Mass Production Services
Koonze Model specializes in high-efficiency mass production, ensuring precision, consistency, and relatively fast lead times. Our advanced facilities support large-scale manufacturing with optimized costs and a wide range of materials.
- 98% of bulk orders are delivered on time.
- Monthly output exceeds 100,000 parts.
- Mass production yield rate reaches up to 96.8%.
Start a Mass Production Quote
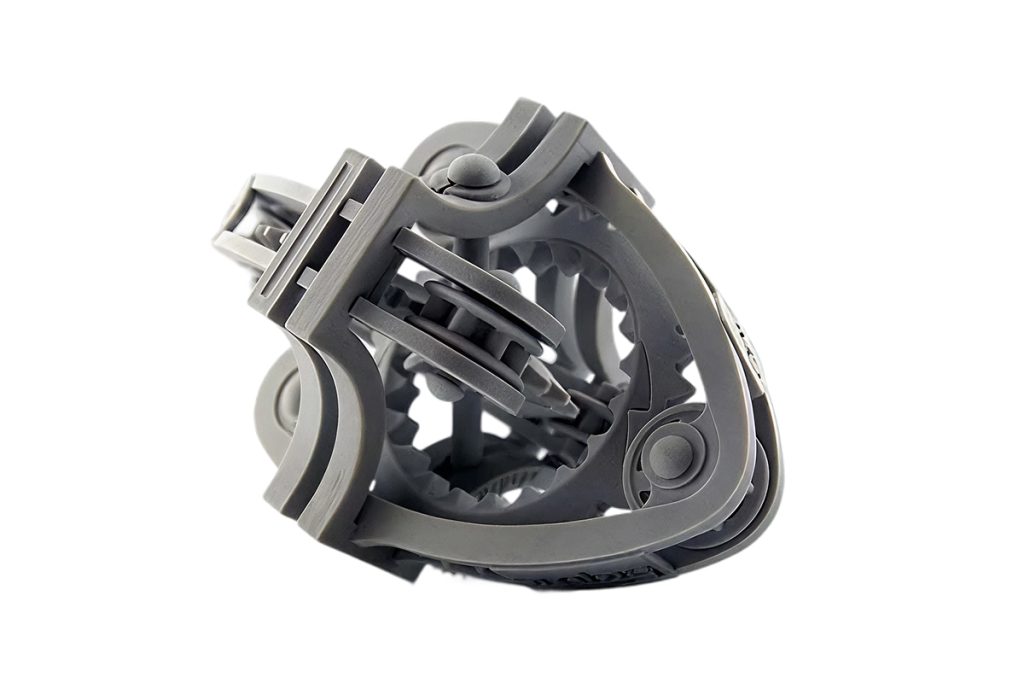
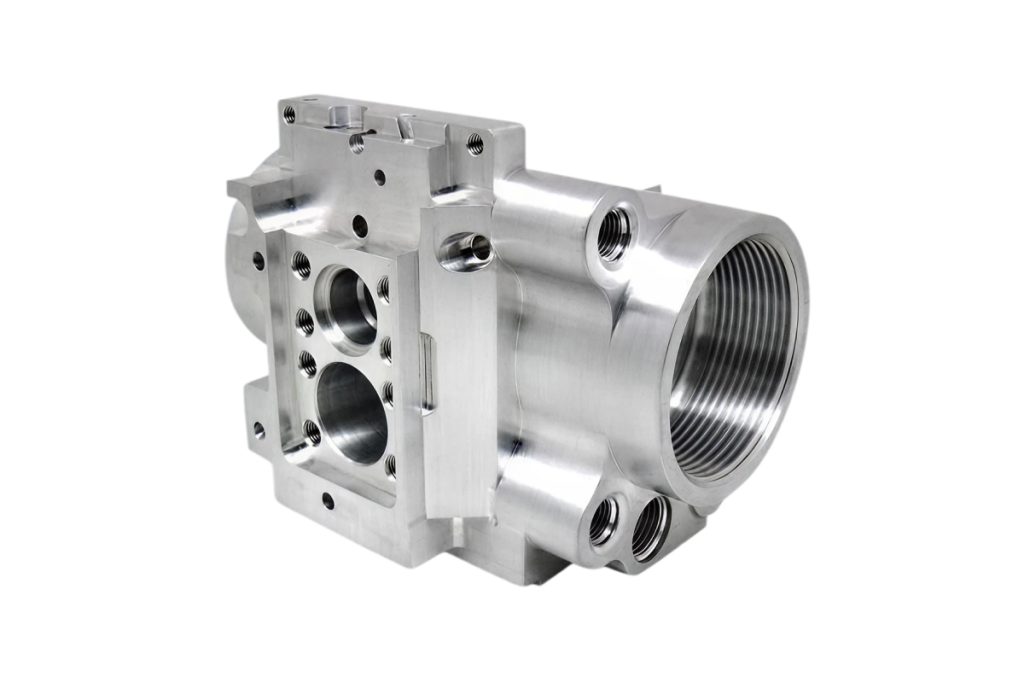
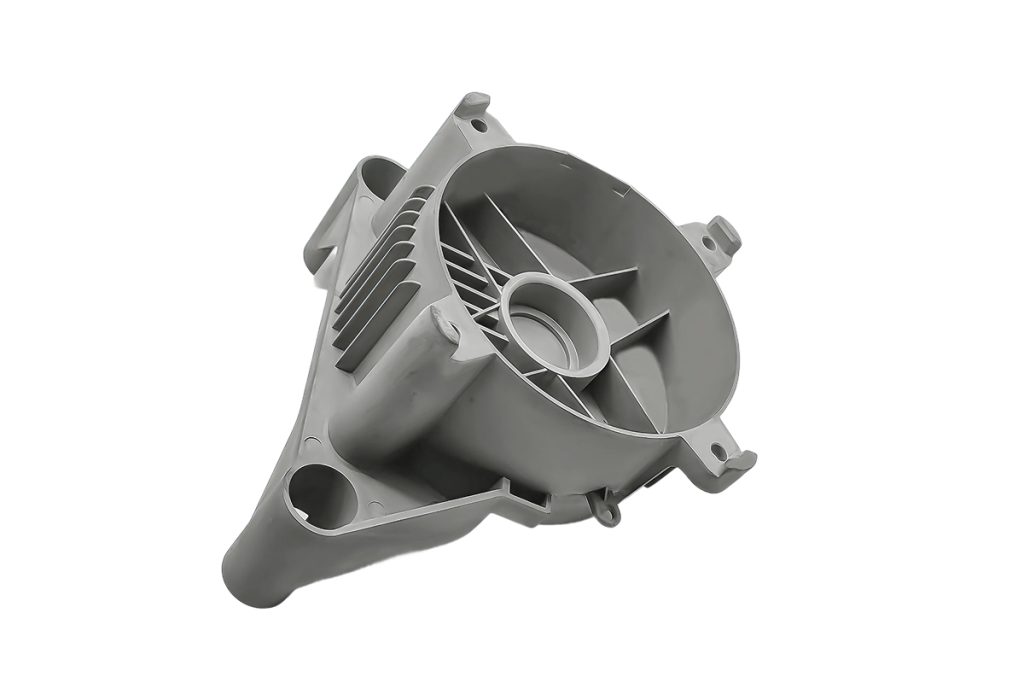
- All uploads are secure and confidential.
Koonze's Mass Production Solutions
Koonze Model is your go-to solution for custom part production. With diverse manufacturing processes, expert engineers, and dedicated project managers, scaling up has never been easier. Partner with us, and we’ll handle the heavy lifting.
From single prototypes to millions of parts, we accommodate all production scales across industries worldwide. Every order benefits from:
- Free DFM feedback for optimized manufacturability.
- Rigorous mass production QC, backed by 11+ advanced inspection tools, including 5 CMMs, 8 2D Optical Measuring Systems, height gauges, micrometers, spectrometers, and more.
- Comprehensive in-house assembly for high-volume production, including box and electromechanical assembly.
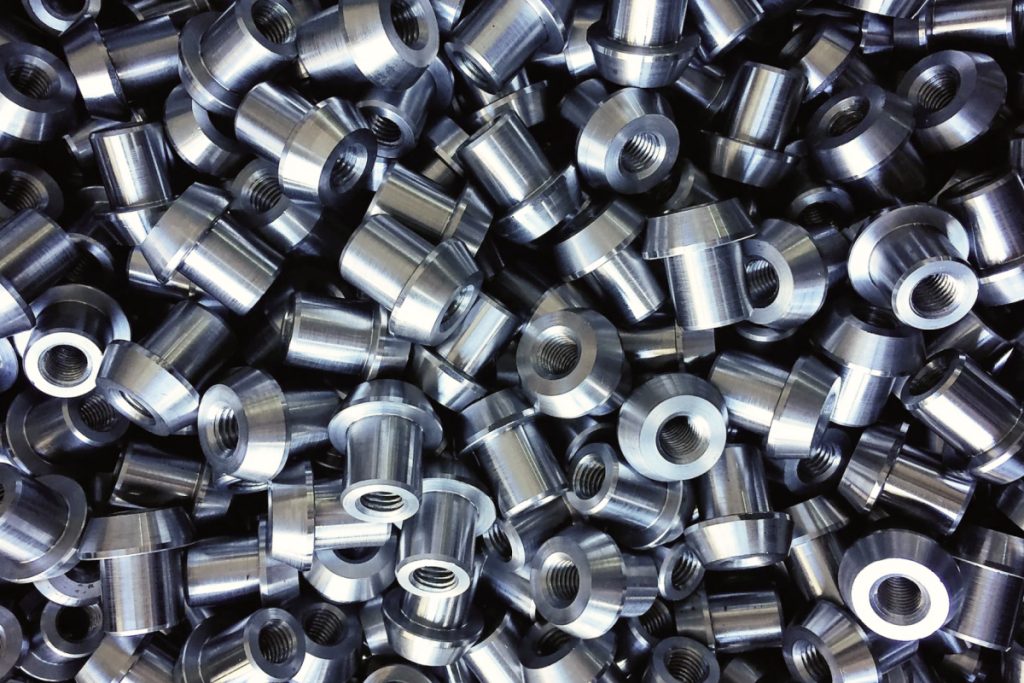
Our Visualized Production Progress
Our Key Mass Production Services
CNC Machining
CNC machining delivers high-precision, versatile production of metal and plastic parts with tight tolerances.
At Koonze Model, our state-of-the-art CNC machines handle complex geometries and intricate designs with exceptional accuracy, offering a wide range of material options, from aluminum and stainless steel to engineering plastics.
Advanced machining techniques, automation, and rigorous quality control ensure fast, reliable production for industries like automotive, aerospace, medical devices, and consumer electronics.
Dimensions | Description |
---|---|
Material Selection | We offer a variety of materials, including aluminum, stainless steel, titanium, and engineering plastics, to match your part’s strength, durability, and cost requirements. |
Precision Machining | Our CNC machines achieve precise tolerances as tight as ±0.01mm, ensuring high-quality parts with exact specifications. |
Surface Finish | We provide a range of surface finishes, from smooth milled finishes to polished or anodized surfaces, ensuring both aesthetics and functionality. |
Complex Geometries | Our advanced CNC capabilities handle intricate designs, multi-axis milling, and turning, producing parts with complex geometries and fine details. |
Efficiency & Speed | By optimizing tool paths and minimizing machine downtime, we ensure fast turnarounds and competitive lead times without sacrificing quality. |
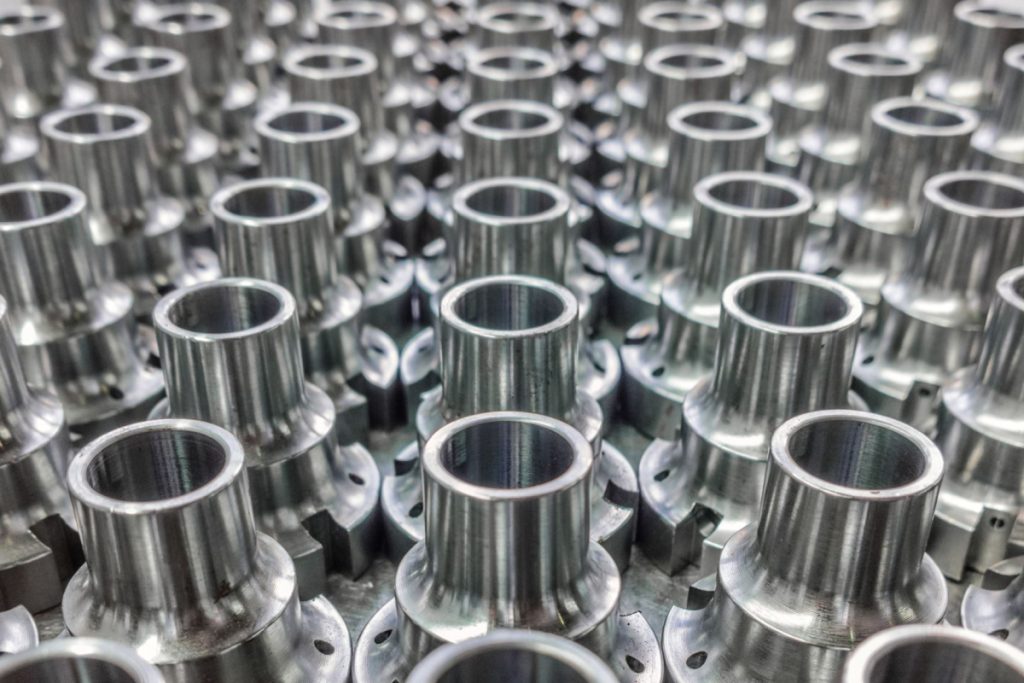
Injection Molding
Injection molding enables high-precision, cost-efficient mass production of plastic parts.
At Koonze Model, our advanced high-tonnage injection molding machines machines handle complex geometries with tight tolerances using a wide range of thermoplastics, from ABS to high-performance resins.
Optimized mold design, automation, and strict quality control ensure fast, reliable production for industries like automotive, medical, and consumer electronics.
Dimensions | Description |
---|---|
Material Selection | We help you choose from 50+ thermoplastics, including ABS, PC, and POM, to ensure optimal strength, durability, and cost-effectiveness based on your application needs. |
Mold Design Optimization | Our engineers refine mold designs to reduce cycle times, minimize waste, and improve efficiency, lowering production costs. |
Wall Thickness Control | Maintaining uniform wall thickness prevents defects like warping or sink marks, ensuring structural integrity and cost savings. |
Draft Angles | Proper draft angles enable easy mold release and high-quality surface finishes, enhancing manufacturability. |
Gate Location | Strategic gate placement ensures uniform material flow, reducing stress concentrations and defects for consistent part quality. |
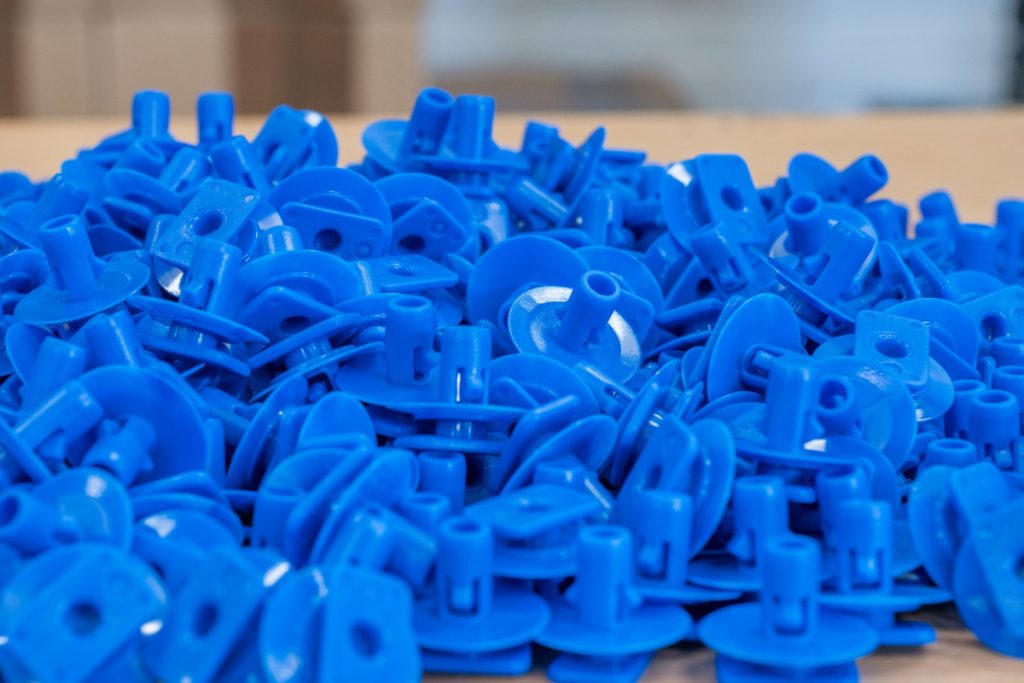
Die Casting
Die casting enables high-volume production of precise metal parts with excellent detail and surface finish. At Koonze Model, our advanced die casting machines handle aluminum, zinc, and magnesium alloys, ensuring strong, lightweight components with tight tolerances (±0.05mm).
From automotive parts to electronics enclosures, we deliver consistent quality and durability at scale.
Capabilities | Description |
---|---|
Alloy Selection | Selecting the appropriate alloy (e.g., aluminum, zinc, magnesium) ensures the desired mechanical properties, corrosion resistance, and cost-effectiveness. |
Tooling Design | Our advanced tooling design techniques minimize cycle times and maximize part consistency. We use state-of-the-art CAD/CAM systems to create precise molds. |
Surface Finish | Die casting produces parts with excellent surface finish, reducing the need for secondary finishing operations and lowering overall costs. |
Post-Casting Finishing | We offer a range of post-casting finishing options, including machining, polishing, and coating, to meet your exact specifications. |
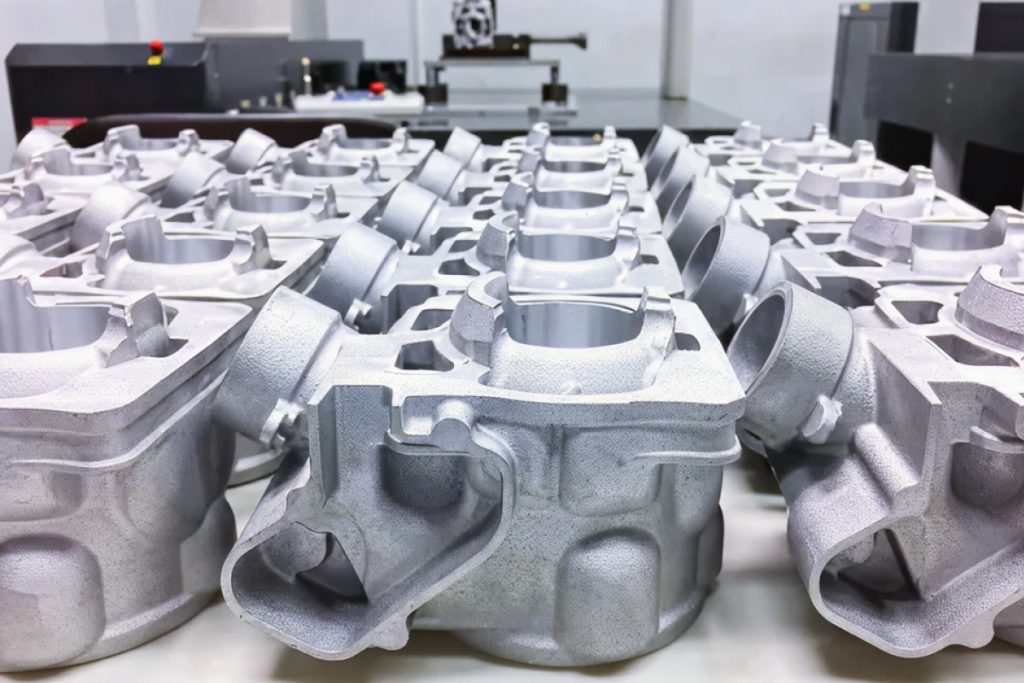
Extrusion
Extrusion is ideal for producing continuous profiles with consistent cross-sections, such as pipes, frames, and structural components.
At Koonze Model, we work with aluminum, PVC, and other materials to create high-precision extrusions with tight tolerances (±0.1mm).
Our capabilities support custom shapes, hollow or solid sections, and complex geometries, ensuring cost-effective, high-quality solutions for industries like construction, automotive, and electronics.
Capabilities | Description |
---|---|
Profile Design | Customizable profile designs allow us to produce parts with precise dimensions and cross-sectional consistency. |
Material Selection | We work with a variety of materials, including metals and plastics, to ensure the best fit for your application's requirements. |
Uniformity | Extrusion ensures consistent wall thickness and shape along the entire length of the profile, minimizing waste and rework. |
Secondary Operations | We offer additional operations such as cutting, drilling, and welding to complete your parts according to your specifications. |
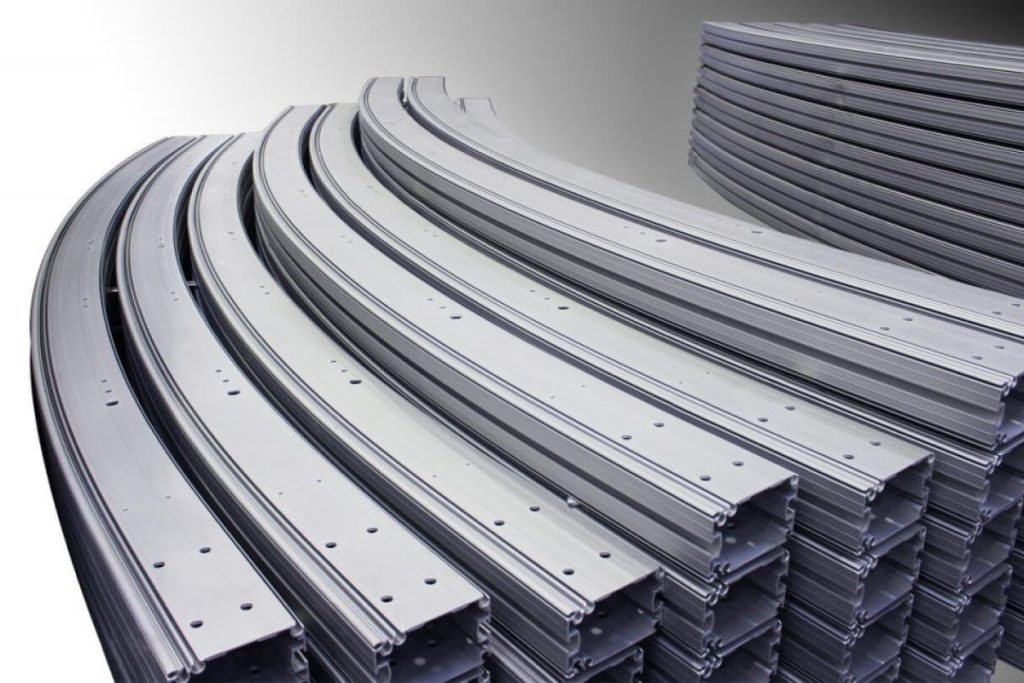
Stamping
Stamping is a high-speed, cost-efficient process for producing precision metal parts with complex shapes and tight tolerances (±0.05mm).
At Koonze Model, we utilize progressive, deep-draw, and transfer stamping to manufacture brackets, enclosures, and structural components from steel, aluminum, and copper alloys. Our automated presses handle high-volume production with consistent quality, making stamping ideal for automotive, electronics, and industrial applications.
Capabilities | Description |
---|---|
Material Selection | We work with a variety of sheet metals, including steel, aluminum, and stainless steel, to meet your strength and corrosion resistance requirements. |
Tooling Precision | Our precision tooling ensures consistent part geometry and dimensional accuracy across high volumes. |
Forming Techniques | We employ various forming techniques, such as bending, punching, and drawing, to achieve complex shapes while maintaining structural integrity. |
Surface Treatment | Optional surface treatments (e.g., painting, plating) enhance corrosion resistance and aesthetic appeal. |
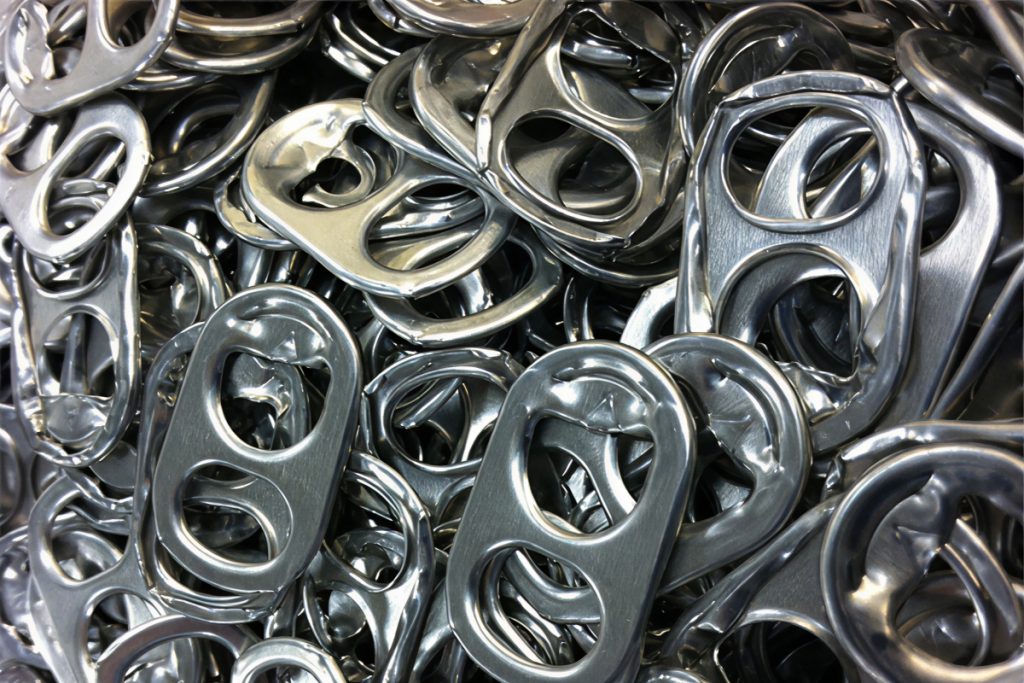
Assembly, Packaging, and Shipping
Efficient assembly, packaging, and shipping are key to on-time delivery and product integrity in large-scale production.
At Koonze Model, we optimize every step of the logistics process, from automated assembly lines to customized packaging solutions, ensuring parts are securely packaged to prevent damage during transit.
Capabilities | Description |
---|---|
Custom Packaging Solutions | We design and provide customized packaging to protect your products during transit and storage. |
Inventory Management | Robust inventory systems ensure timely availability of parts and materials, avoiding production bottlenecks. |
Shipping Coordination | Our logistics team coordinates with carriers to optimize shipping routes and schedules, ensuring timely deliveries. |
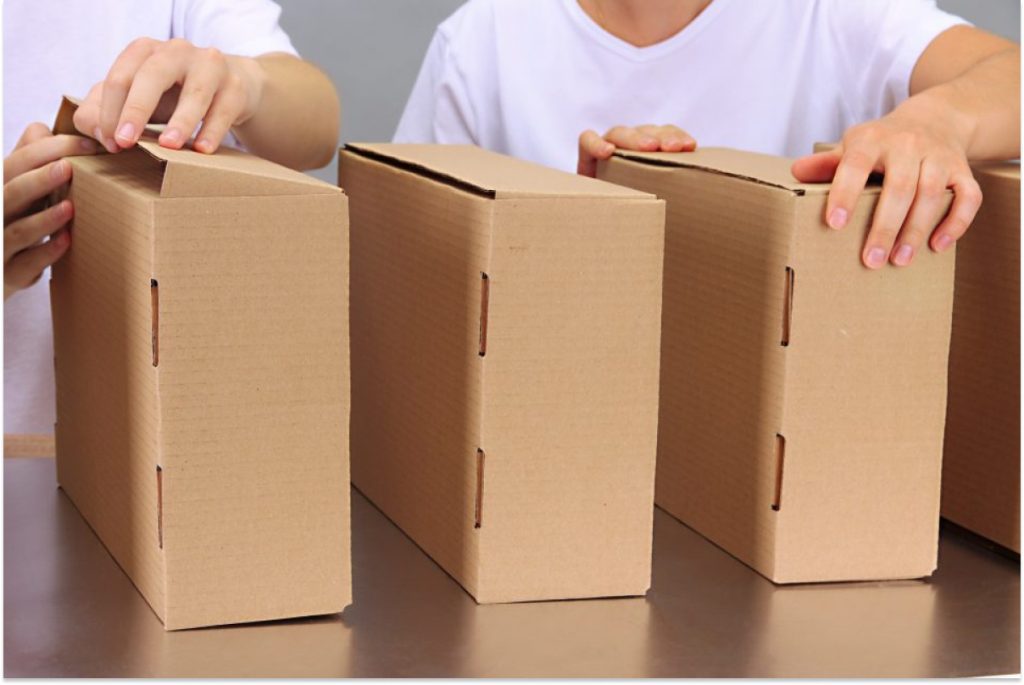
Your Trusted Partner for Mass Production
Ready to Scale Your Production? Get a Free Quote Today and Start Your Mass Production Journey with Us!
How to Choose
The Right Mass Production
Capabilities | Best For | Materials | Lead Time | Production Volume | Key Benefits | Cost |
CNC Machining | Precision parts with tight tolerances and complex geometries | Metal and plastic (e.g., aluminum, stainless steel, POM) | 3-7 days (no tooling needed) | Low to medium | High accuracy, fast turnaround, excellent material versatility | Moderate per part, no tooling cost |
Injection Molding | High-volume production of plastic parts with consistent quality | Plastic (e.g., ABS, PP, PC, Nylon) | 2-4 weeks (mold creation) | Medium to very high | High consistency, durable molds, suitable for complex shapes, cost-effective at scale | Low per part (at scale), high initial mold cost |
Die Casting | High-volume production of intricate metal parts with excellent surface finish | Metal (e.g., aluminum, zinc, magnesium) | 3-6 weeks (mold creation) | Medium to very high | Durable and consistent parts, suitable for mass production, excellent detail reproduction | Low per part (at scale), high initial mold cost |
Extrusion | Continuous production of uniform cross-sectional profiles such as pipes, frames, and structural components | Metal (e.g., aluminum), Plastic | 2-4 weeks (setup time) | Medium to very high | Cost-effective for linear parts, consistent cross-sections, minimal material waste | Low |
Stamping | High-volume production of flat or slightly curved metal parts with high precision | Metal (e.g., steel, aluminum, stainless steel) | 1-3 weeks (tooling setup) | Medium to very high | Fast cycle times, high repeatability, suitable for thin sheet metal parts | Low per part (at scale), moderate tooling cost |
Koonze Model's Production Quality Assurance
Why Choose Us
Precision Quality Control
We ensure every product meets strict quality standards through comprehensive inspections and advanced technology.
Fast Turnaround Time
Our efficient processes and experienced team allow us to deliver large volumes quickly, without compromising quality.
Scalability & Flexibility
whether you're producing small or large batches, we adapt to your needs, providing cost-effective solutions for any project size.
FAQs About Our Mass Production
We support production from low-volume pilot runs to high-volume manufacturing exceeding 100,000 units per month.
We follow strict quality control processes, including in-process inspections and final checks, with a qualified rate up to 96.8%.
We serve automotive, consumer electronics, medical, robotics, and more—delivering reliable and scalable parts across sectors.
Yes. Our engineers provide DFM (Design for Manufacturability) feedback to improve efficiency, reduce cost, and enhance part reliability.
Our main factory is located in Shenzhen, China, equipped with advanced CNC machines, injection molding lines, and quality labs.