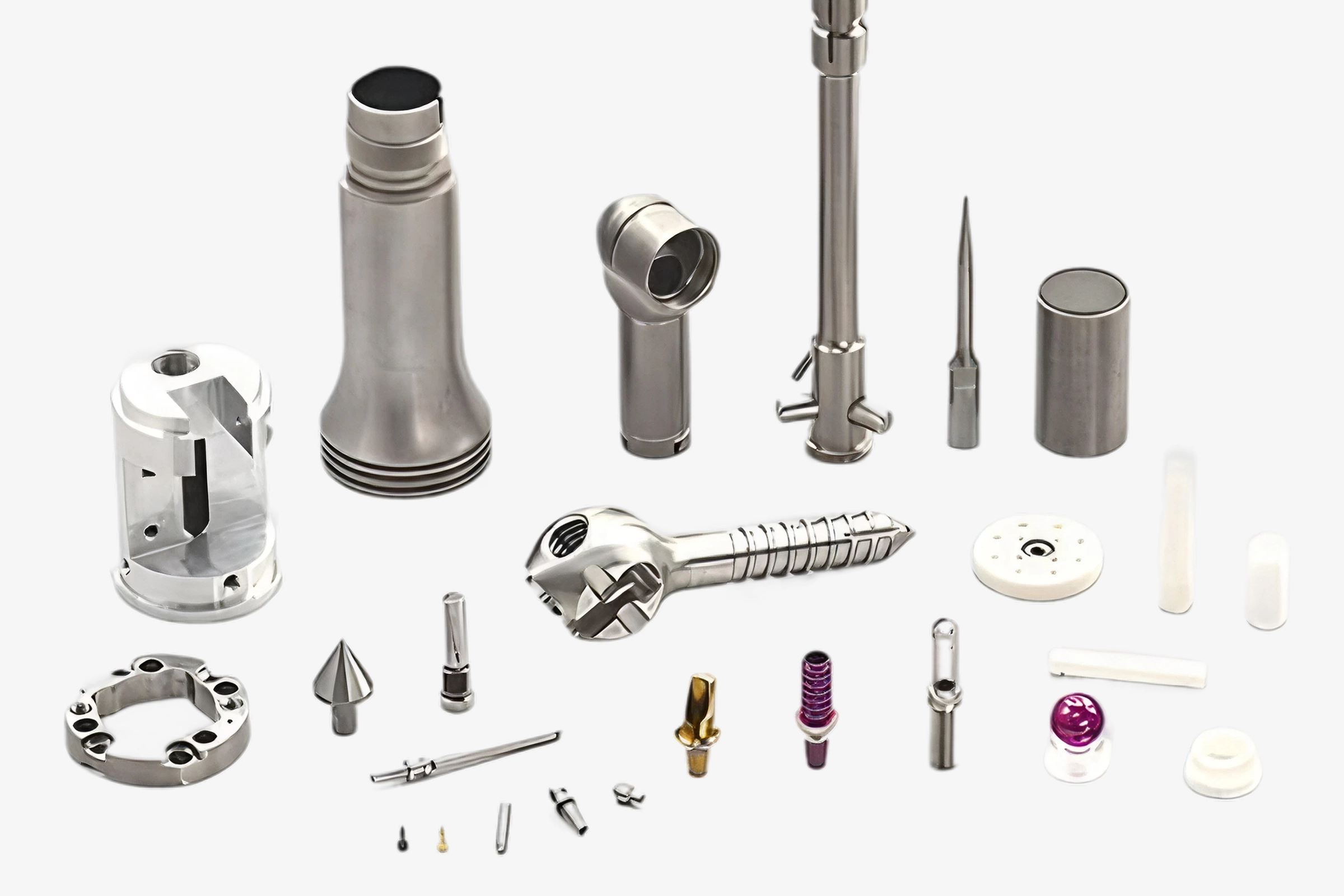
“We had strict ISO 13485 requirements and needed full traceability for a batch of machined parts. Koonze provided complete documentation, material certs, and inspection reports without us needing to ask twice. That reliability makes them a long-term partner.”
— Laura Kim, Supply Chain Lead
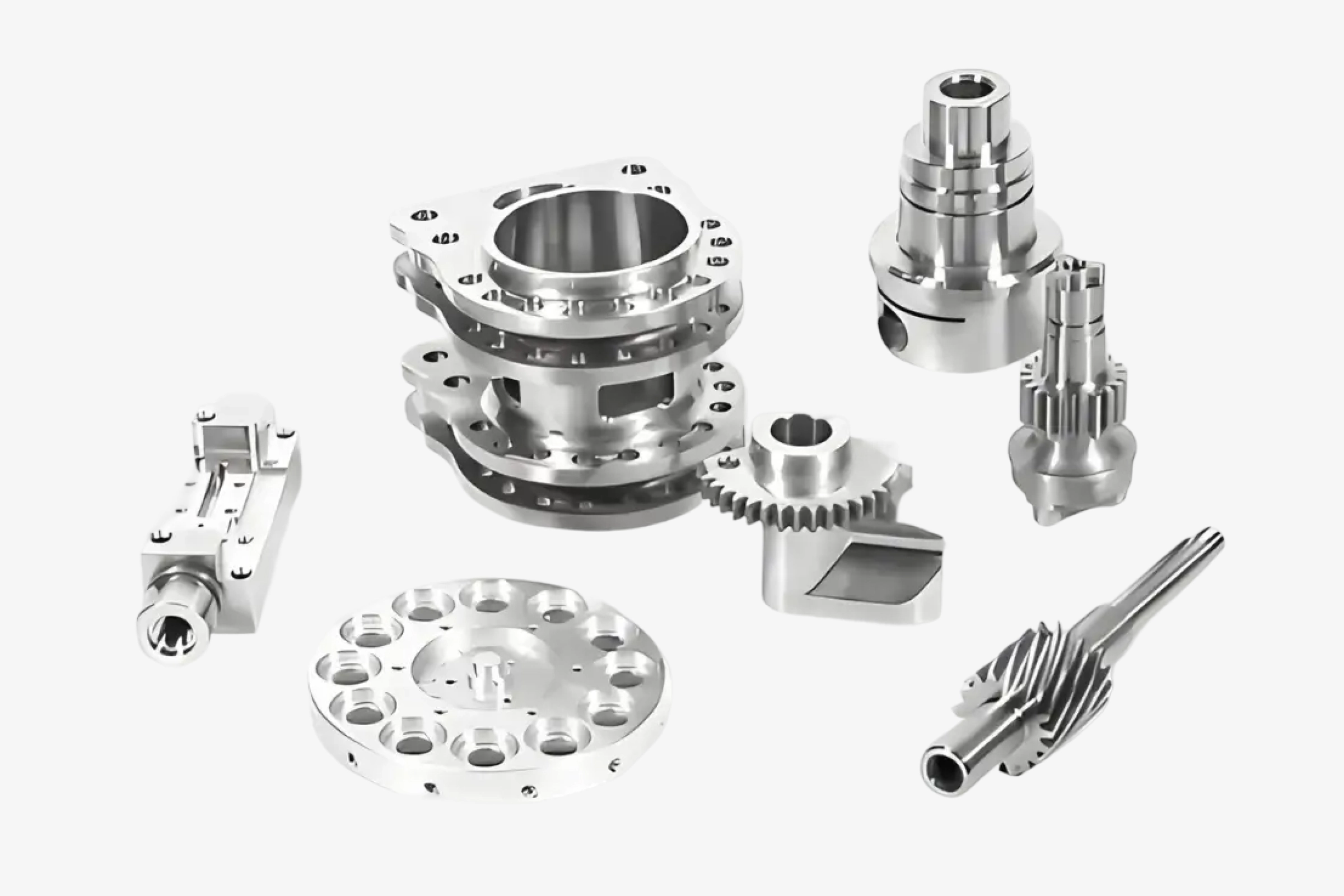
“We needed rapid CNC samples for EV powertrain components. Koonze delivered precise aluminum parts within a week, complete with CMM reports. Their speed and accuracy kept our test schedule on track.”
— Lars M., Mechanical Engineer
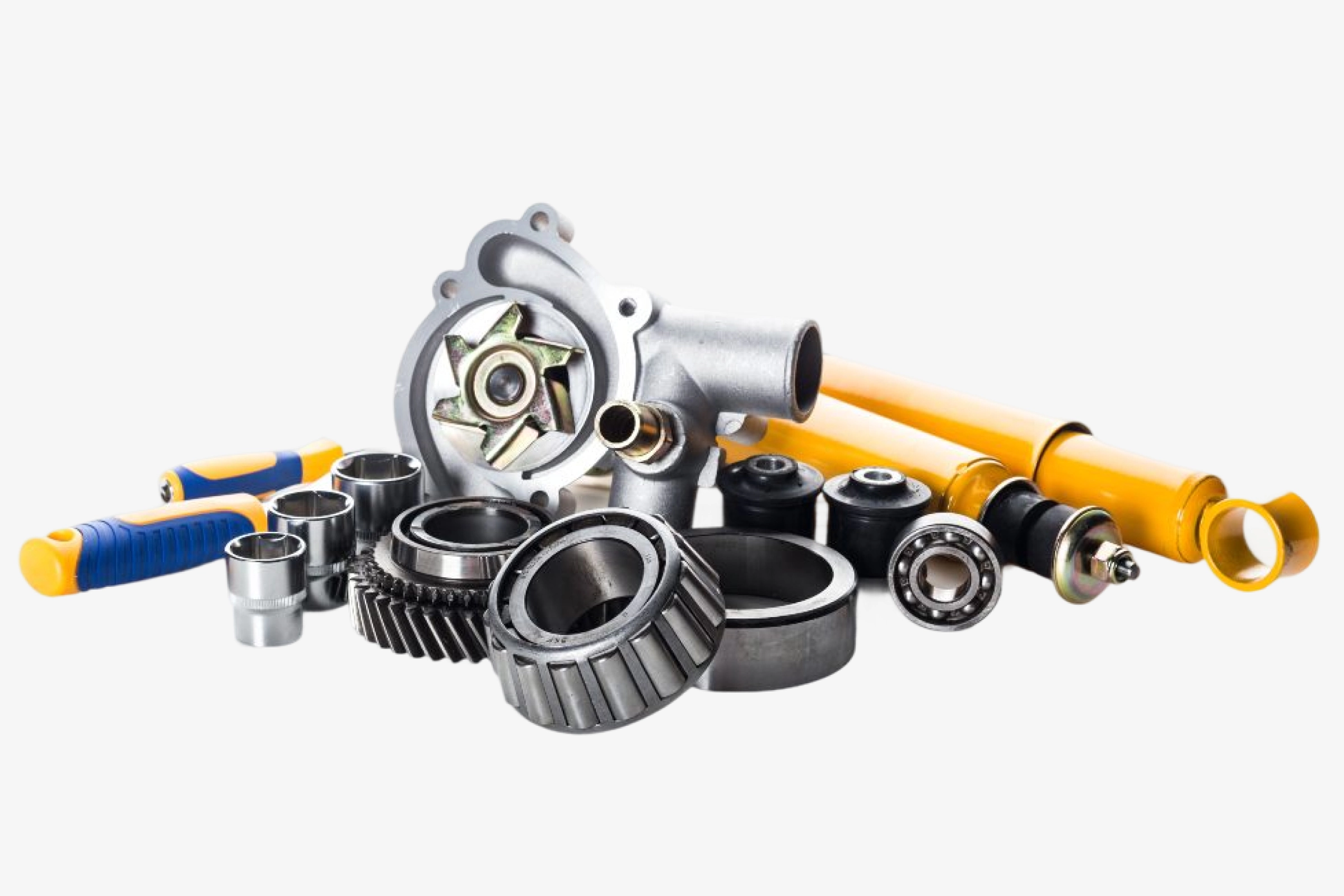
“Koonze’s ability to handle tight tolerances and complex geometries made them our go-to partner for small-batch automotive tooling. Communication was fast and technical.”
— Rachel Lee, Purchasing Lead
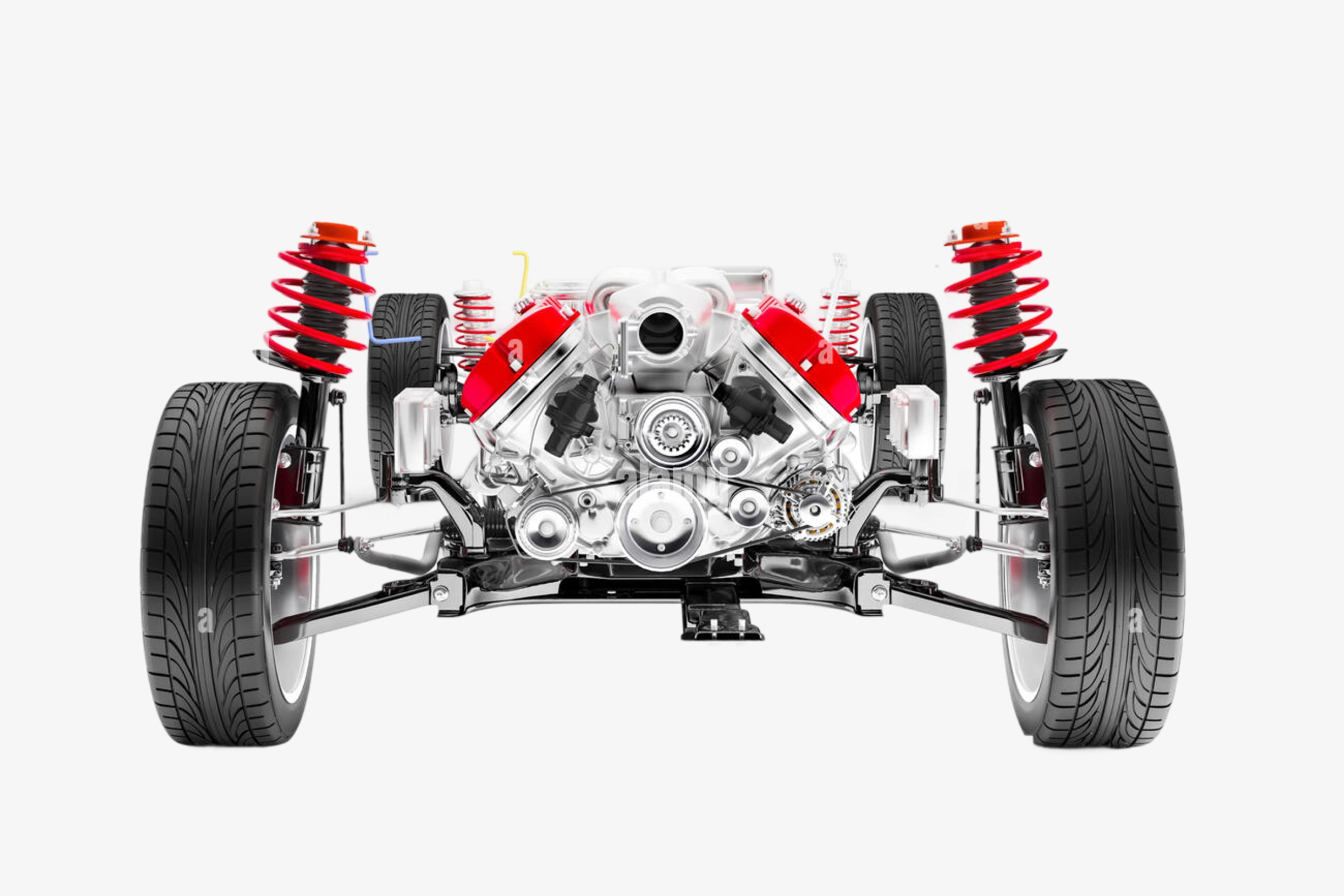
“Our under-the-hood parts required heat resistance and tight fits. The parts from Koonze passed all functional tests without rework. That saved us both time and cost.”
— Carlos Rivera, Program Manager
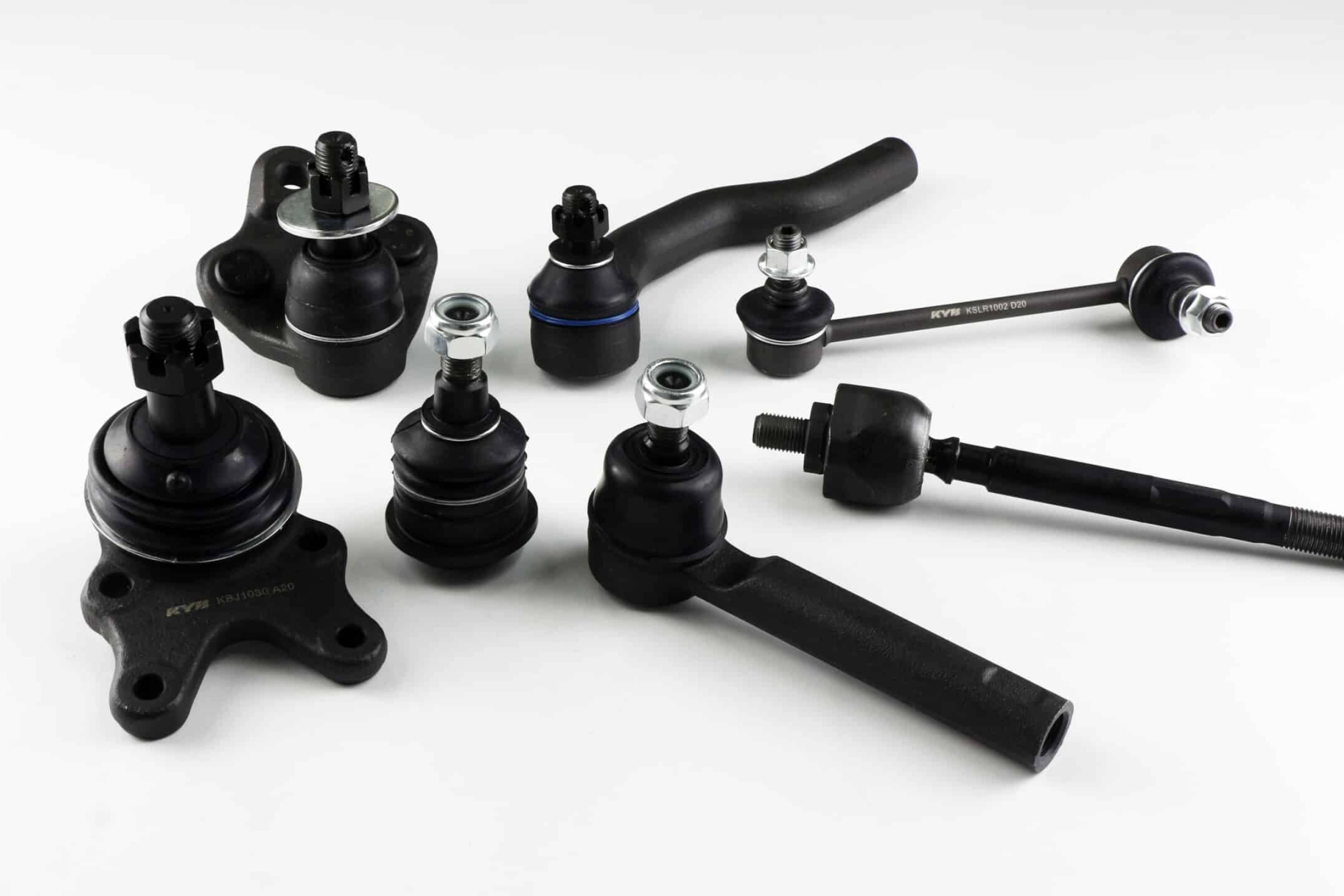
“We used Koonze for early-stage prototyping of a steering module. Their feedback on DFM helped us reduce machining costs by 30% before tooling.”
— Akira Tanaka, Design Engineer
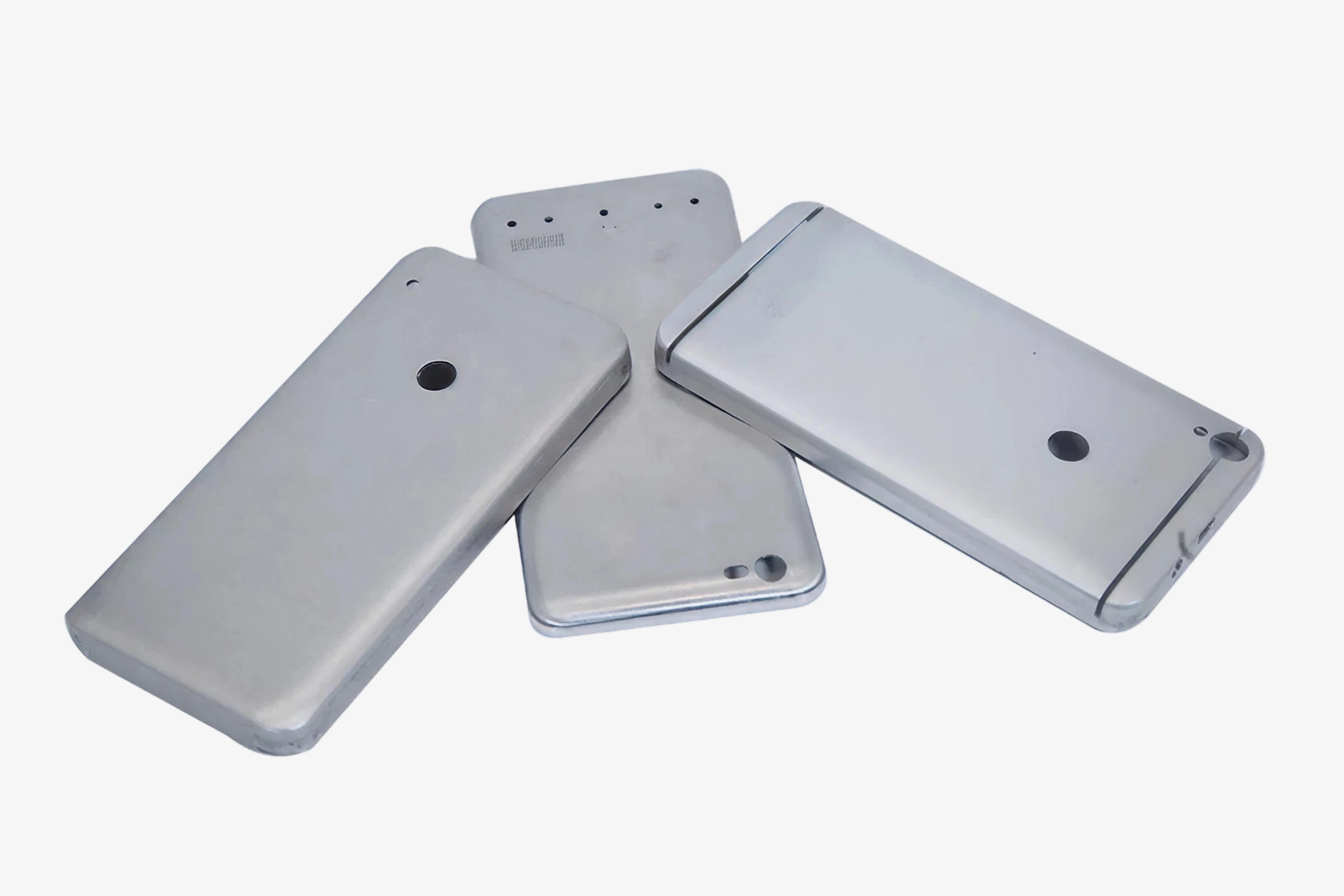
“We needed tight cosmetic standards for our smartwatch enclosures. Koonze delivered polished CNC parts that looked ready for launch. Zero visible tool marks.”
— Melissa Chang, Industrial Designer
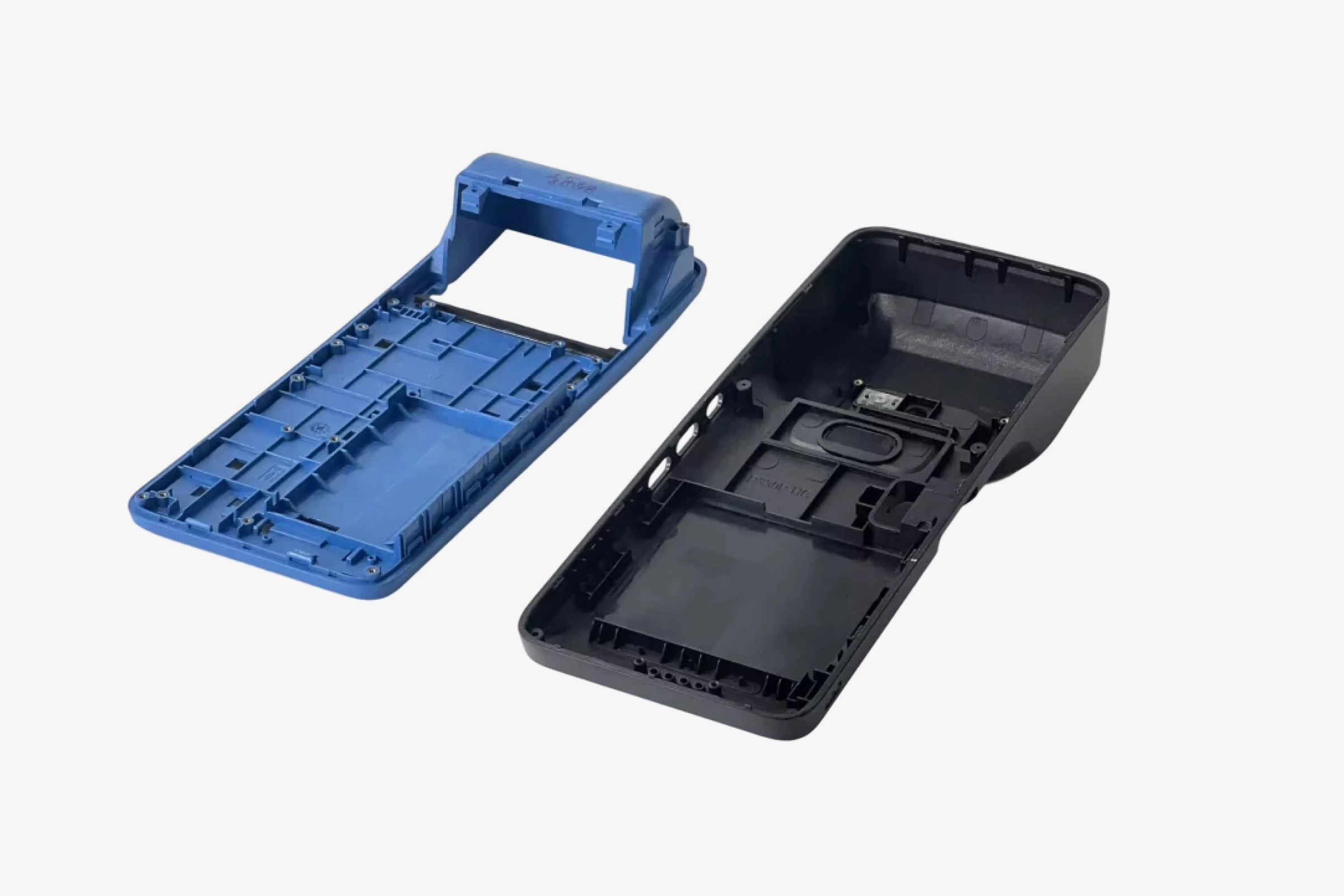
“Quick turnaround was critical for our launch schedule. Koonze hit our 5-day deadline with consistent quality across all units.”
— Jinwoo Park, Hardware PM
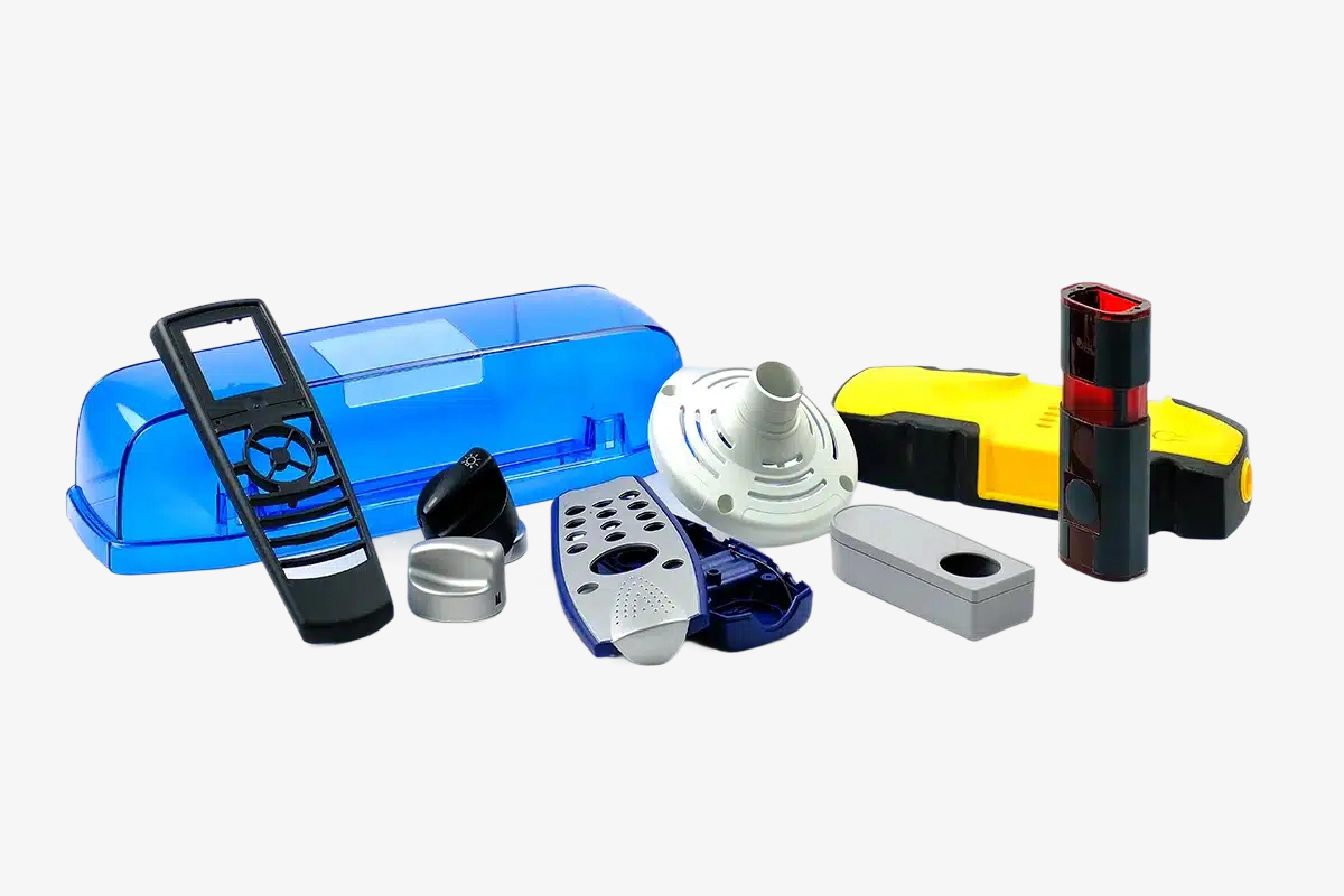
“We had complex plastic housings that needed functional testing before injection molding. Koonze’s prototypes felt close to final production—very helpful for user testing.”
— Sandra Liu, UX Researcher
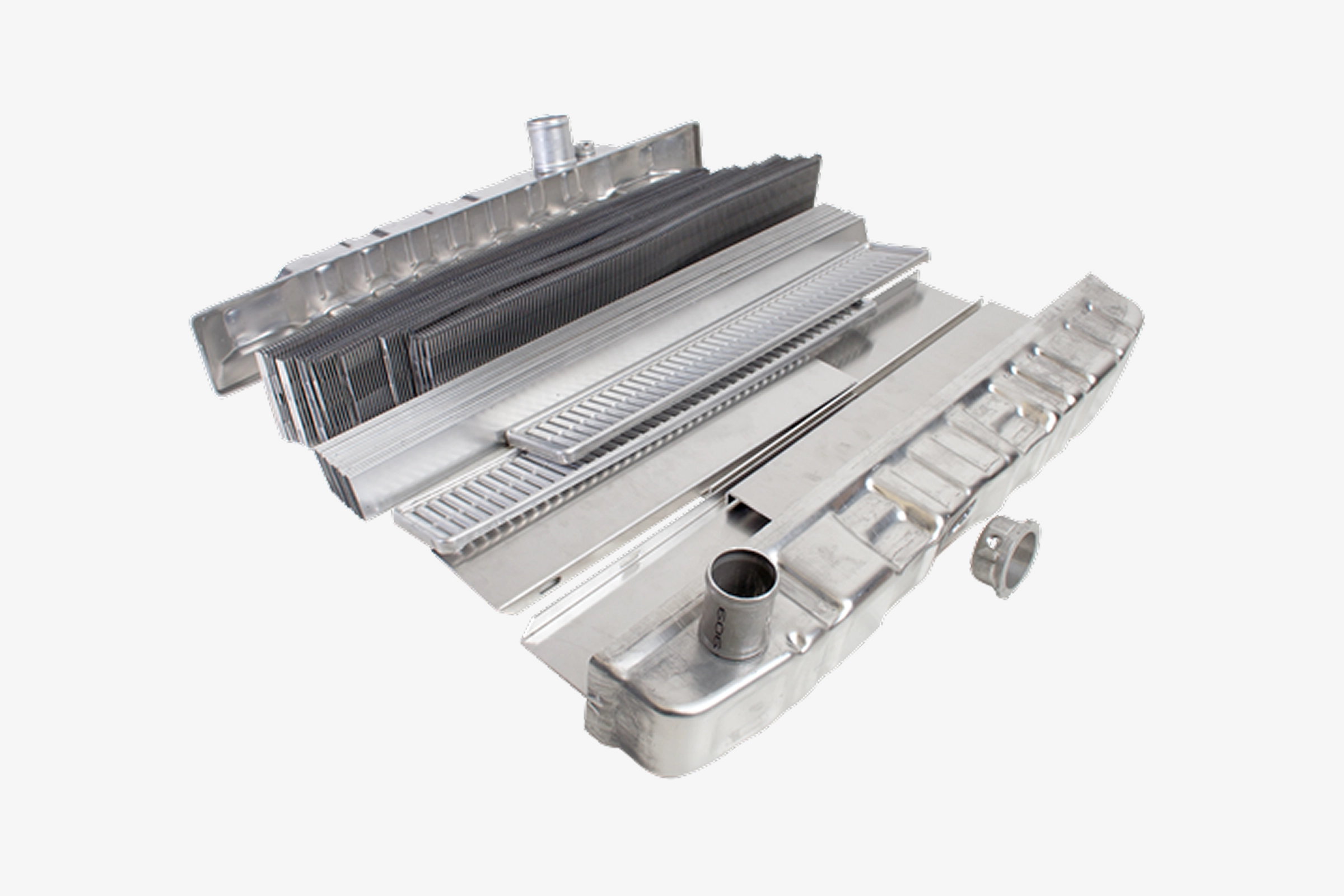
“Their team was proactive in suggesting ways to improve heat dissipation in our aluminum heat sink design. That insight made a real impact.”
— Eric Ng, Product Engineer
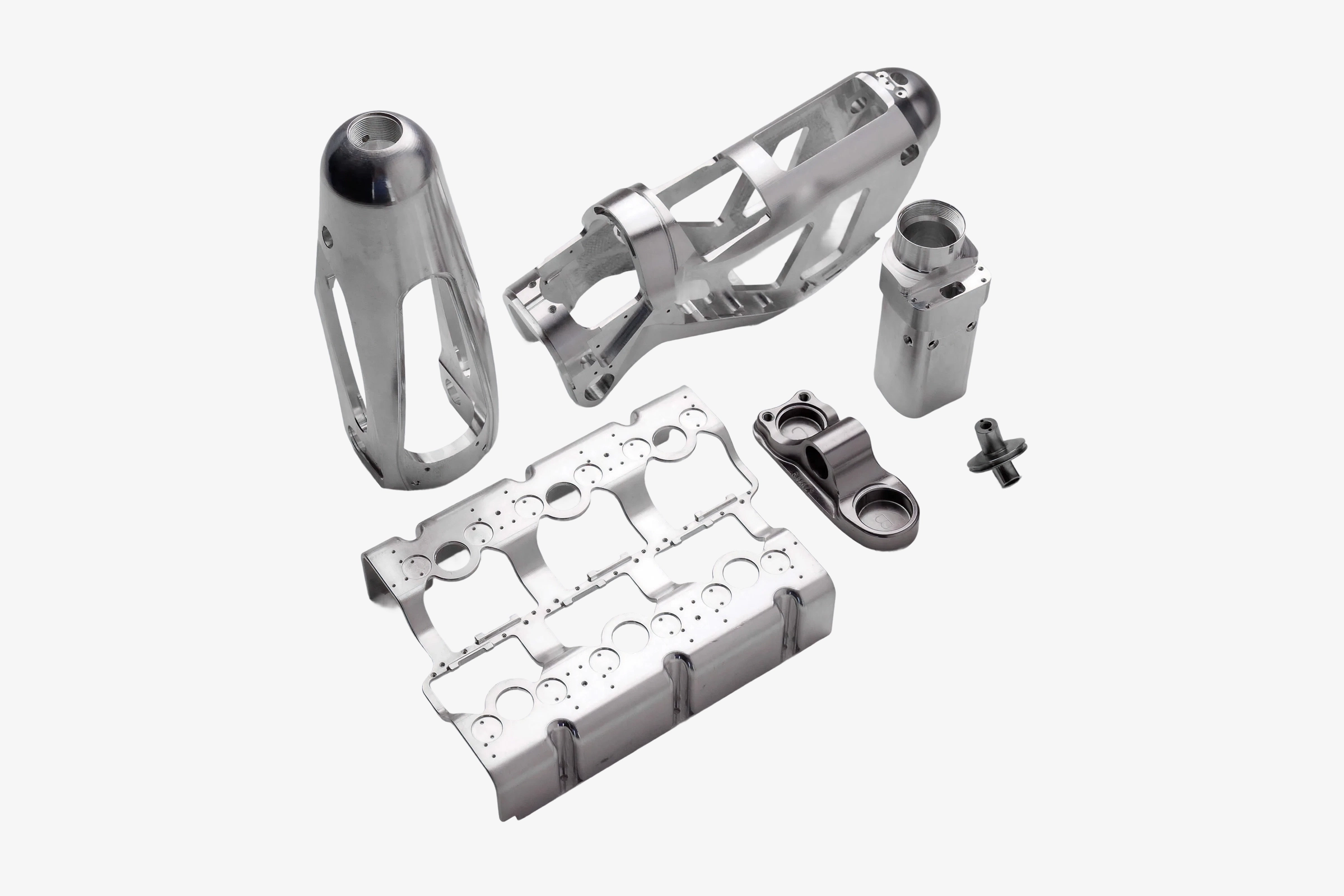
“Flight-ready components require traceability and consistency. Koonze provided full certs and flawless parts—no deviations, no delays.”
— John Becker, QA Manager
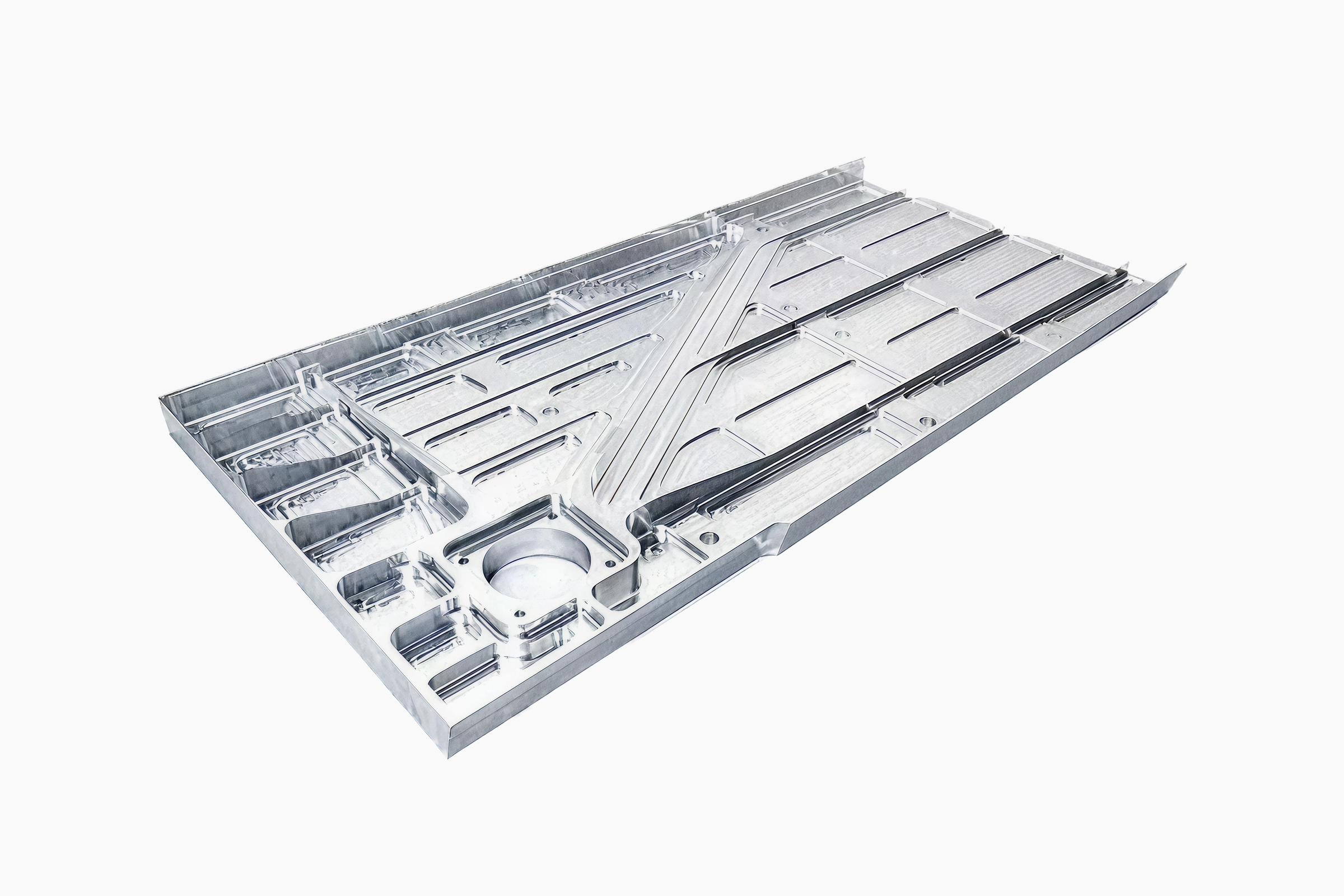
“We used their 5-axis machining capabilities for a complex bracket. The precision and finishing exceeded our expectations.”
— Feng Li, Aerospace Design Lead
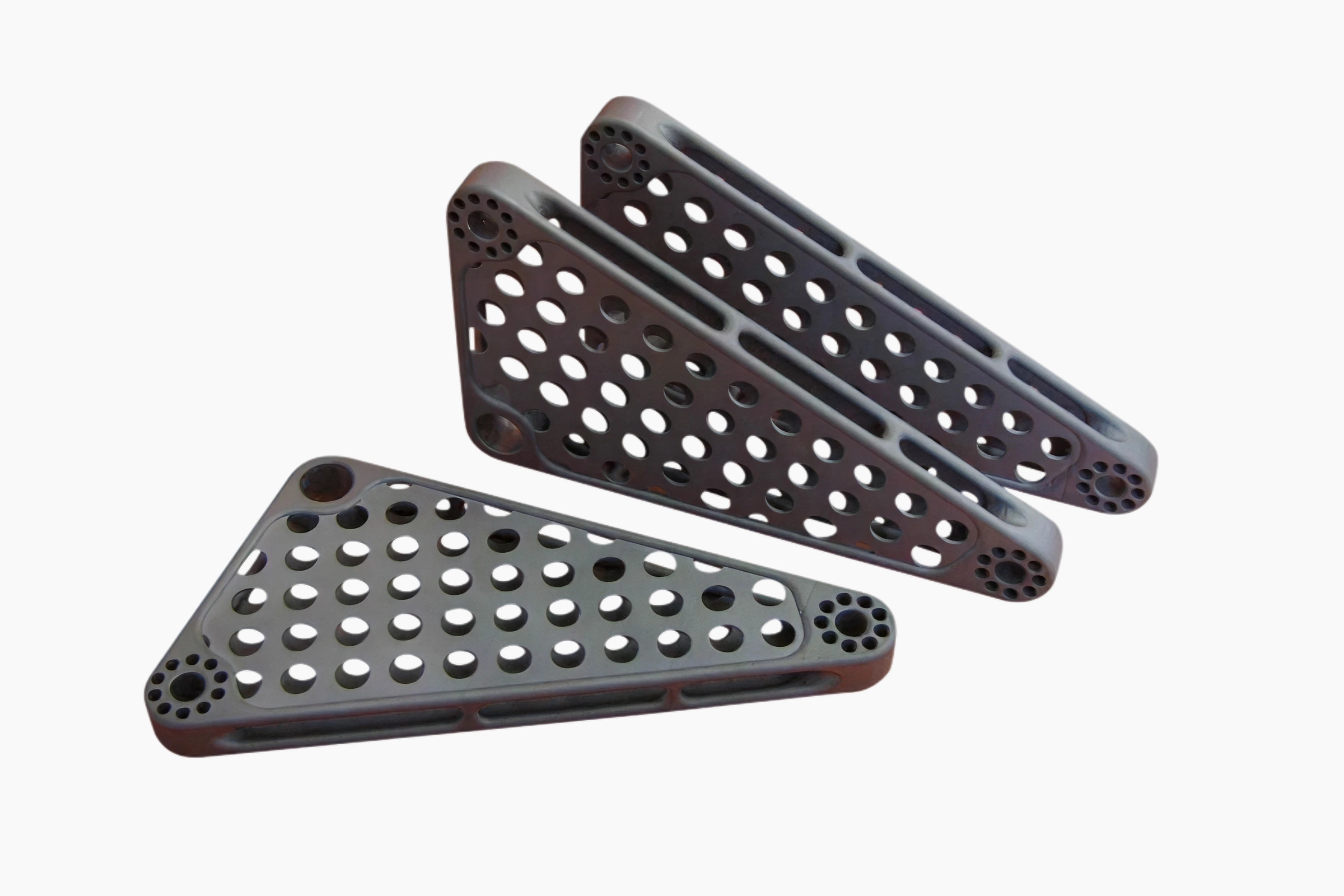
“Koonze delivered titanium parts for a structural test in just 7 days. That responsiveness is hard to find in aerospace manufacturing.”
— Isabel Grant, Technical Buyer

“Their team helped us revise a part design to reduce weight without sacrificing strength. That kind of insight is invaluable.”
— Tyler Nash, Flight Systems Engineer
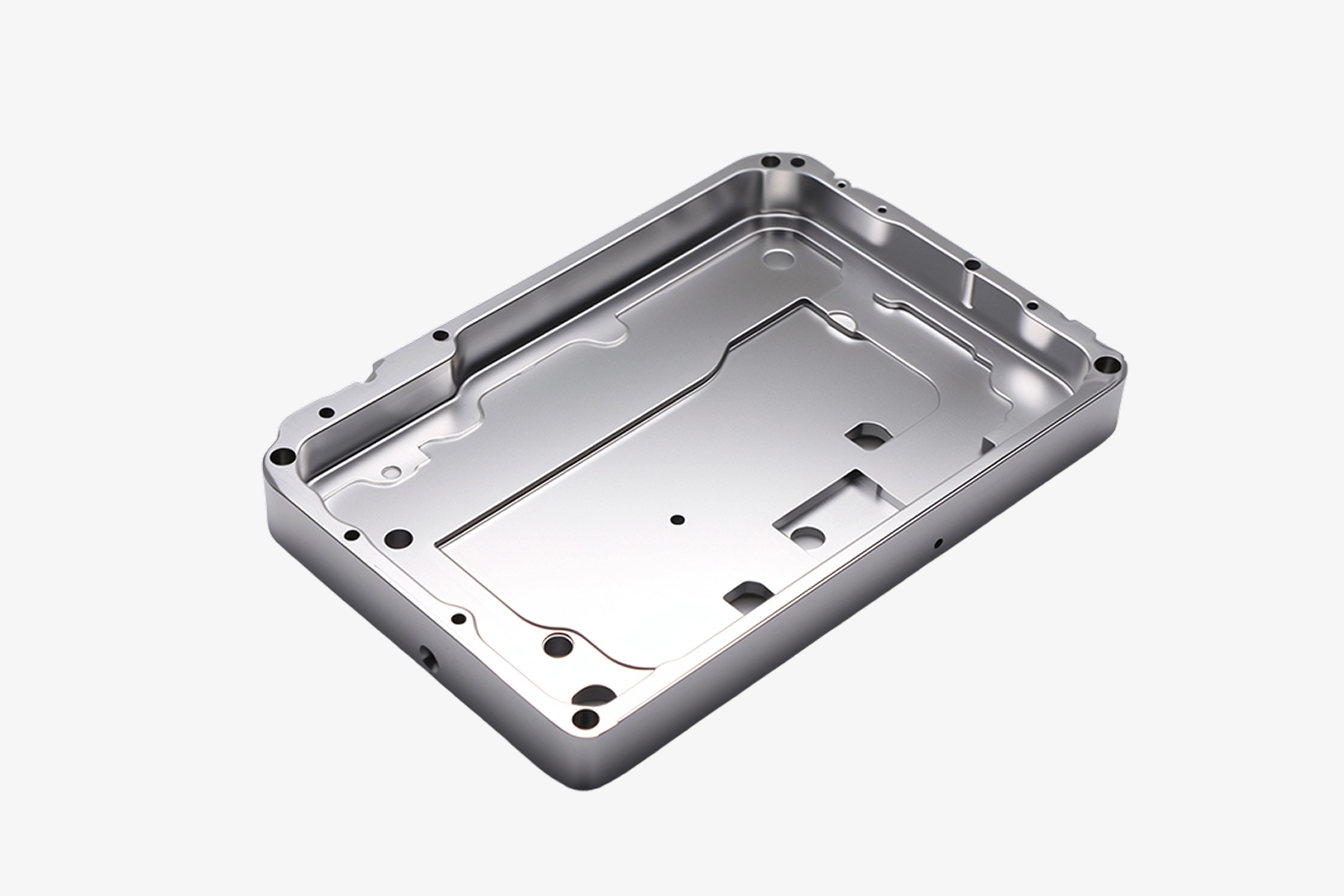
“We needed high-precision enclosures with EMI shielding features. Koonze delivered CNC parts that passed all fit and interference tests.”
— Omar N., Hardware Engineer
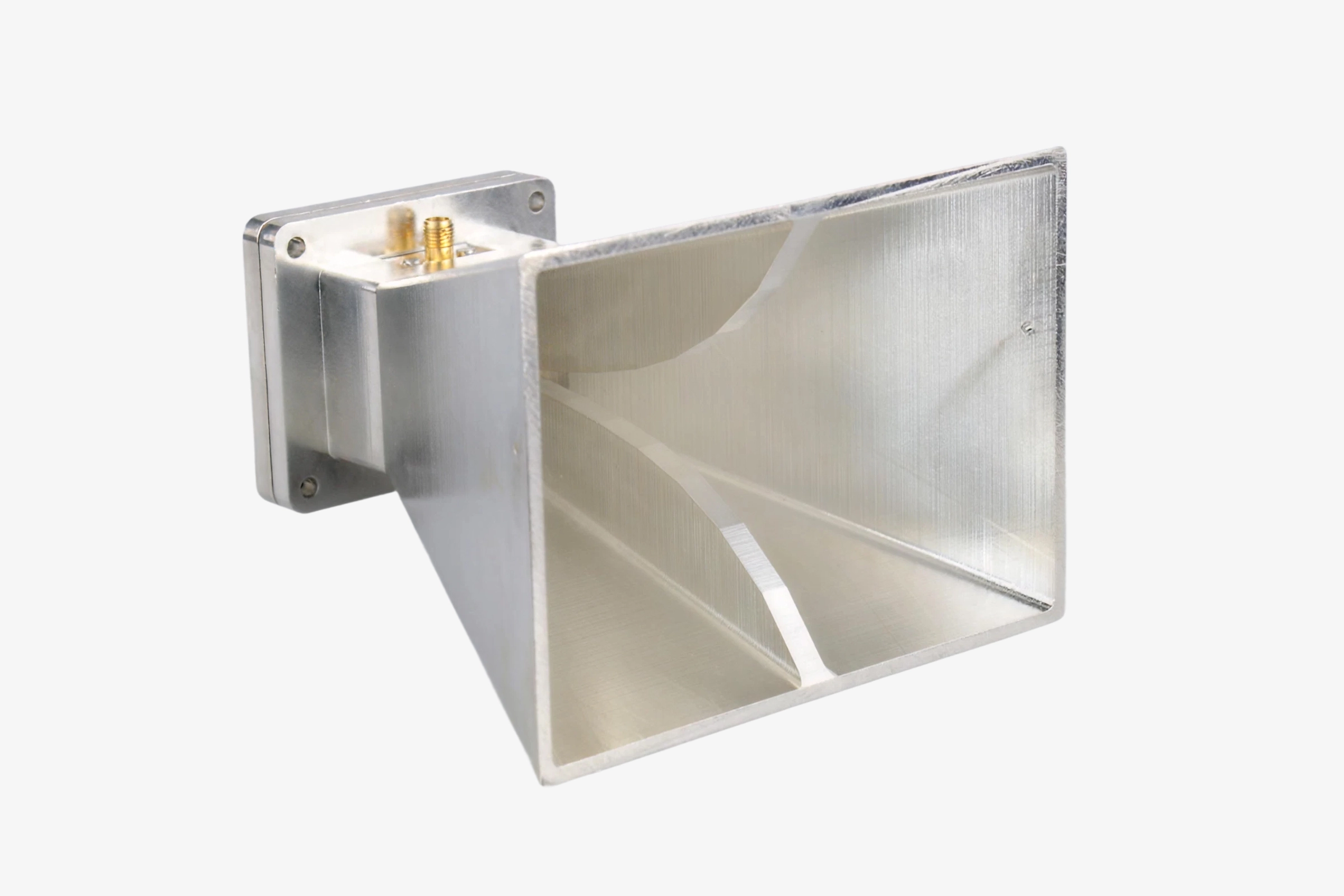
“Turnaround and consistency were critical for our antenna prototypes. Koonze nailed both, even under a tight deadline.”
— Lucy Pang, Program Lead
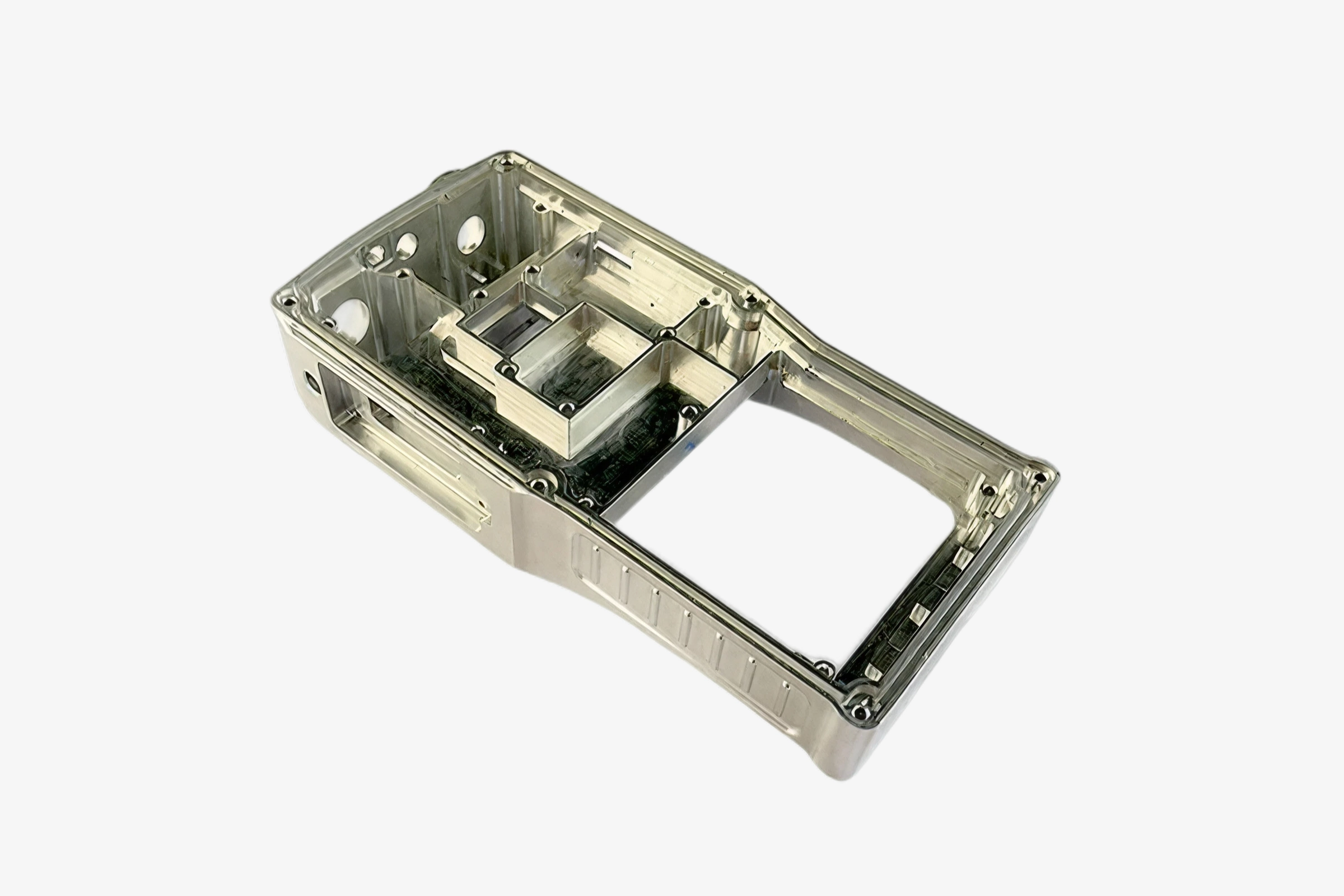
“Their engineers understood the thermal and shielding constraints of our system. That technical input helped us avoid costly redesigns.”
— Nathan Lee, Systems Engineer
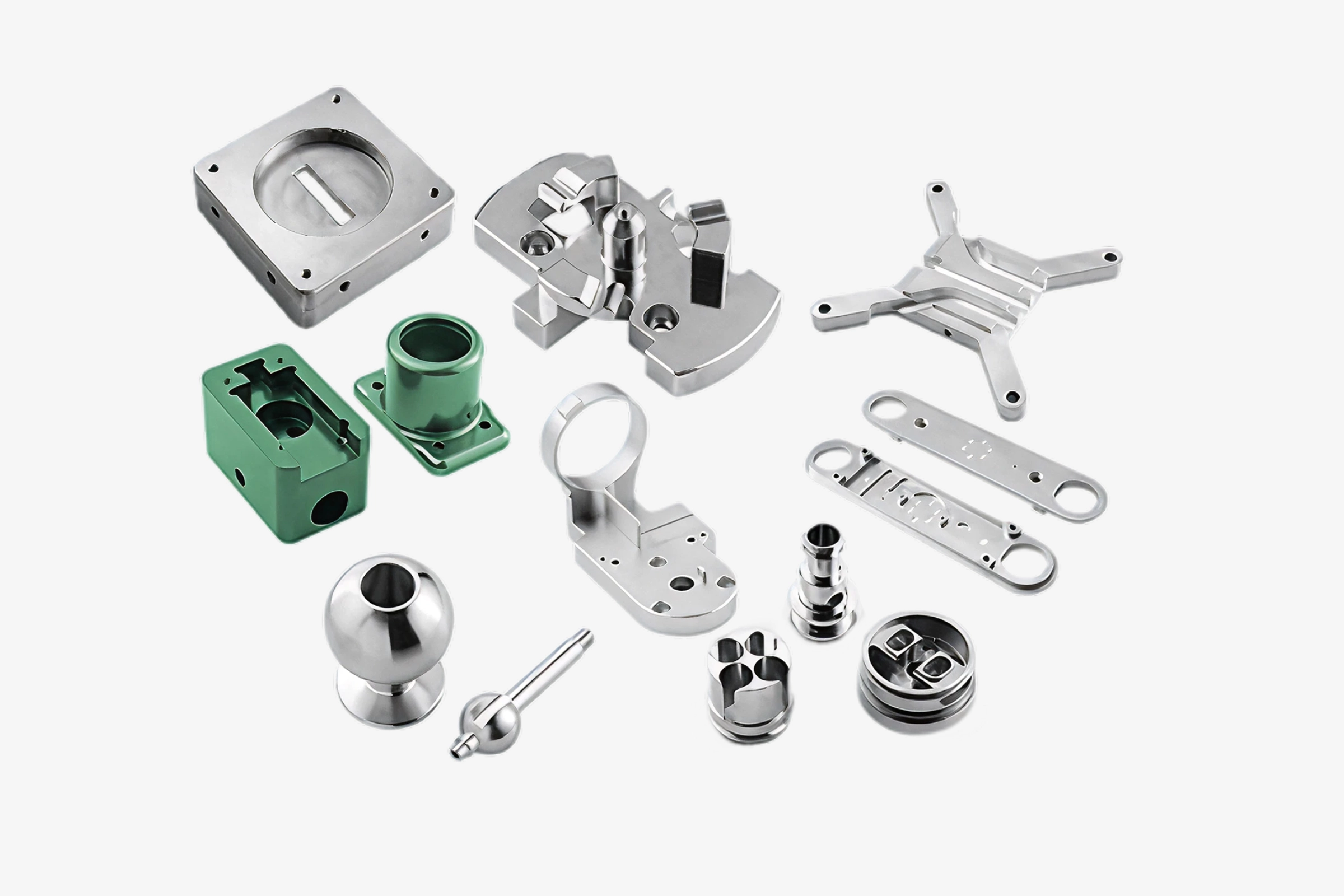
“Everything arrived labeled, inspected, and production-ready. The transparency in their process gave us full peace of mind.”
— Elena García, Quality Analyst
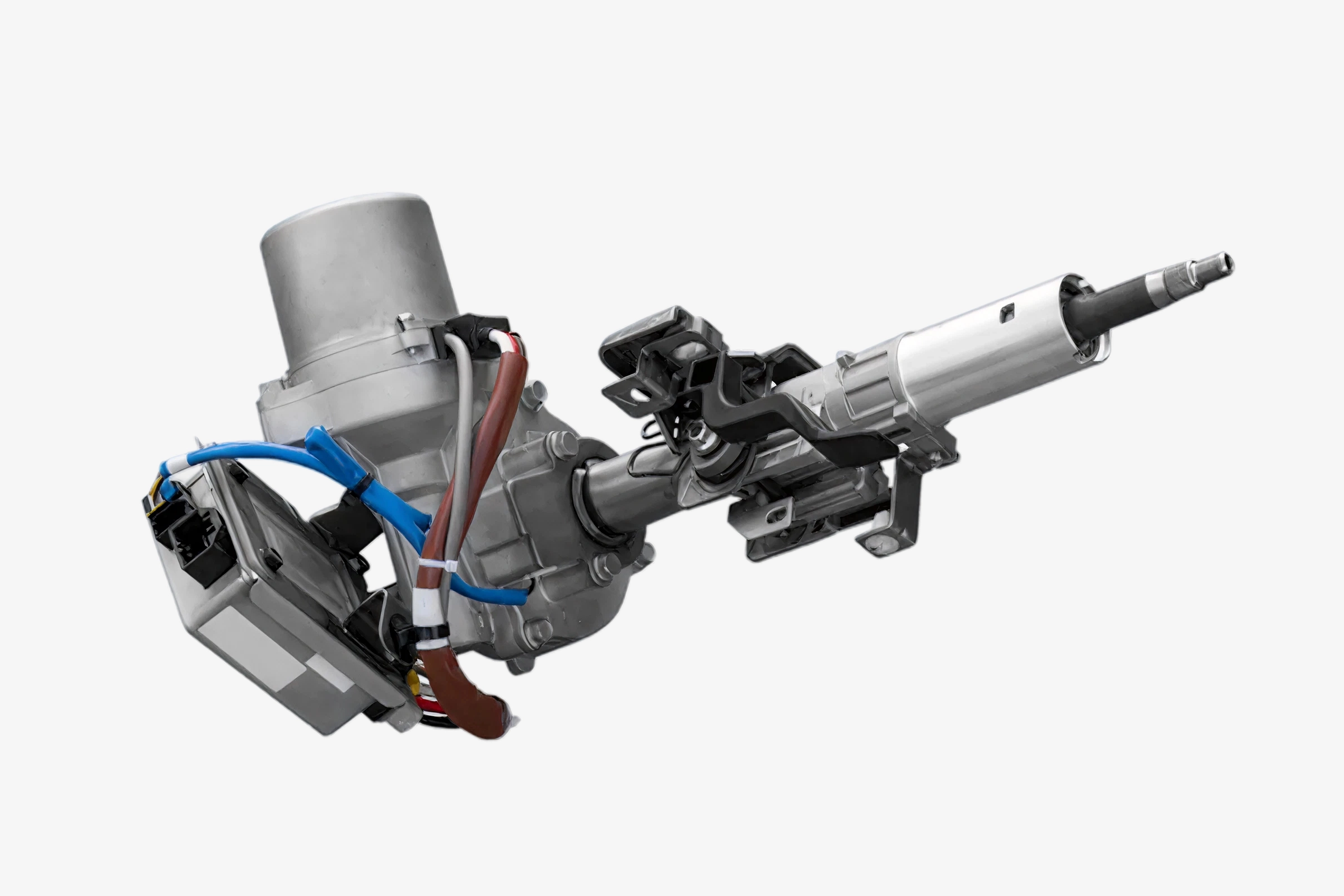
“We needed complex joints and actuator mounts with fine tolerances. Koonze delivered parts that assembled perfectly the first time.”
— Alex W., Robotics Engineer
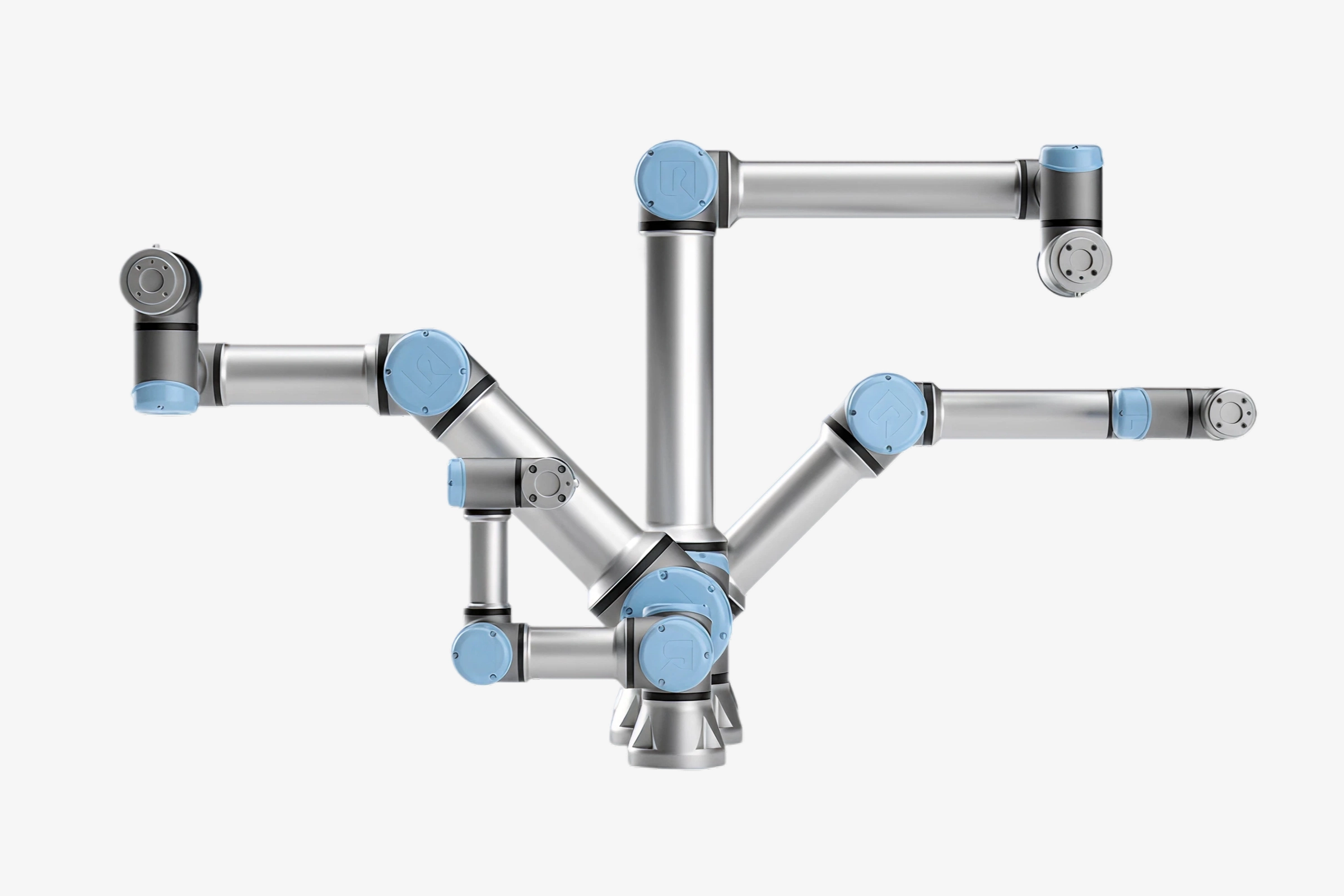
“Koonze helped us reduce weight in our arm module with smart DFM suggestions. That allowed us to boost performance without redesigning the whole system.”
— Jenny Tao, Mechatronics Specialist
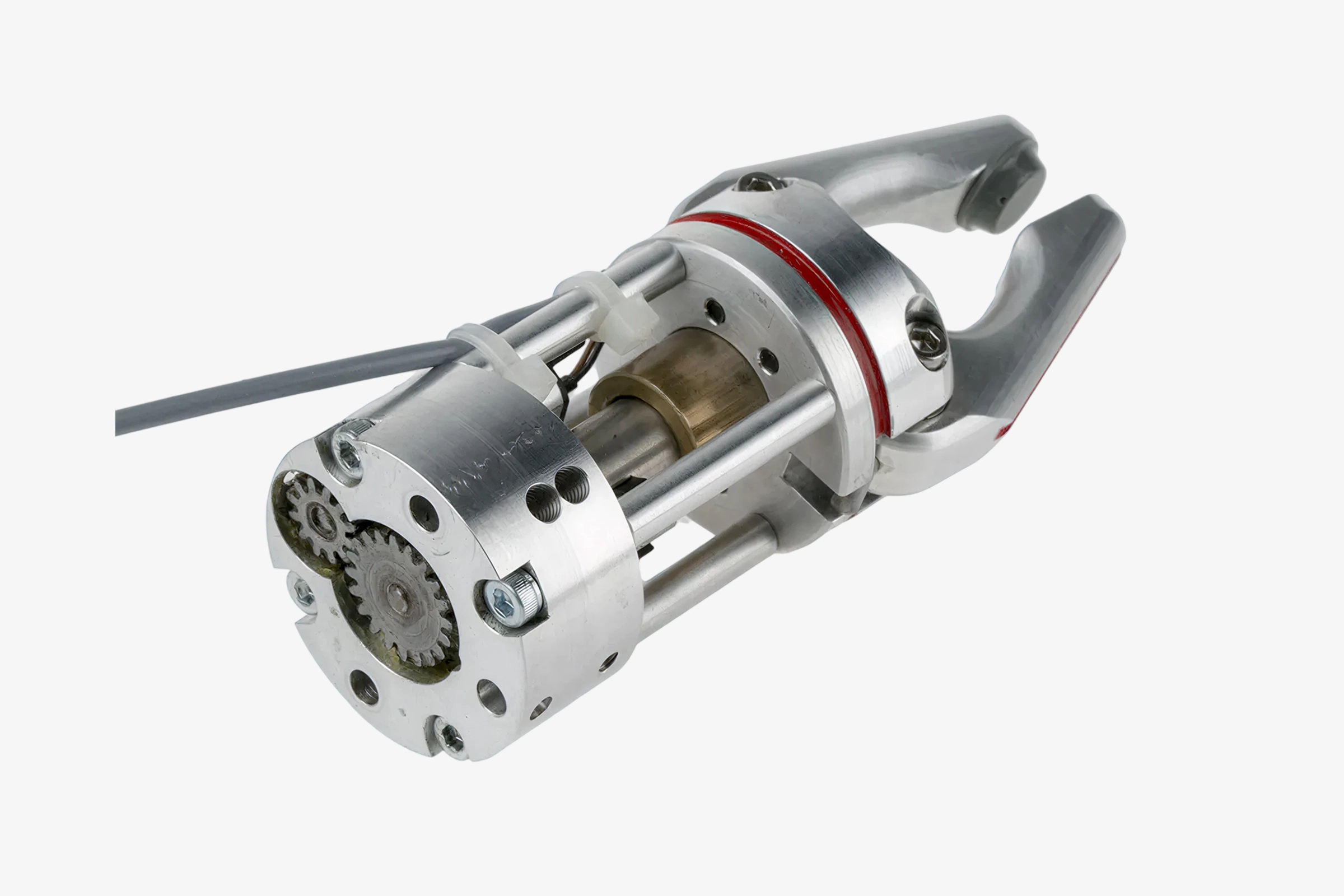
“Every prototype came dimensionally accurate and well-finished. That level of consistency helped us move to pilot production fast.”
— Robert Kim, Technical Lead
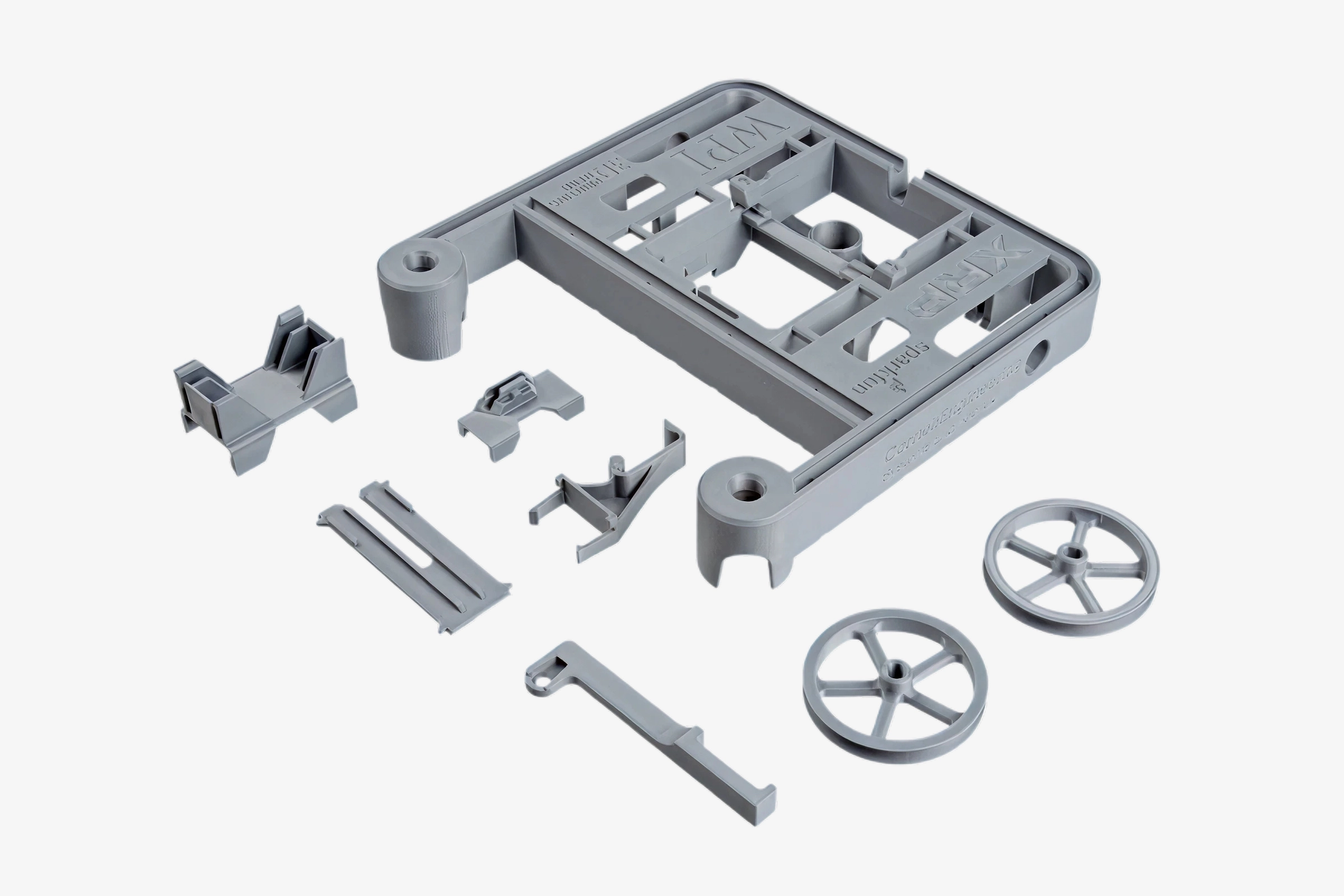
“Their flexibility during rapid iterations made all the difference. We were able to test and refine our design in record time.”
— Elisa Romano, R&D Manager
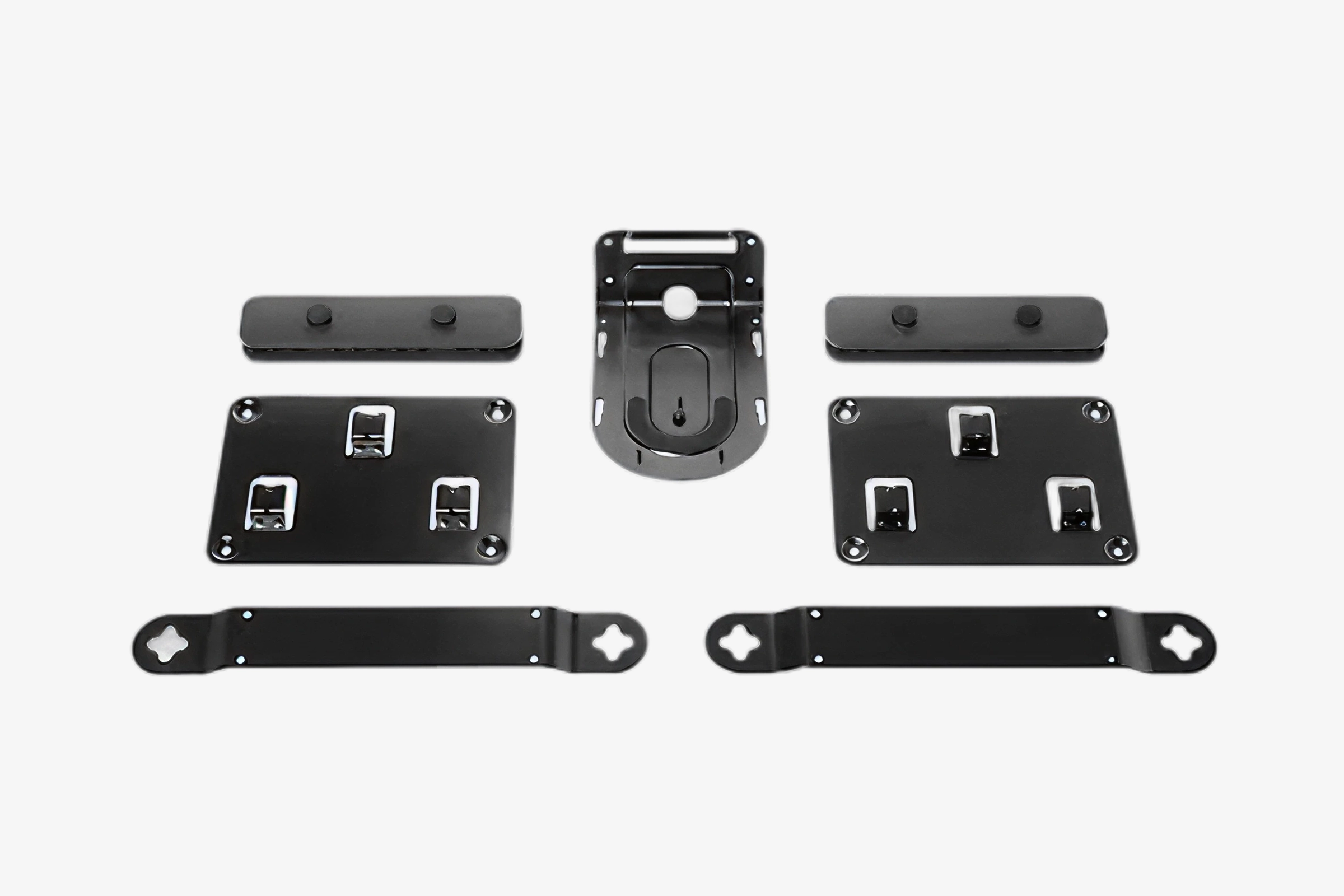
“Surface quality was everything for our camera mount components. Koonze’s attention to detail in finishing and packaging was excellent.”
— Derek Chen, Optical Engineer
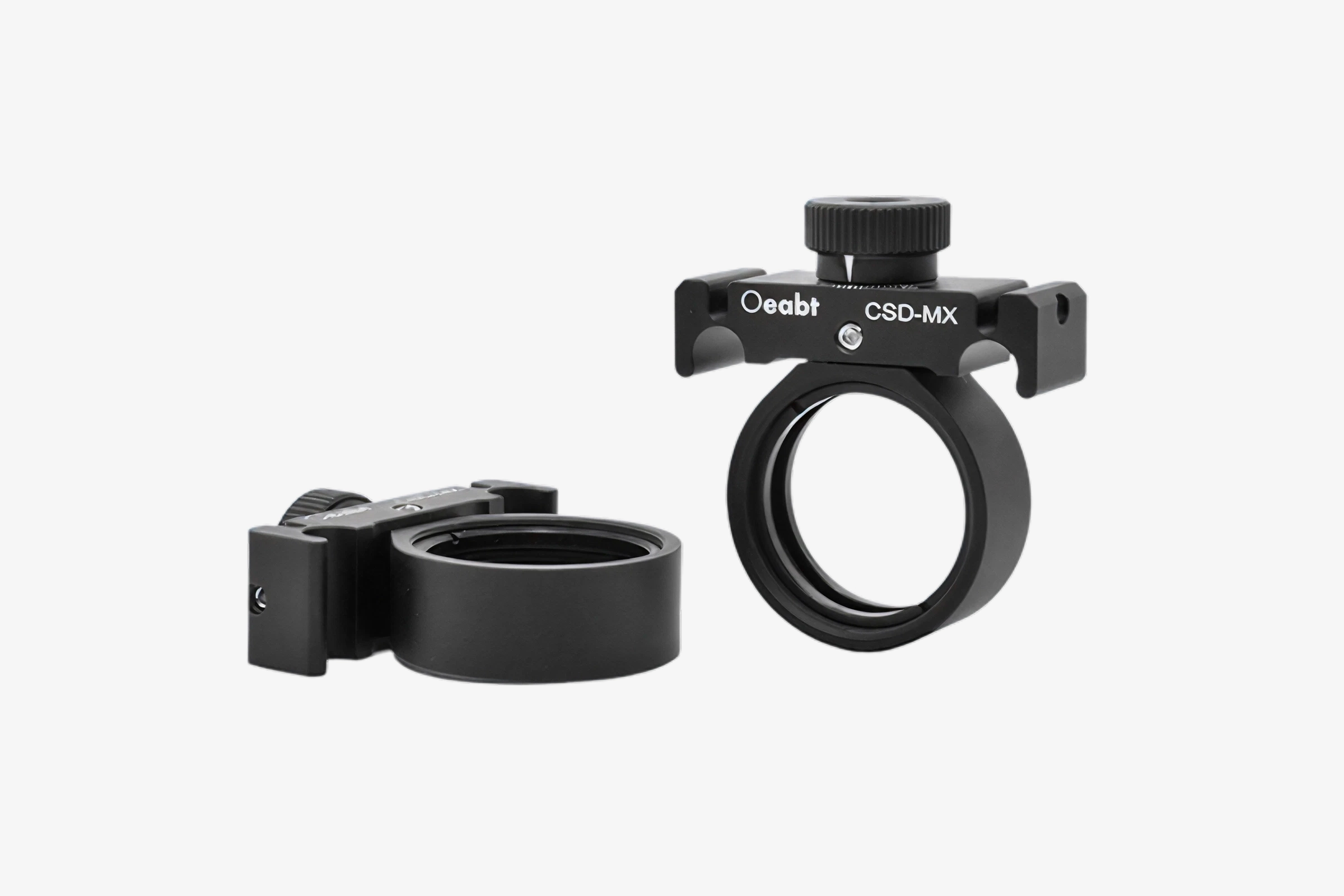
“Precision was non-negotiable for our imaging lens fixtures. The tolerances were spot on, and the documentation was clear and complete.”
— Valerie Young, QA Specialist
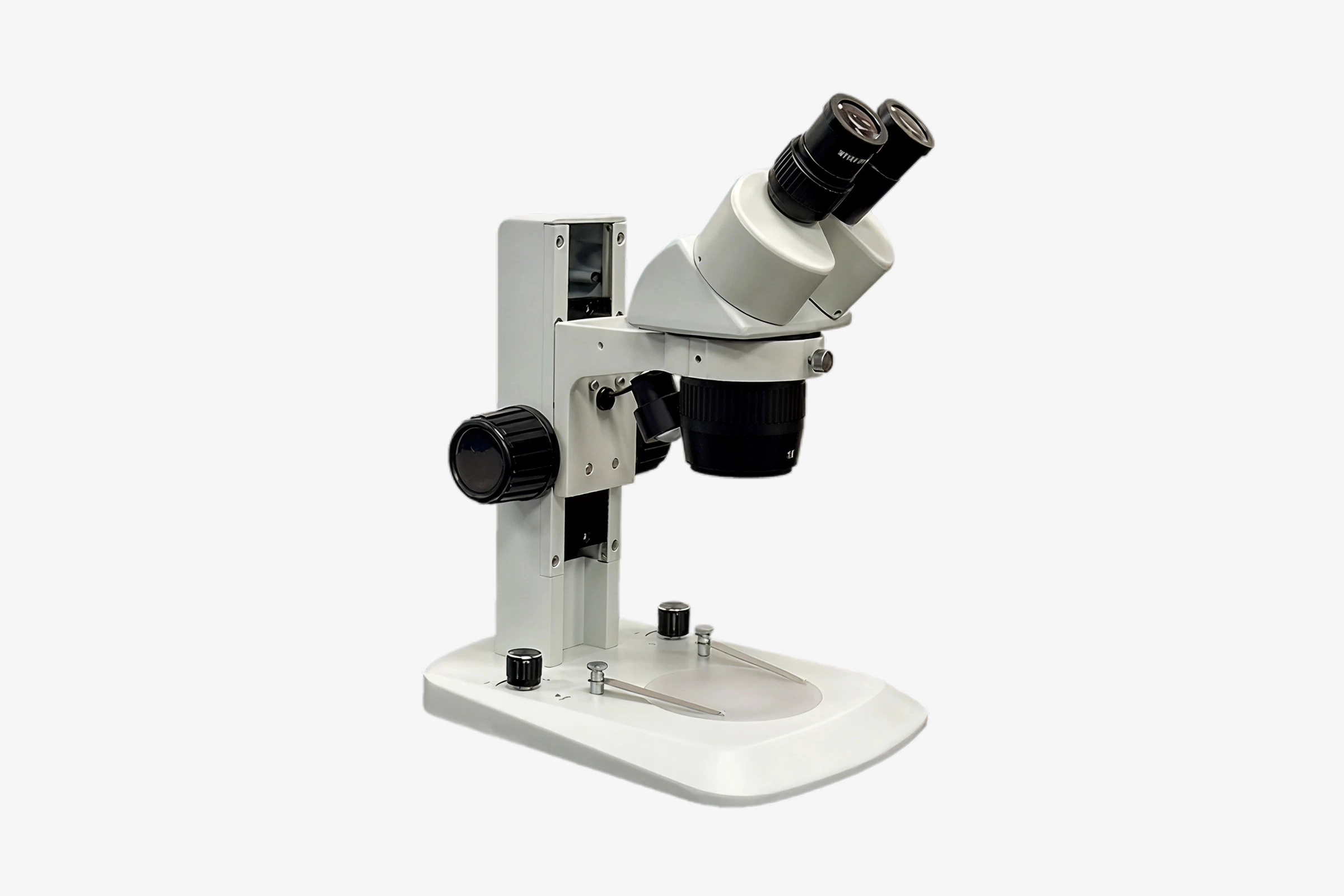
“We had a small window to prototype custom enclosures for our new microscope line. Koonze turned them around in days with no compromise in accuracy.”
— Tomás Alvarez, Engineering Manager
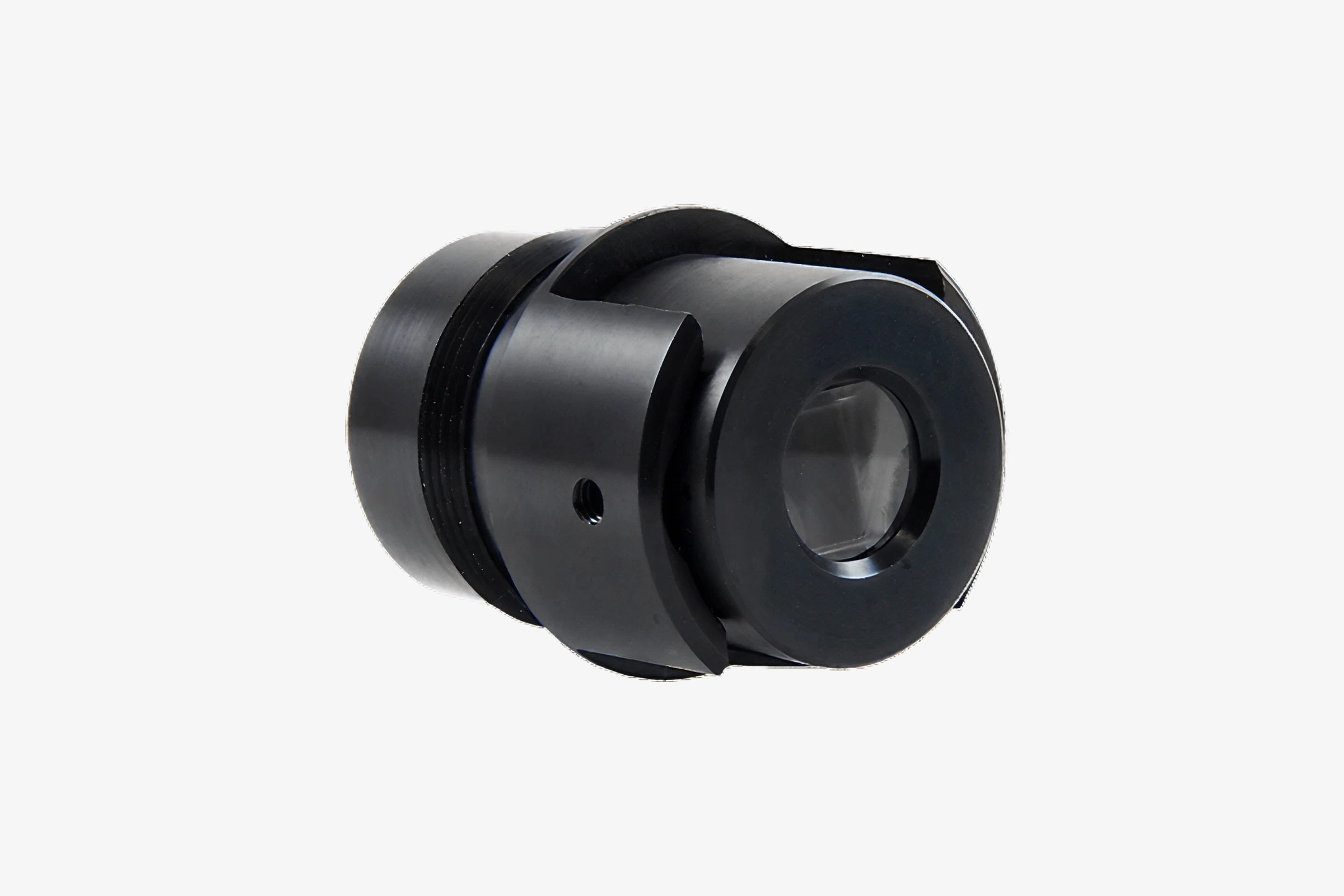
“Their team understood the importance of part alignment and flatness in optical assemblies. That technical depth gave us a lot of confidence.”
— Annika Müller, Systems Engineer
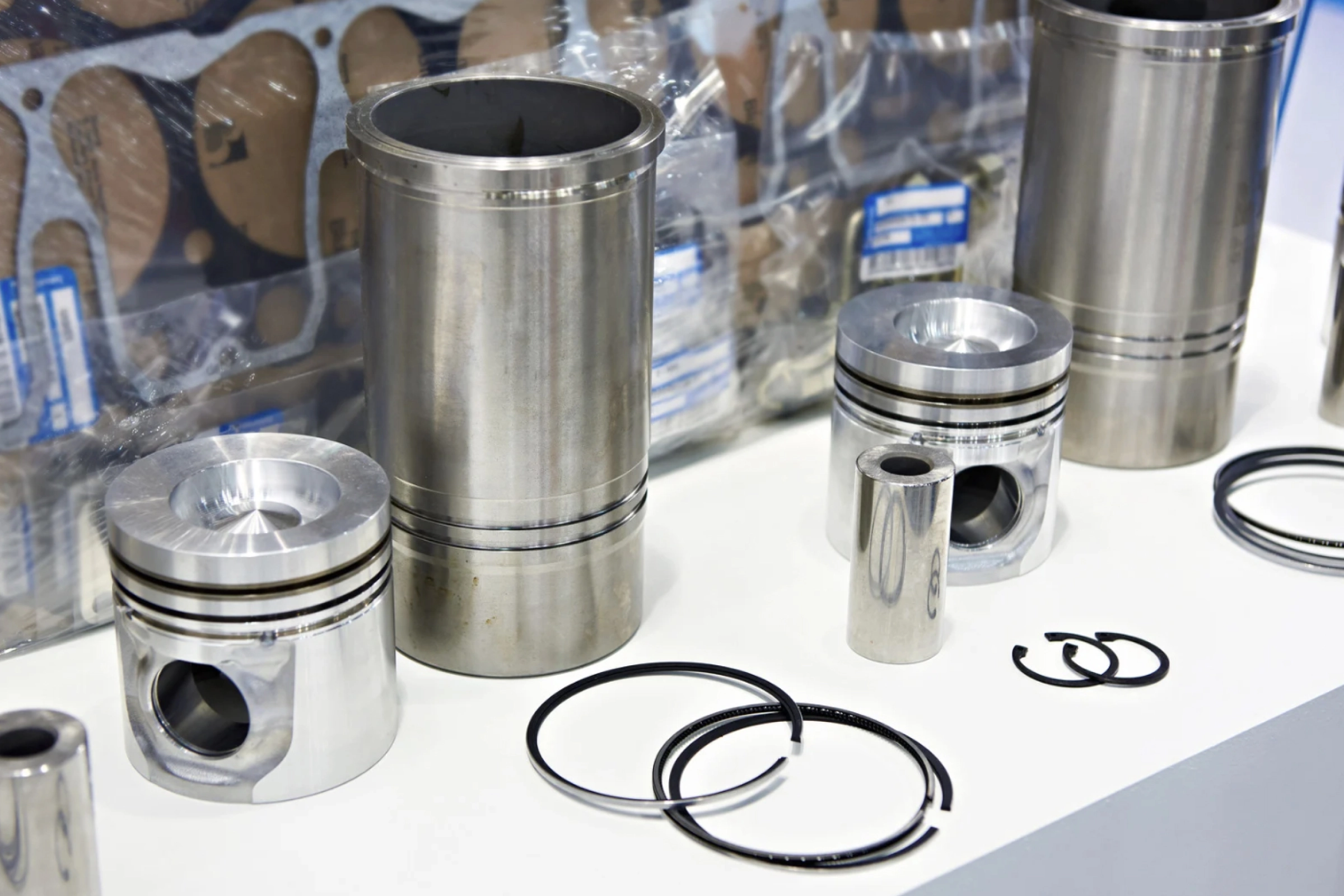
“Durability and repeatability matter most for industrial assemblies. Koonze’s machined parts held up across multiple test cycles with zero variance.”
— Martin Zhao, Manufacturing Engineer
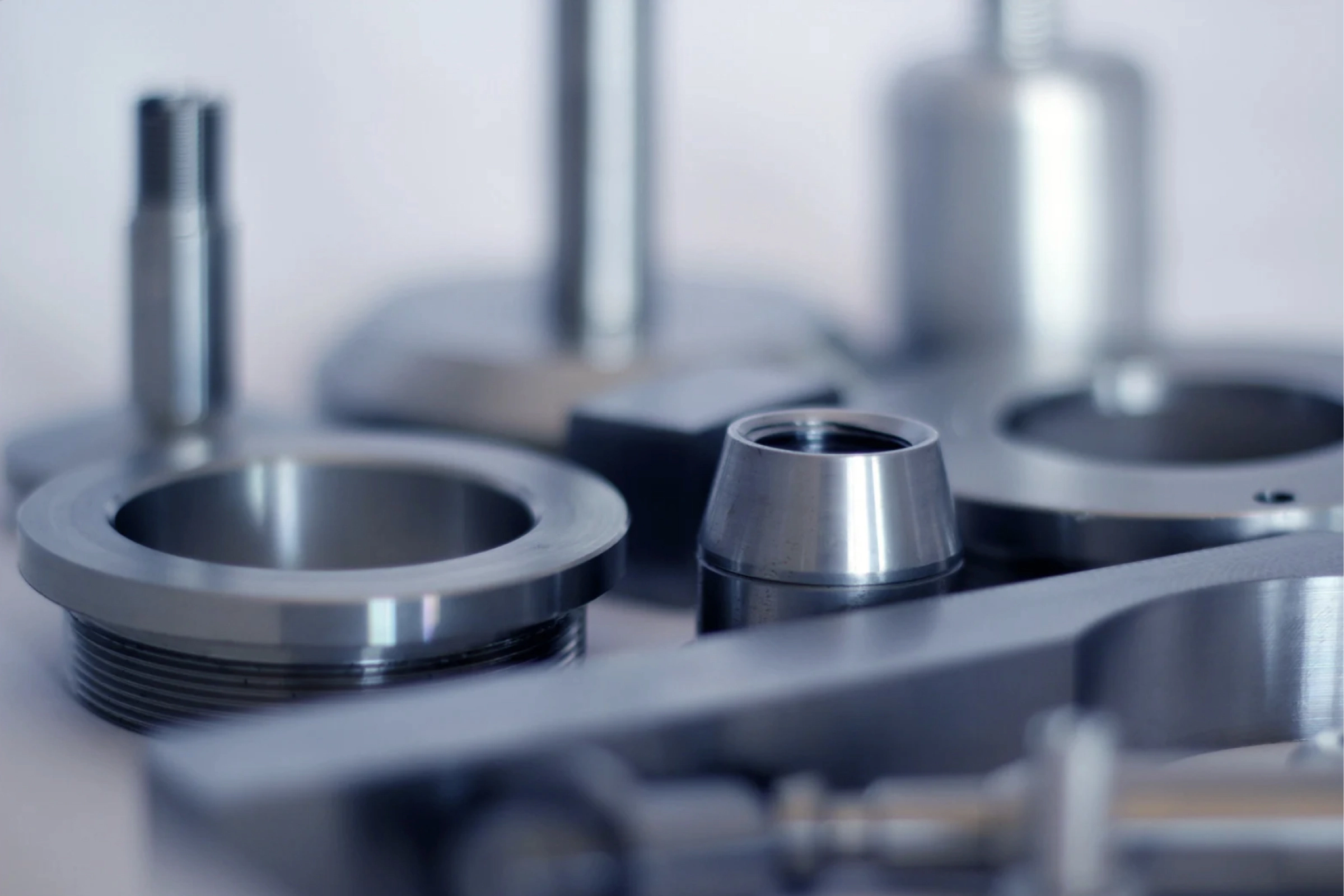
“Their team was flexible during design changes and handled last-minute requests without delay. That kind of support is rare.”
— Sarah DeWitt, Project Coordinator
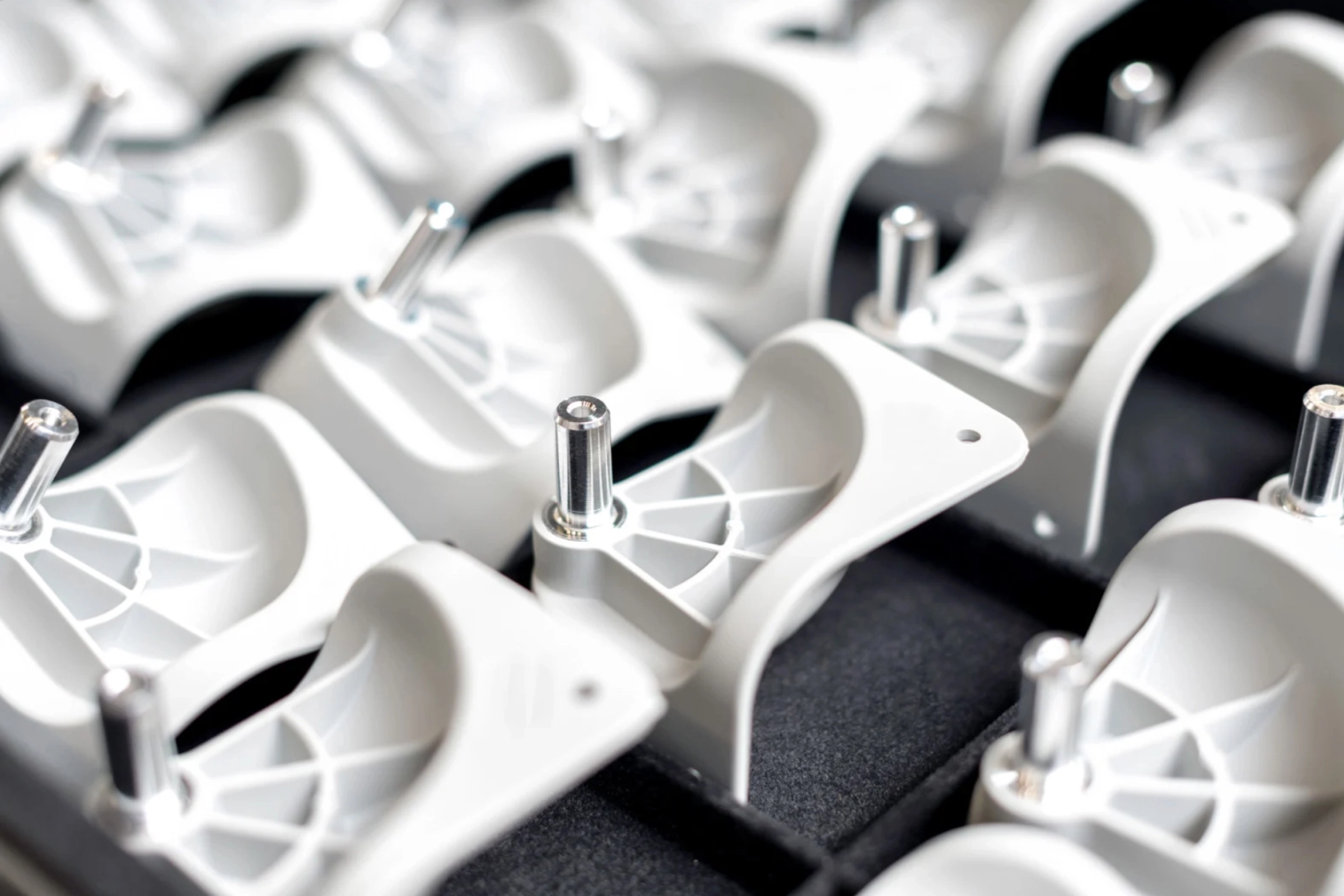
“Our custom housings needed tight fits and rugged materials. Koonze delivered exactly what we asked for, on time and within spec.”
— Leon K., Mechanical Supervisor
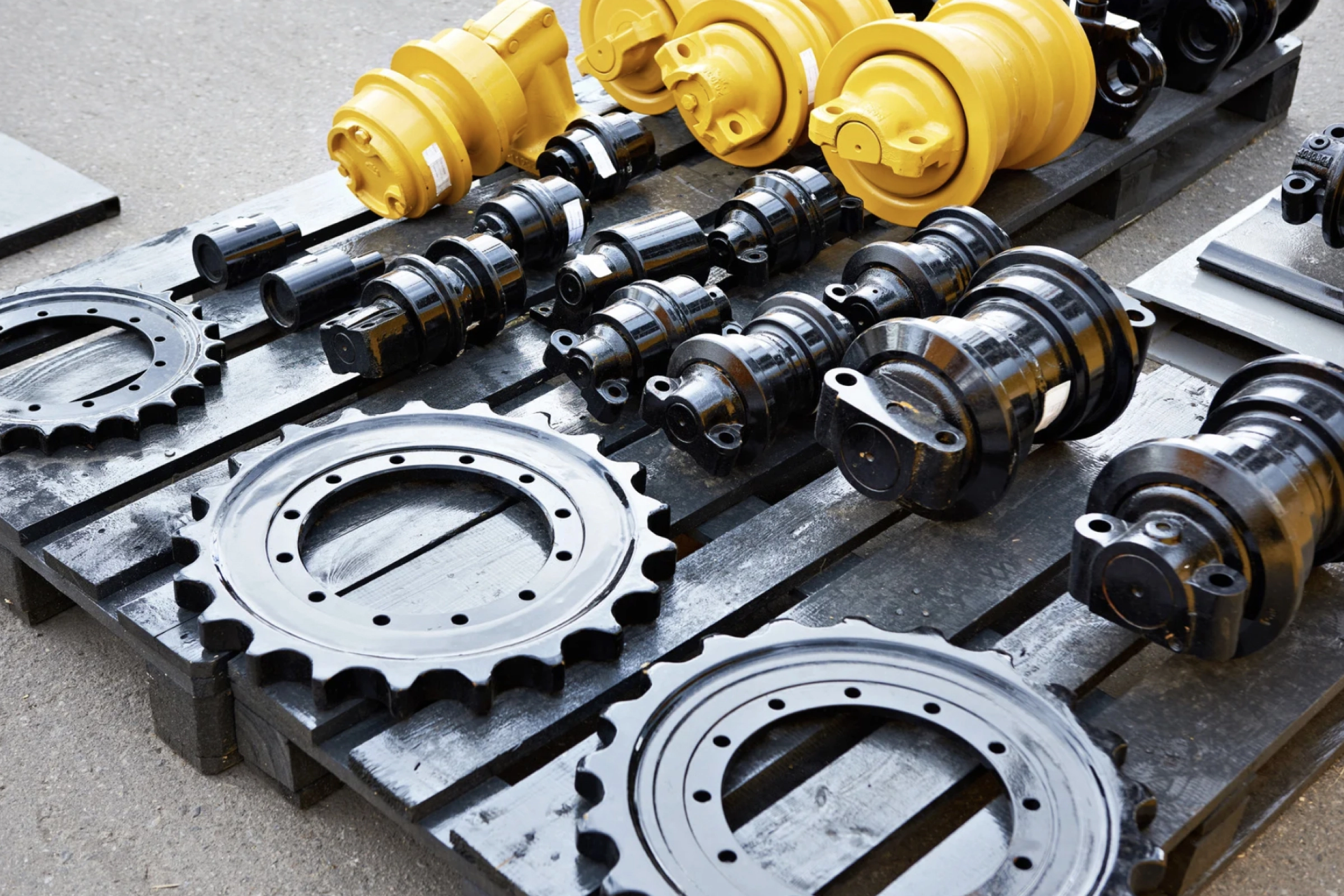
“The parts were well-packed, labeled, and arrived fully inspected. It’s the kind of reliability we count on for production tooling.”
— Priya Anand, Procurement Manager
How to Work with Us
Upload Design
Upload your detailed specifications and design to receive a rapid quote.
DFM Review
We provide DFM analysis to refine your design before mass production.
Confirm Quote
We collaborate with experts to bring your designs to life.
Receive Parts
Your custom parts will arrive at your doorstep in just a few days.
Why Choose Us
Every part undergoes rigorous inspection to ensure it meets your exact specifications—no surprises, just precision.
From prototypes to production, we deliver on time with streamlined processes and efficient project management.
Our engineers review your designs and provide actionable feedback to help optimize cost, performance, and manufacturability.