Custom Die Casting Services
Koonze Model’s die-casting services deliver high-precision castings with outstanding dimensional accuracy and surface quality. These castings minimize post-processing needs and enhance compatibility, resulting in faster production and reduced costs.
- Achieves tight tolerances up to ± 0.05 mm for precision parts.
- Supports aluminum, zinc, and magnesium alloys for versatile applications.
- Utilizes high-pressure die-casting machines from 160T to 2000T for efficient production.
Start a New Die Casting Service Quote
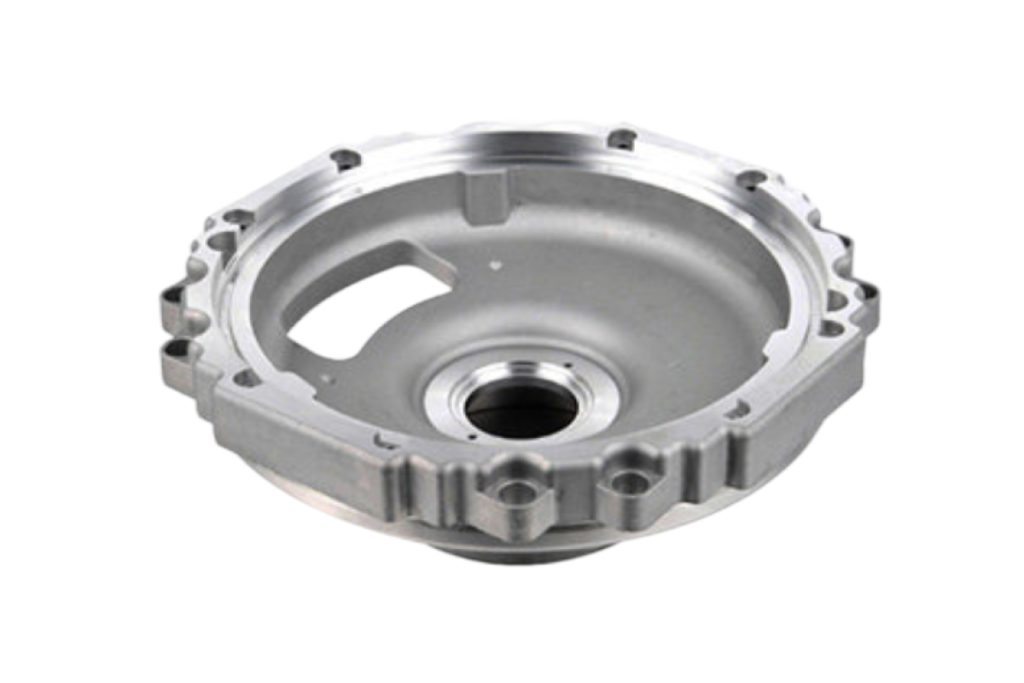
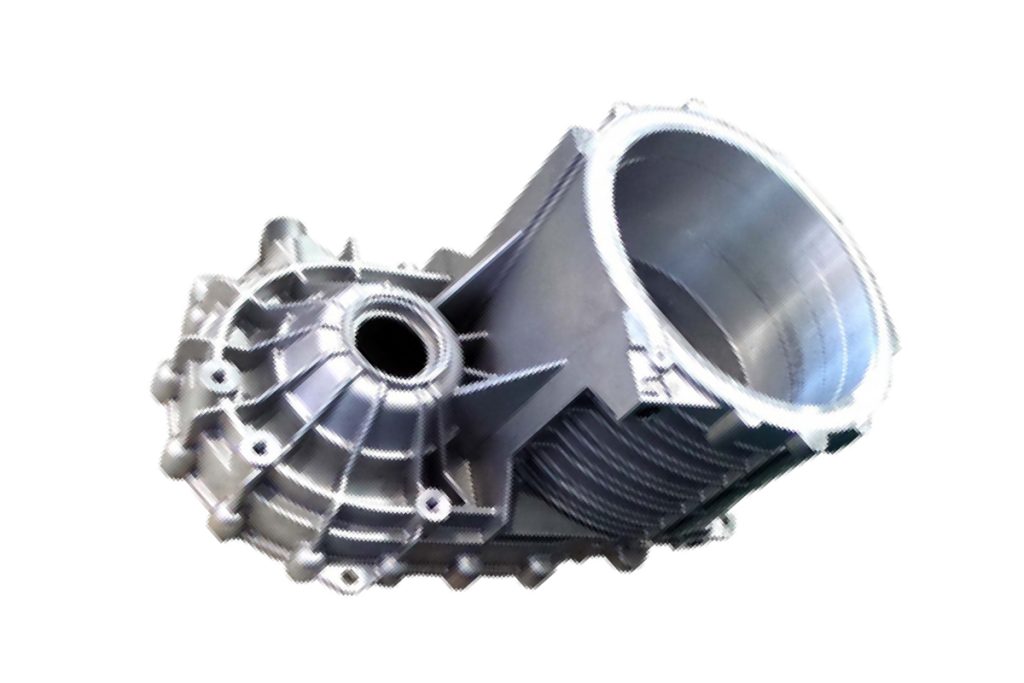
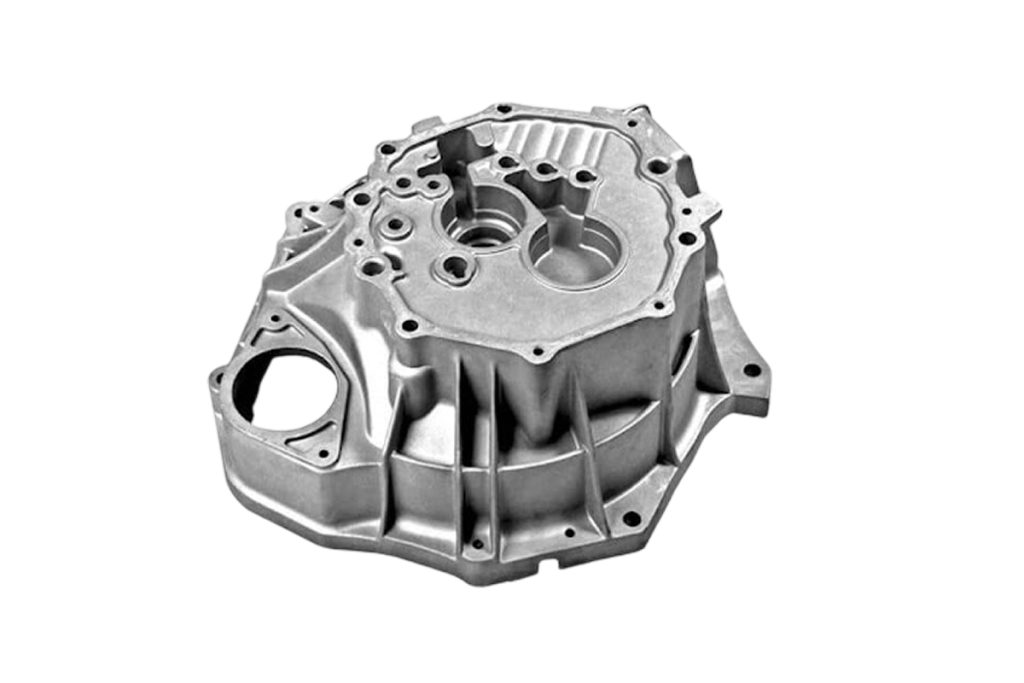
- All uploads are secure and confidential.
Die Casting Solutions Offered by Koonze Model
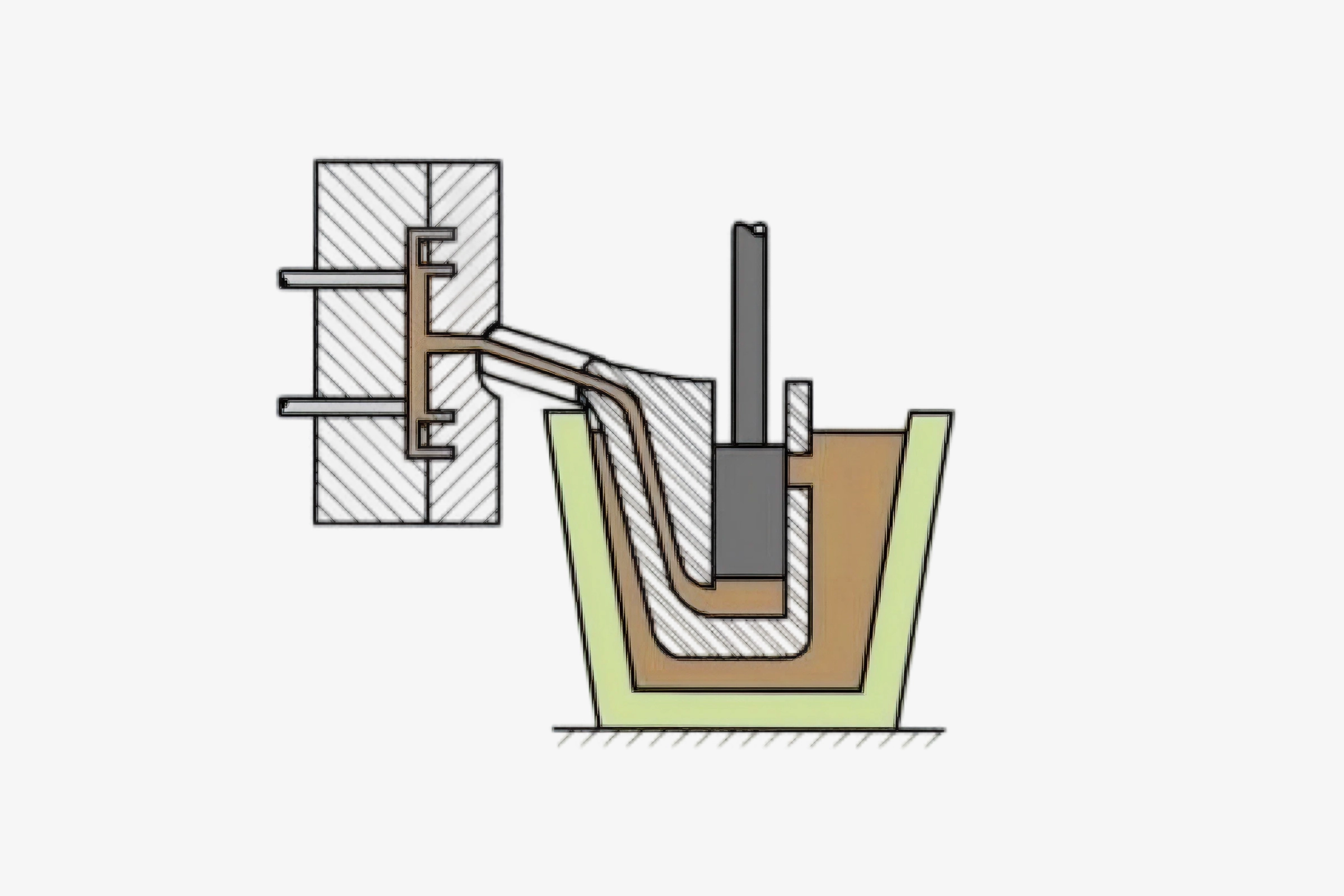
Hot Chamber Die Casting
Koonze Model offers reliable hot chamber die casting services for high-volume production of zinc, magnesium, and lead parts. With in-house gooseneck systems and precision tooling, we ensure consistent quality, fast cycle times, and smooth surface finishes—ideal for small, intricate components that demand accuracy and durability.
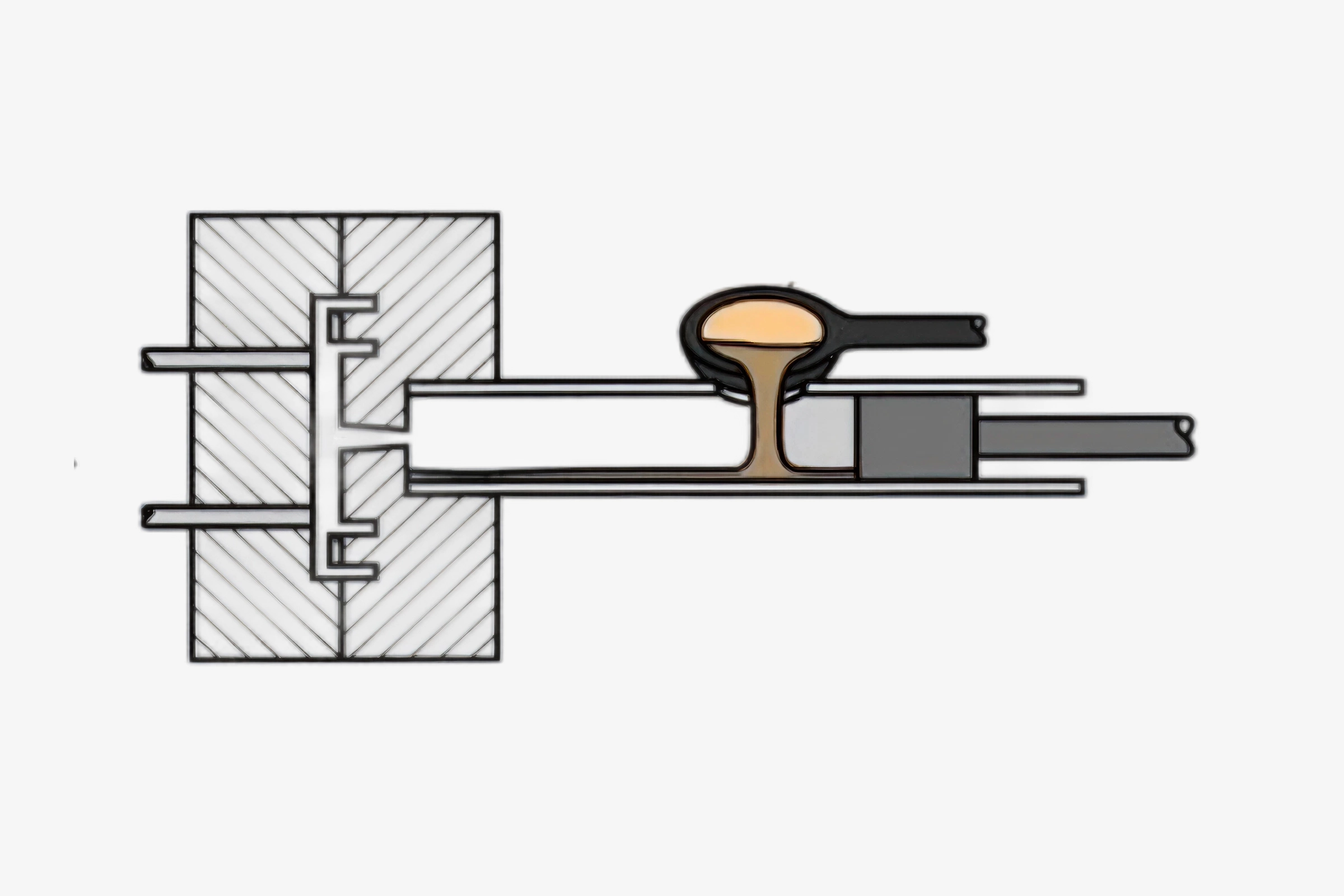
Cold Chamber Die Casting
We also deliver high-precision cold chamber die casting services for aluminum and other high-melting-point alloys. With advanced equipment and tight process control, we produce strong, complex parts with excellent dimensional accuracy—ideal for demanding applications in automotive, aerospace, and beyond.
Our Die Casting Factory
Get High-Precision Die Cast Parts
Unlock durable, high-accuracy die casting solutions tailored to your needs. Request a quote today!
Materials for Die Casting
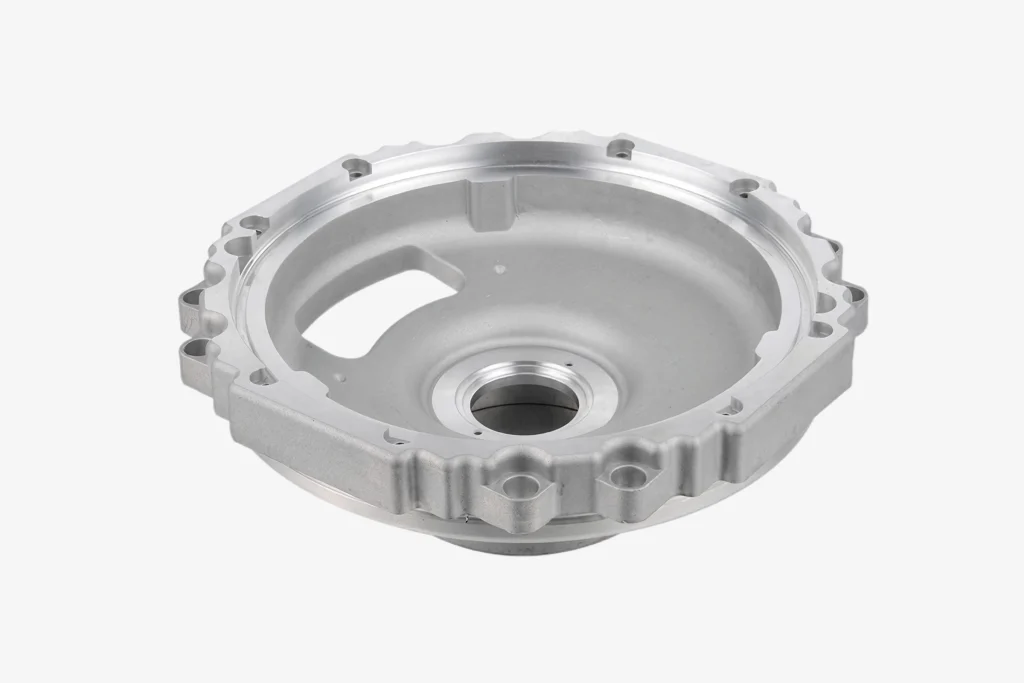
Aluminum
Aluminum’s strength and light weight make it perfect for durable, weight-sensitive automotive and aerospace components.
- Aluminum ADC12
- Aluminum ADC6
- Aluminum A360
- Aluminum A380
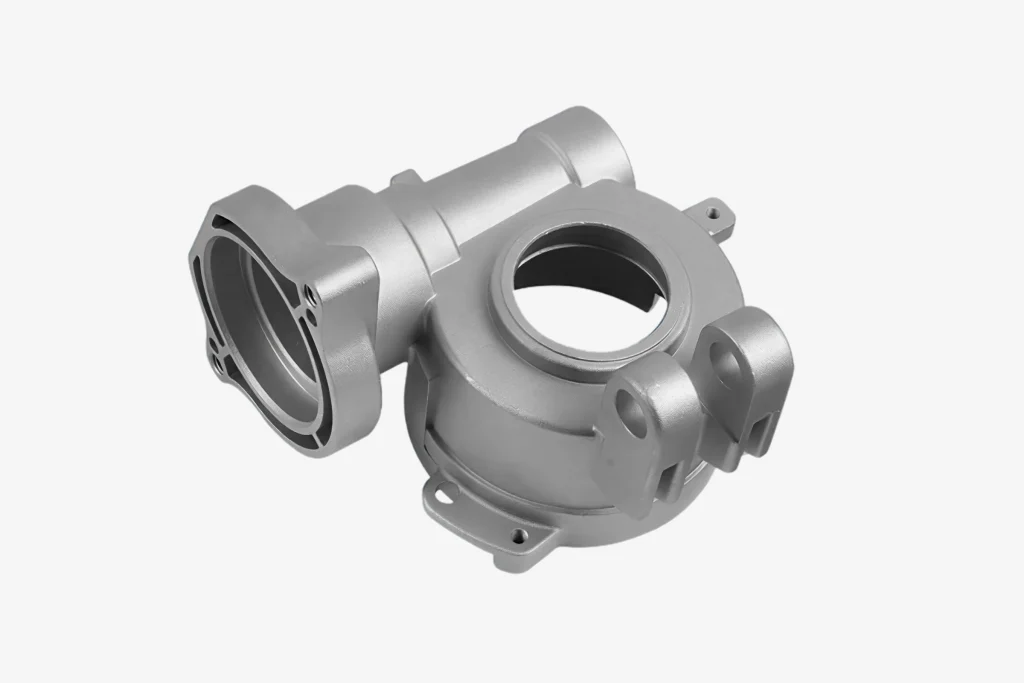
Zinc
Zinc’s toughness allows for high-precision casting, making it ideal for intricate designs and durable parts.
- Zinc Zamak 3
- Zinc Zamak 5
- Zinc Zamak 2
- Zinc ZA8
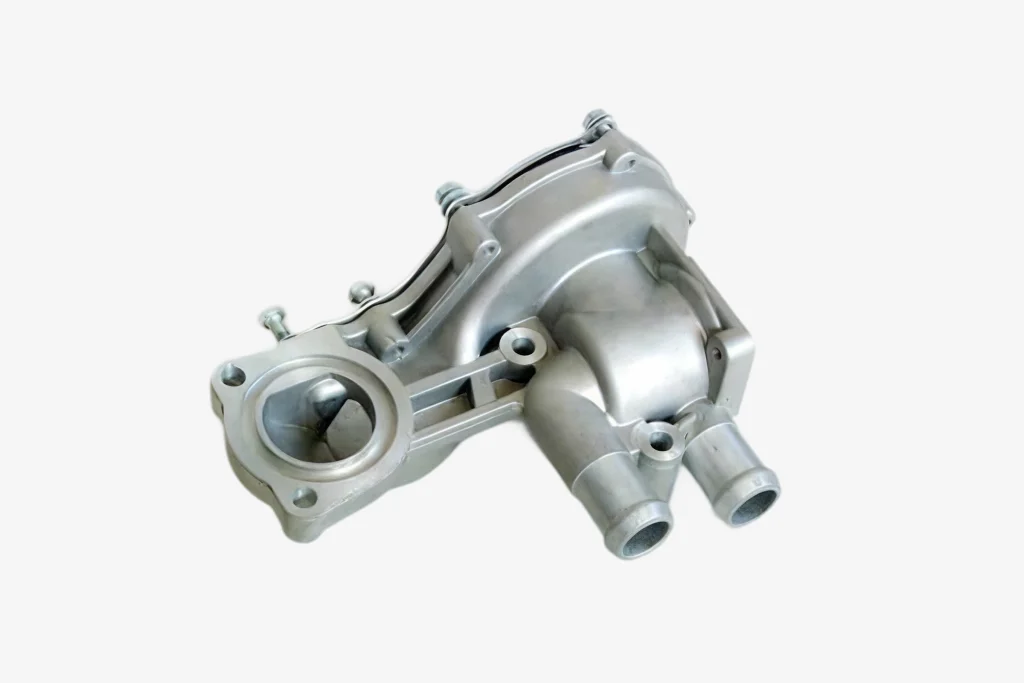
Magnesium
Magnesium, the lightest structural metal, provides a superior stiffness-to-weight ratio, perfect for weight-sensitive applications.
- Magnesium AZ91D
- Magnesium AM60B
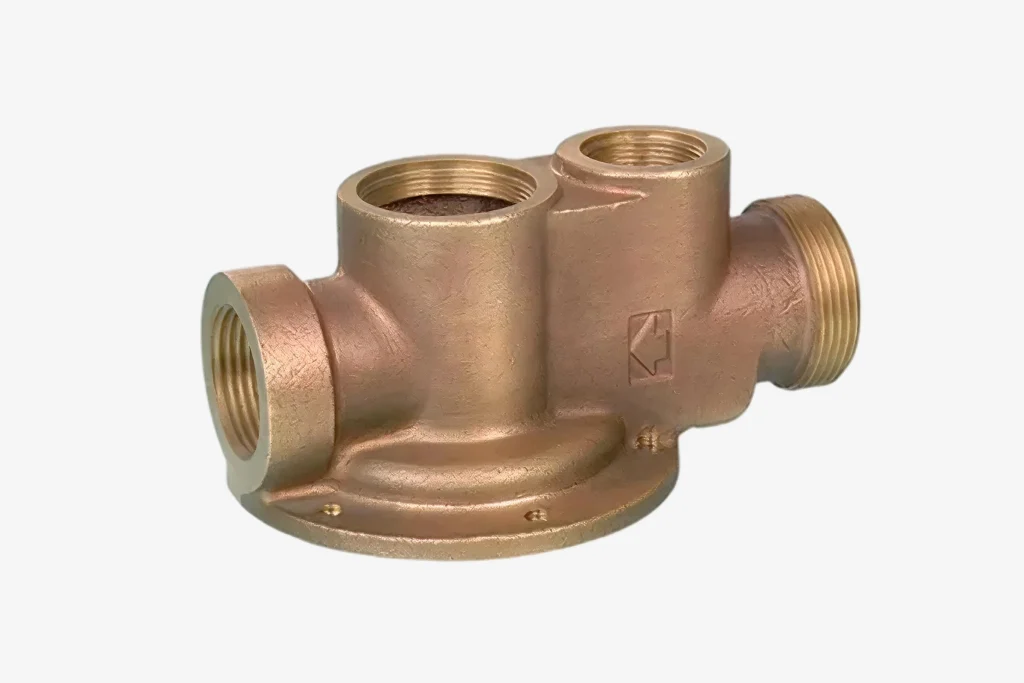
Copper
Copper’s exceptional thermal and electrical conductivity makes it ideal for heat sinks and electrical connectors.
- Copper ZQA19-2
- Copper ZQA19-4
- Copper ZQA19-7
- Copper ZQA19-10
Note: The materials listed above are for reference only. We offer over 100 different materials – please contact us now to find the best option for your needs.
Die Casting Finish Options
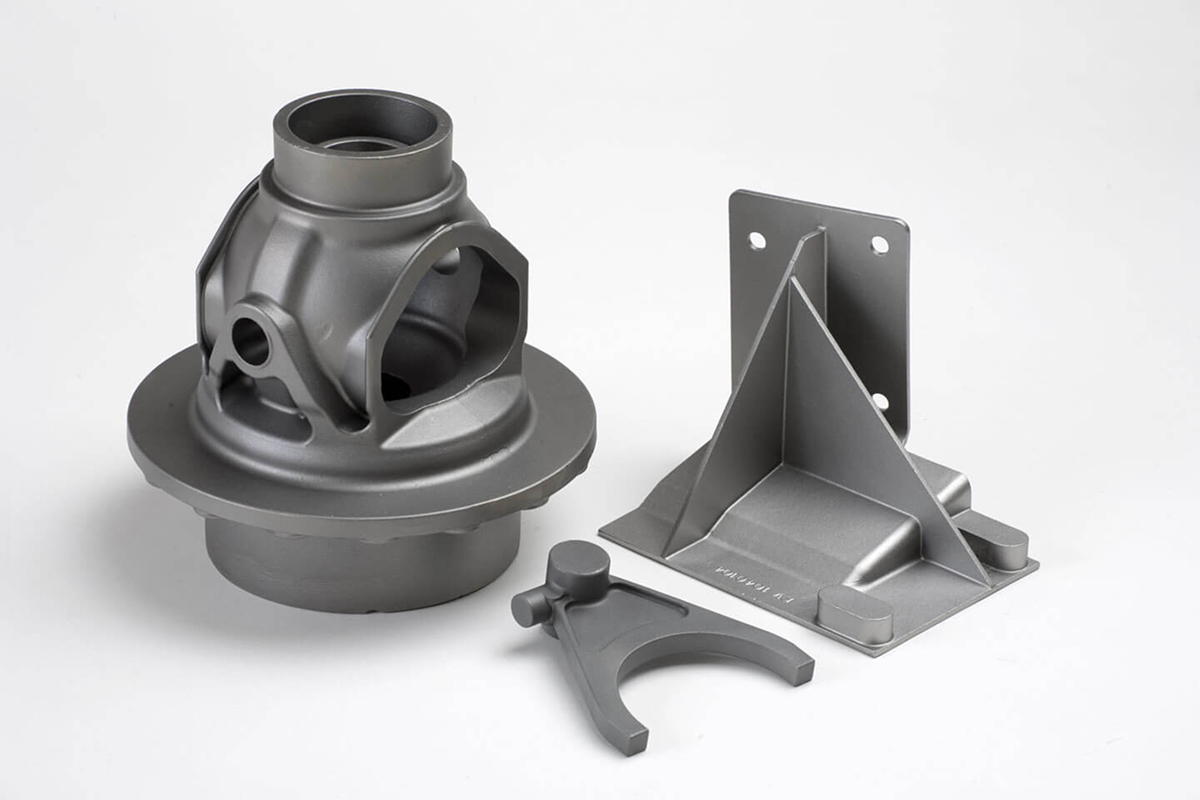
Provides a basic, functional finish with a relatively smooth surface and minor tool marks, making it suitable for non-cosmetic applications.
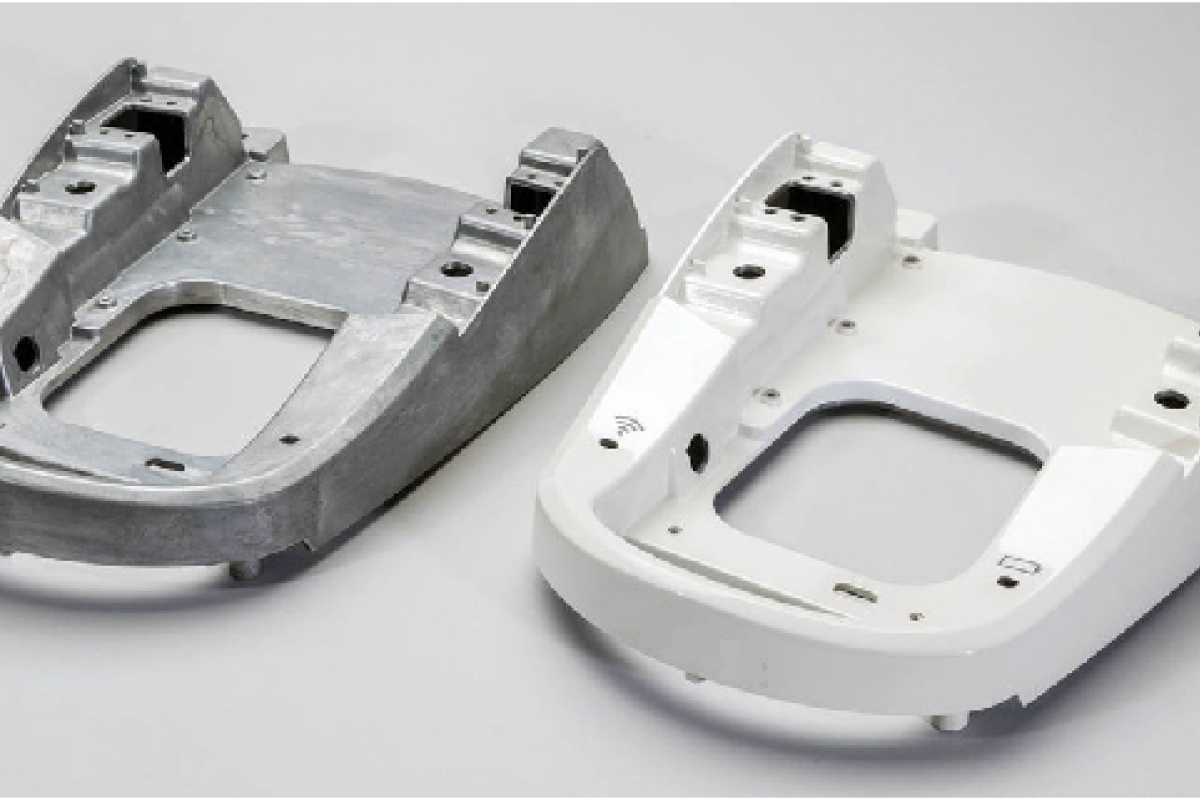
Improves surface smoothness and shine, reducing roughness for a high-gloss, visually appealing finish.
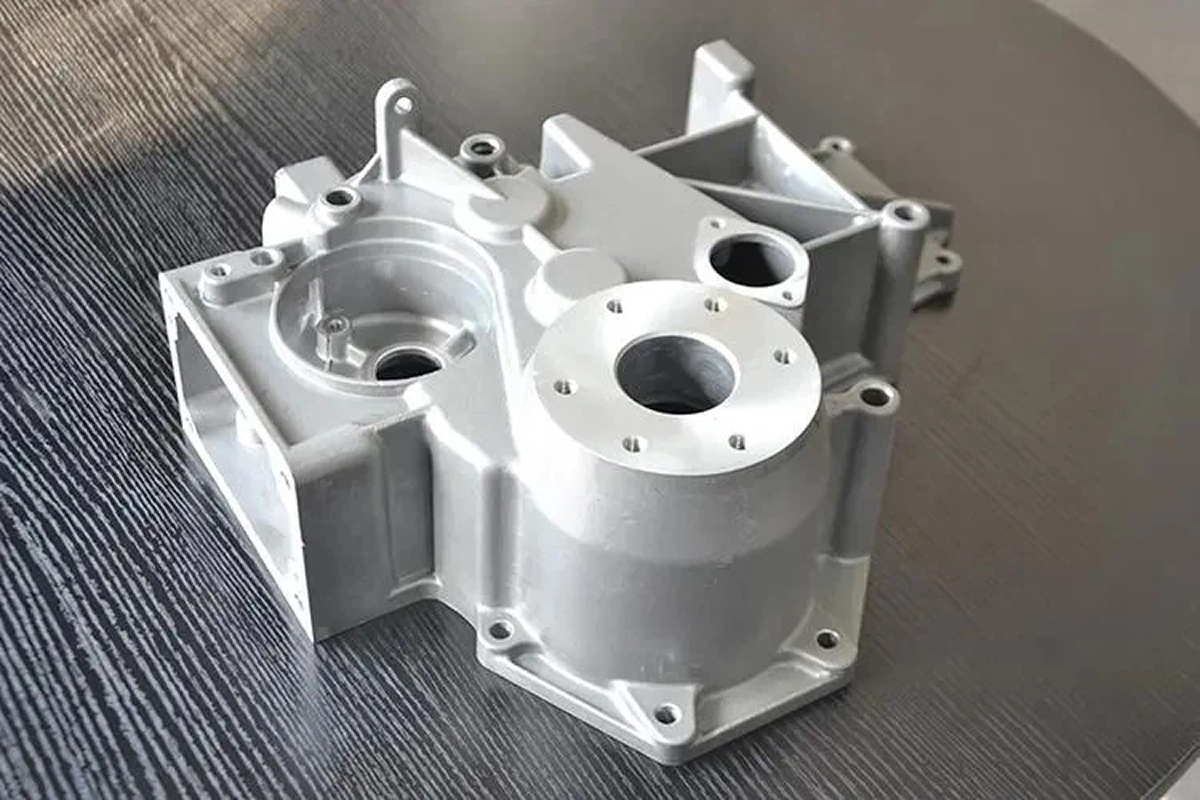
Creates a matte, uniform finish by blasting the surface with fine particles, helping to remove imperfections and prep for further treatments.
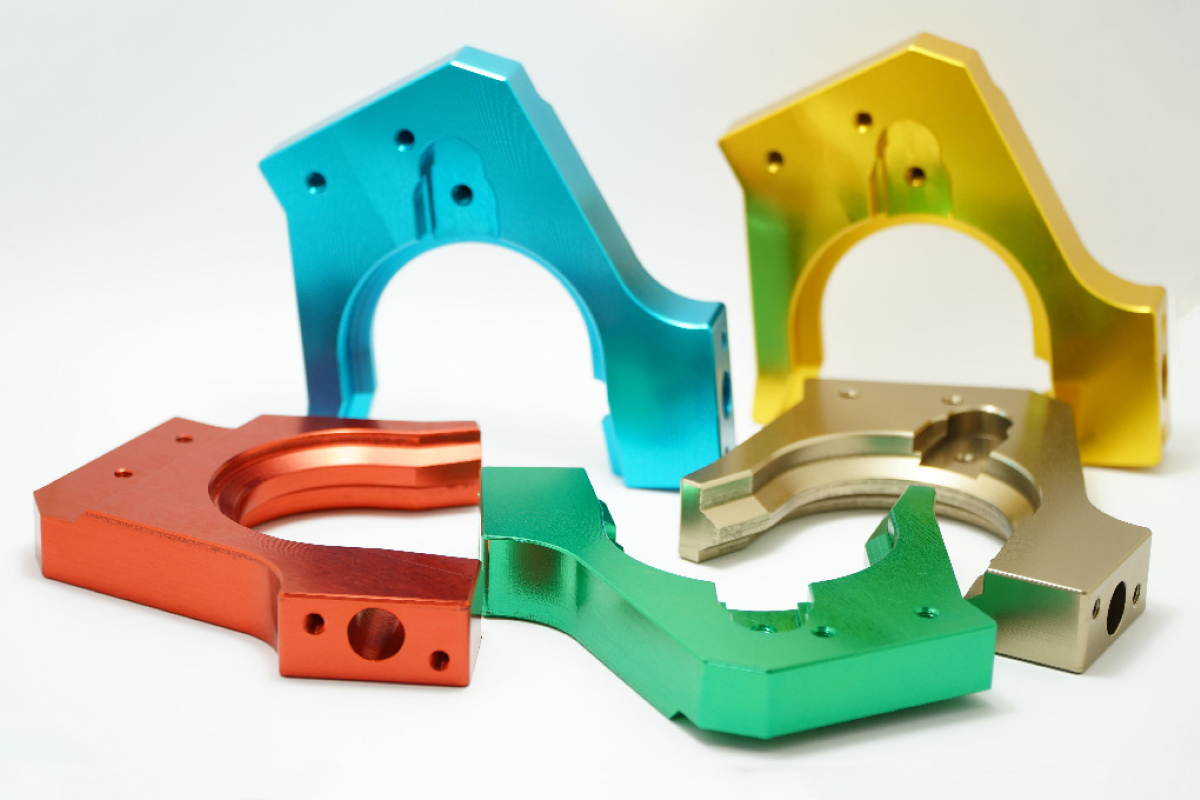
Enhances corrosion resistance and durability of aluminum cast parts while allowing for color customization to improve both function and aesthetics.
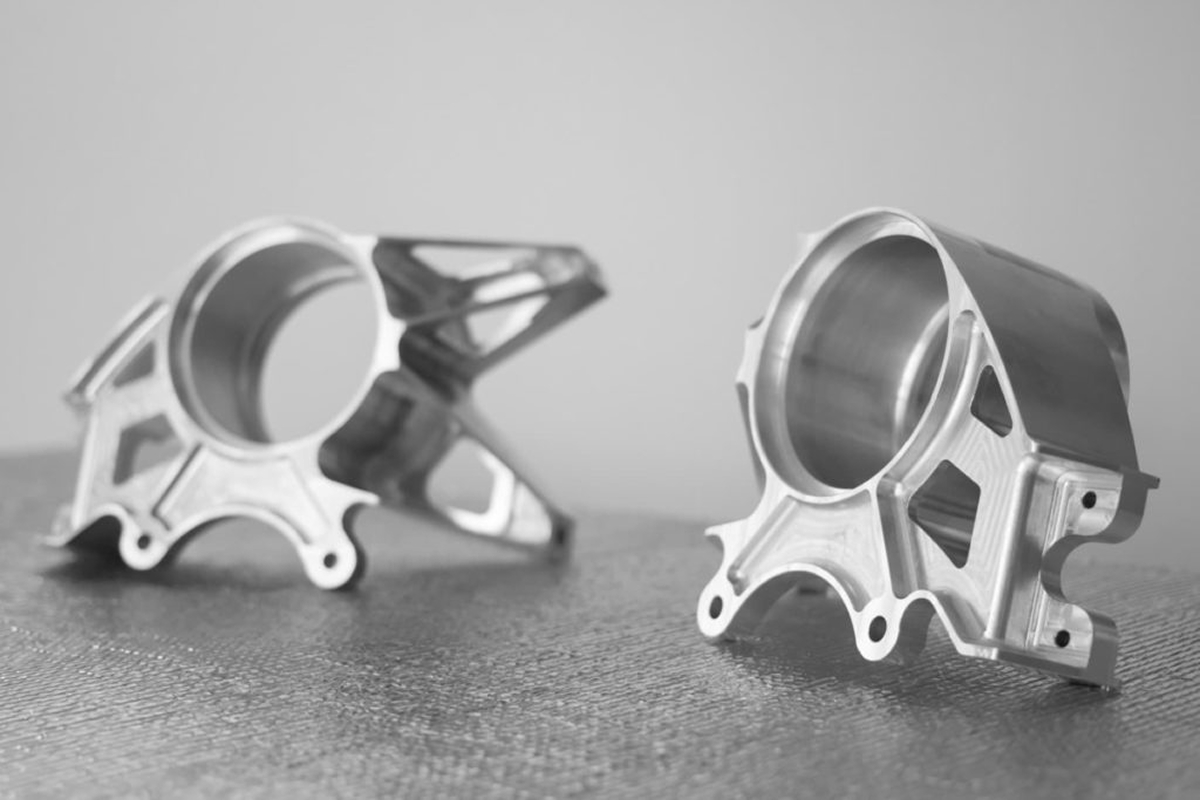
Applies a thick, durable coating that is tougher than traditional paint, providing vibrant colors and extra protection against corrosion and chipping.
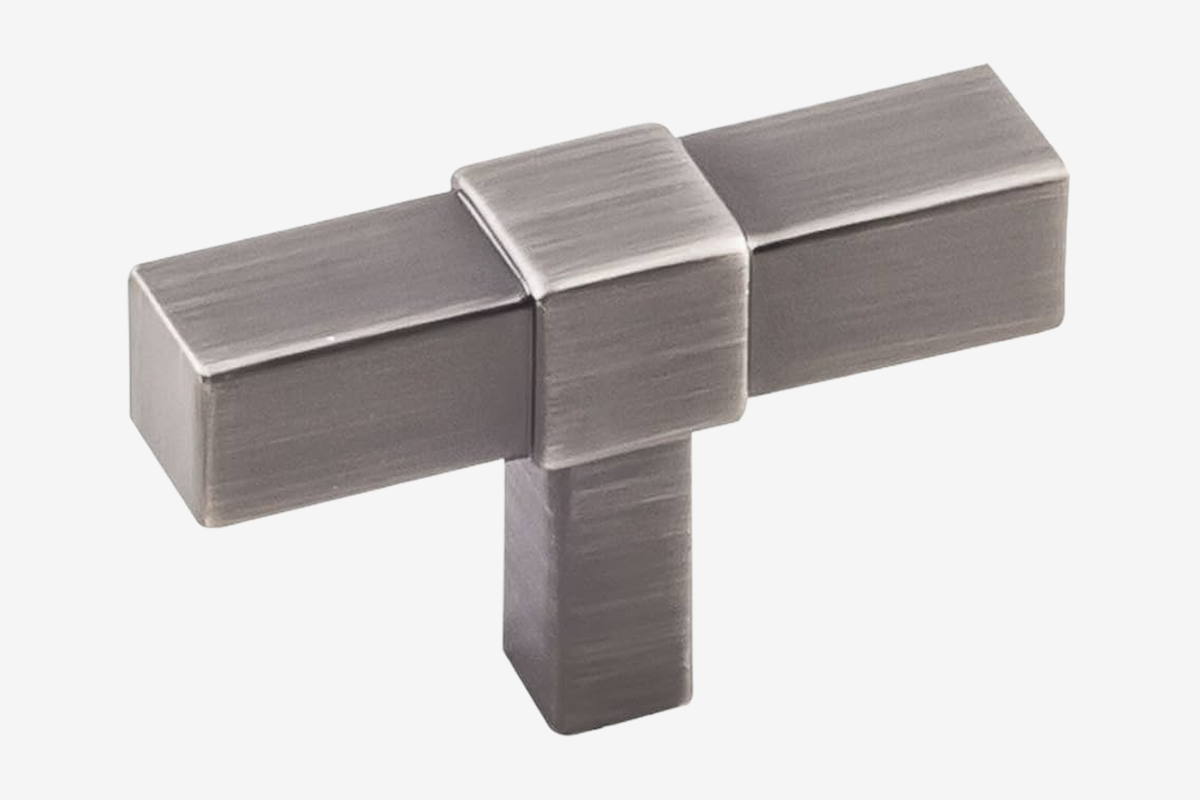
Adds a fine-line texture to the surface, helping to conceal fingerprints and minor scratches, combining style with practicality.
Fast & Reliable Die Casting Services
Need quality cast parts quickly? Our expert team delivers precision and speed. Get started now!
Die Casting Capabilities
Specification | Description |
---|---|
Minimum Part Weight | 0.017 kg |
Maximum Part Weight | 12 kg |
Minimum Part Size | ∅17 mm × 4 mm |
Maximum Part Size | 300 mm × 650 mm |
Minimum Wall Thickness | 0.8 mm |
Maximum Wall Thickness | 12.7 mm |
Quality Control | ISO 9001 Certified |
Minimum Possible Batch | 1000 pcs |
How Does Die Casting Work?
FAQs About Die Casting
Typically 2 to 12 weeks, depending on design complexity, metal choice, and required precision. Molds undergo machining, testing, and adjustments before production.
Standard: ±0.1 mm (≤25 mm), ±0.5 mm (≤250 mm).
High precision: ±0.02 mm with post-machining.
Material properties and advanced techniques like vacuum or squeeze casting impact accuracy.
- Wall Thickness – Keep uniform to prevent defects; thin walls save material but depend on metal and design.
- Draft Angles – Add 1-2° for easy removal.
- Fillets & Radii – Avoid sharp corners to reduce stress and improve flow.
- Gating System – Ensure smooth metal flow to minimize defects.
- Venting – Allow gases to escape to prevent porosity.
- Simplify Geometry – Avoid undercuts and complex features to reduce costs.
- Vacuum Pressure Casting – Vibrations can disrupt the vacuum, causing defects.
- Low Pressure Casting – Unsteady flow due to vibrations affects consistency.
- Semi-Solid Casting – Impacts metal flow and final properties.
- Squeeze Casting – Uneven pressure application may lead to inconsistencies.
Yes, post-machining is often needed for tighter tolerances and smoother finishes. Processes like drilling, milling, and CNC machining refine features, correct defects, and add complex details that casting alone cannot achieve. This combination ensures both cost efficiency and high precision.
Resources
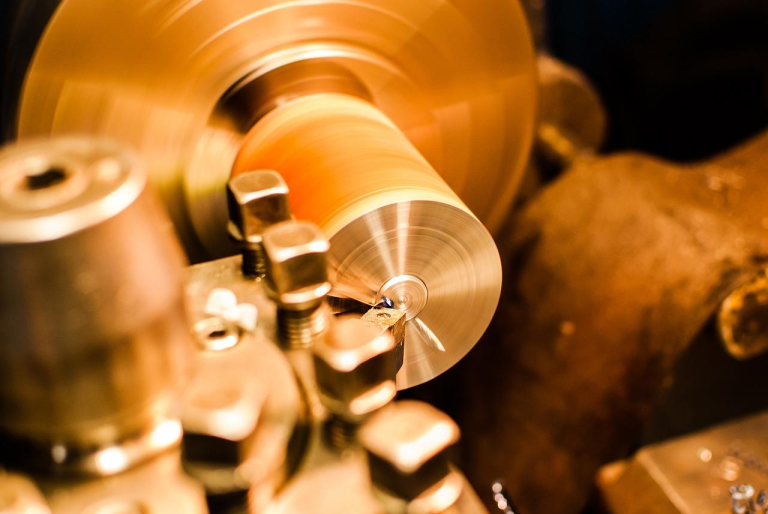
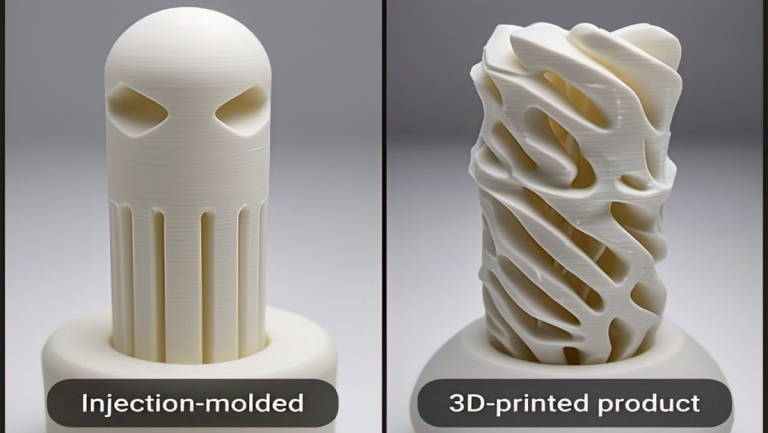